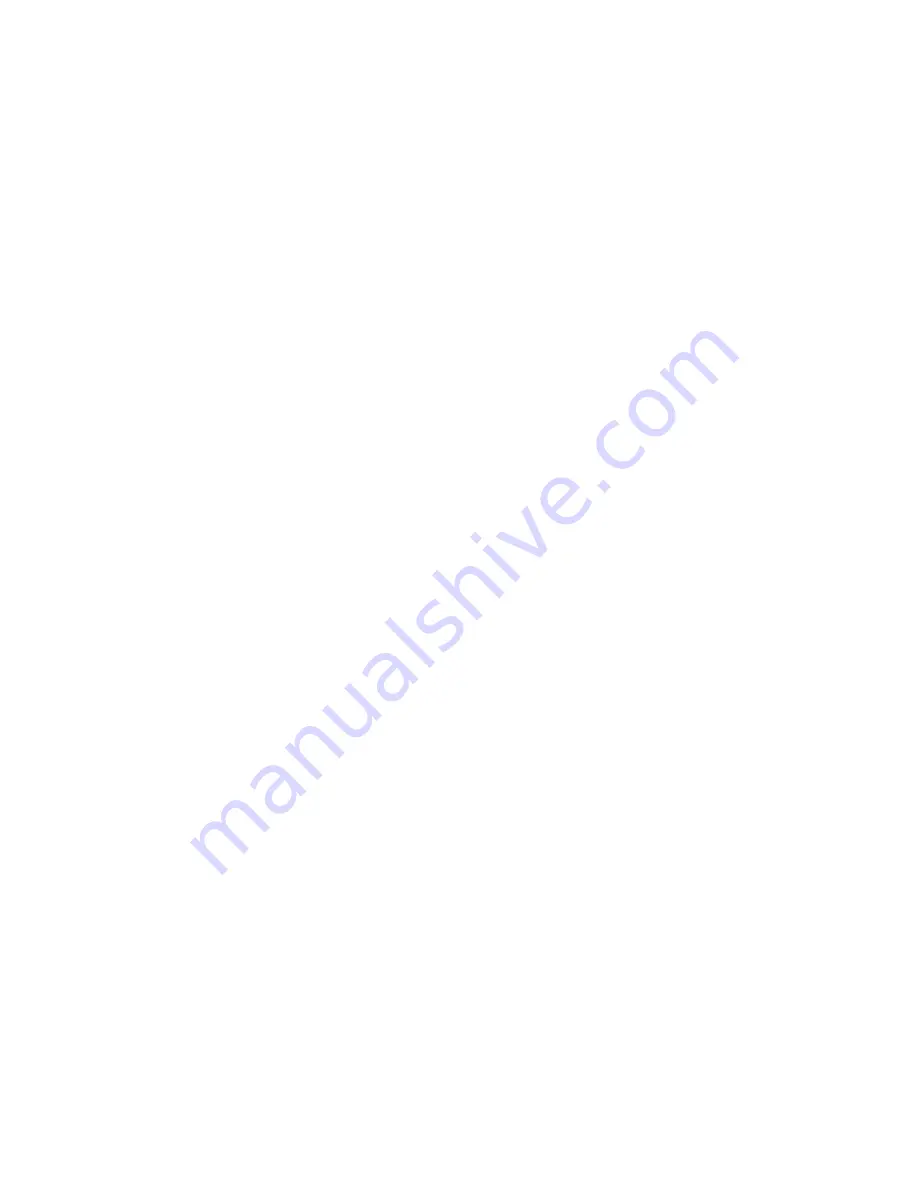
16
through the line cannot be stopped to allow for cleaning and calibration of the sensor, then it should be placed in
a by-pass line with isolation valves to allow for sensor removal. Install the sensor vertically, with the measuring
surface pointing down, at least 5 degrees above horizontal. Flow rate regulation must be done upstream from the
sensor, because any flow restriction downstream can increase the pressure above atmospheric and damage the
membrane cap!
The
corrosion sensor
should be placed as close to the controller as possible, to a maximum distance of 100 feet
(30 m) from the controller. A junction box and shielded cable (p/n 100084) are available to extend the standard
6 foot (3 m) or 20 foot (6 m) length. The sensor should not be installed unless the o-rings/electrodes that match
the metallurgy to be examined are attached to the steel threaded rods. Standard corrosion electrodes are 5 cm2
surface area. Do not touch the metal electrodes; they should be clean and free of any scratches, oils or contami-
nation to accurately measure the corrosion. The sensor should be mounted horizontally, such that the measuring
surfaces will always stay completely wet. The sensor should ideally be installed in the side branch of a 1” or ¾”
tee, with the flow entering the tee through the top branch and flowing away from the base of the sensor, towards
the tips of the electrodes. A constant flow rate is required, at a minimum of 1.5 gpm (5.7 lpm) with an ideal flow
rate of 5 gpm (19 lpm). If more than one metal is to be used, the most noble metal should be first.
Important Boiler Sensor Installation Notes: (refer to typical installation drawing)
1. Make sure the minimum water level in the boiler is at least 4-6 inches above the skimmer blowdown line.
If the skimmer line is closer to the surface, it is likely that steam will be drawn into the line instead of boiler
water. The skimmer line must also be installed above the highest tube.
2.
Maintain a 3/4 inch minimum pipe ID with no flow restrictions from the tap for the boiler skimmer blow
-
down line to the electrode. If the ID is reduced below 3/4 inch, then flashing will occur beyond that point
and the conductivity reading will be low and erratic. Minimize the usage of tees, valves, elbows or unions
between the boiler and the electrode.
3.
A manual shut off valve should be installed so that the electrode can be removed and cleaned. This valve
must be a full port valve in order to avoid a flow restriction.
4. Keep the distance between the tap for the boiler skimmer line to the electrode as short as possible, to a maxi-
mum of 10 feet.
5. Mount the electrode in the side branch of a cross in a horizontal run of pipe. This will minimize entrapment
of steam around the electrode and will allow any solids to pass through.
6.
There MUST be a flow restriction after the electrode and/or control valve in order to provide back pressure.
This flow restriction will be either a flow control valve or an orifice union. The amount of the flow restric
-
tion will affect the blowdown rate as well, and should be sized accordingly.
7. Install the motorized ball valve or solenoid valve per the manufacturer’s instructions.
For best results, align the hole in the conductivity electrode such that the direction of water flow is through the
hole.
Guide to Sizing Blowdown Valves and Orifice Plates
1.
Determine the Rate of Steam Production in Pounds per Hour:
Either read off the boiler name plate (water-tube boilers) or Calculate from horsepower rating (fire-tube
boilers): HP x 34.5 = lbs/hr. Example: 100 HP = 3450 lbs/hr.
2. Determine the Concentration Ratio (BASED ON FEEDWATER)
A water treatment chemical specialist should determine the desired number of cycles of concentration. This
is the ratio of TDS in the boiler water to TDS in the feedwater. Note that feedwater means the water that is
fed to the boiler from the deaerator and includes makeup water plus condensate return. Example: 10 cycles
of concentration has been recommended
3.
Determine the Required Blowdown Rate in Pounds Per Hour
Blowdown Rate = Steam Production / (Concentration Ratio –1) Example: 3450/(10-1) = 383.33 lbs./hr
4. Determine if Continuous or Intermittent Sampling is Required