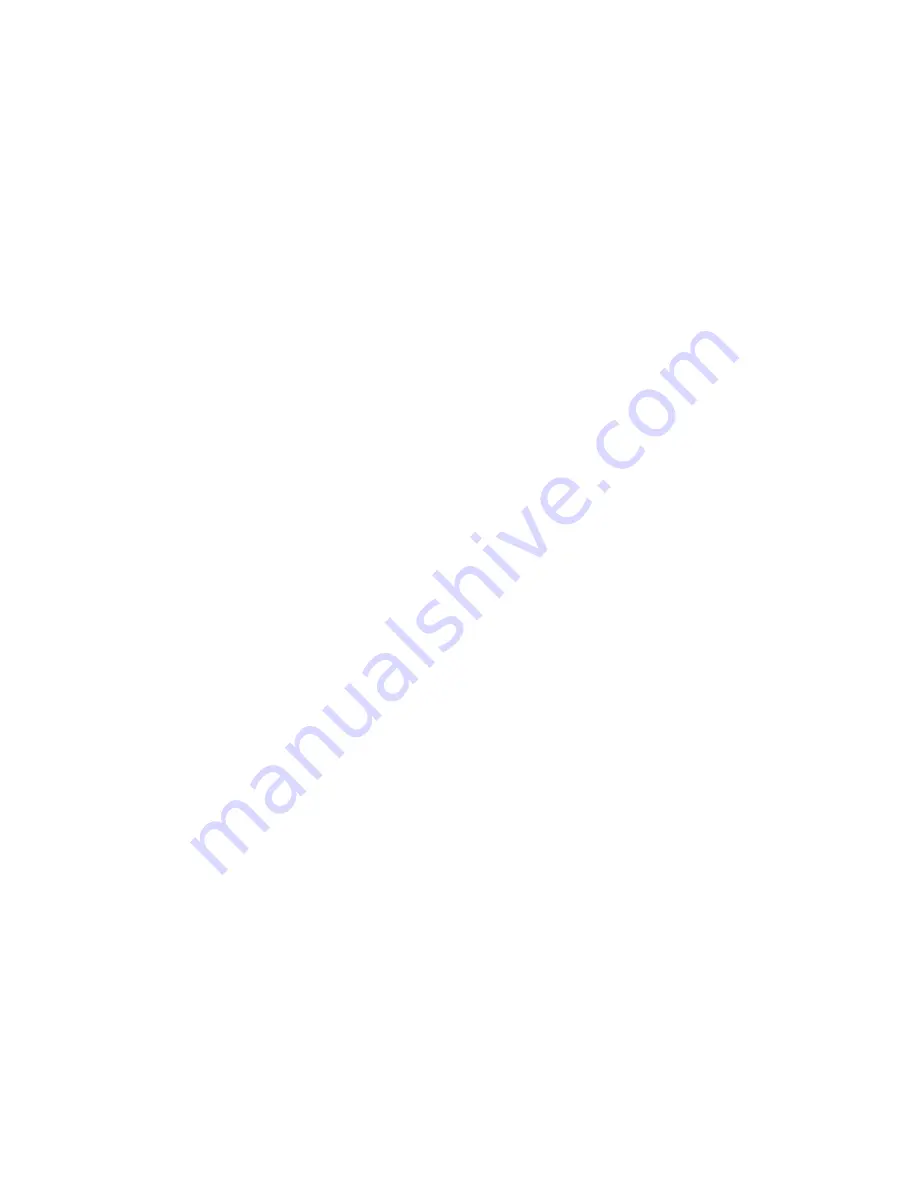
12
3.3 Sensor Installation
Refer to the specific instructions supplied with the sensor being used, for detailed installation instructions.
General Guidelines
Locate the sensors where an active sample of water is available and where the sensors can easily be removed for
cleaning. Position the sensor such that air bubbles will not be trapped within the sensing area. Position the sensor
where sediment or oil will not accumulate within the sensing area.
In-Line Sensor Mounting
In-line mounted sensors must be situated so that the tee is always full and the sensors are never subjected to a
drop in water level resulting in dryness. Refer to Figure 1 for typical installation.
Tap off the discharge side of the recirculation pump to provide a minimum flow of 1 gallon per minute through
the flow switch manifold. The sample must flow into the bottom of the manifold in order to close the flow switch,
and return to a point of lower pressure in order to ensure flow. Install an isolation valve on both sides of the man
-
ifold to stop flow for sensor maintenance.
IMPORTANT: To avoid cracking the female pipe threads on the supplied plumbing parts, use no more than 3
wraps of Teflon tape and thread in the pipe FINGER tight plus 1/2 turn! Do not use pipe dope to seal the threads
of the flow switch because the clear plastic will crack!
Submersion Sensor Mounting
If the sensors are to be submersed in the process, mount them firmly to the tank, and protect the cable with
plastic pipe, sealed at the top with a cable gland, to prevent premature failure. Place the sensors in an area of good
solution movement.
Sensors should be located such that they respond rapidly to a well-mixed sample of the process water and the
treatment chemicals. If they are too close to the chemical injection point, they will see spikes in concentration
and cycle on and off too frequently. If they are too far away from the chemical injection point, they will respond
too slowly to the concentration changes, and you will overshoot the set point.
The
contacting conductivity sensor
should be placed as close to the controller as possible, to a maximum
distance of 250 ft. (76 m). Less than 25 ft. (8 m) is recommended. The cable must be shielded from background
electrical noise. Always route low voltage (sensor) signals with at least a 6” (15 cm) separation from AC voltage wiring.
The
electrodeless conductivity sensor
should be placed as close to the controller as possible, to a maximum
distance of 120 ft. (37 m). Less than 20 ft. (6 m) is recommended. The cable must be shielded from background
electrical noise. Always route low voltage (sensor) signals with at least a 6” (15 cm) separation from AC voltage
wiring. These sensors are affected by the geometry and conductivity of their surroundings, so either maintain 6
inches (15 cm) of sample around the sensor or ensure that any nearby conductive or non-conductive items are
consistently positioned. Do not install the sensor in the path of any electrical current that may be flowing in the
solution, as this will shift the conductivity reading.
The
amplified pH/ORP/ISE electrode
should be placed as close to the controller as possible, to a maximum dis-
tance of 1000 feet (305 m) from the controller. A junction box and shielded cable are available to extend the stan-
dard 20 foot (6 m) length. pH and ORP electrodes must be installed such that the measuring surfaces will always
remain wet. A U-trap provided in the manifold design should achieve this, even if the sample flow stops. These
electrodes also must be installed with the measuring surfaces pointing down; that is 5 degrees above the horizontal,
at a minimum. The flow velocity past the sensor must be less than 10 ft./sec. (3 m/sec.)
The
disinfection sensor
should be placed as close to the controller as possible, to a maximum distance of 100
feet (30 m) from the controller. A junction box and shielded cable are available to extend the standard 20 foot (6
m) length. The sensor should be mounted such that the measuring surfaces will always stay wet. If the membrane
dries out, it will respond slowly to changing disinfectant values for 24 hours, and if dried out repeatedly, will fail
prematurely. The flow cell should be placed on the discharge side of a circulation pump or downhill from a grav
-
ity feed. Flow into the cell must come from the bottom side that has the ¾” x ¼” NPT reducing bushing installed.
The reducing bushing provides the flow velocity required for accurate readings and must not be removed! A “U”
trap should be installed so that if the flow stops, the sensor is still immersed in the water. The outlet of the flow
cell must be plumbed to open atmosphere unless the system pressure is at or below 1 atmosphere. If the flow