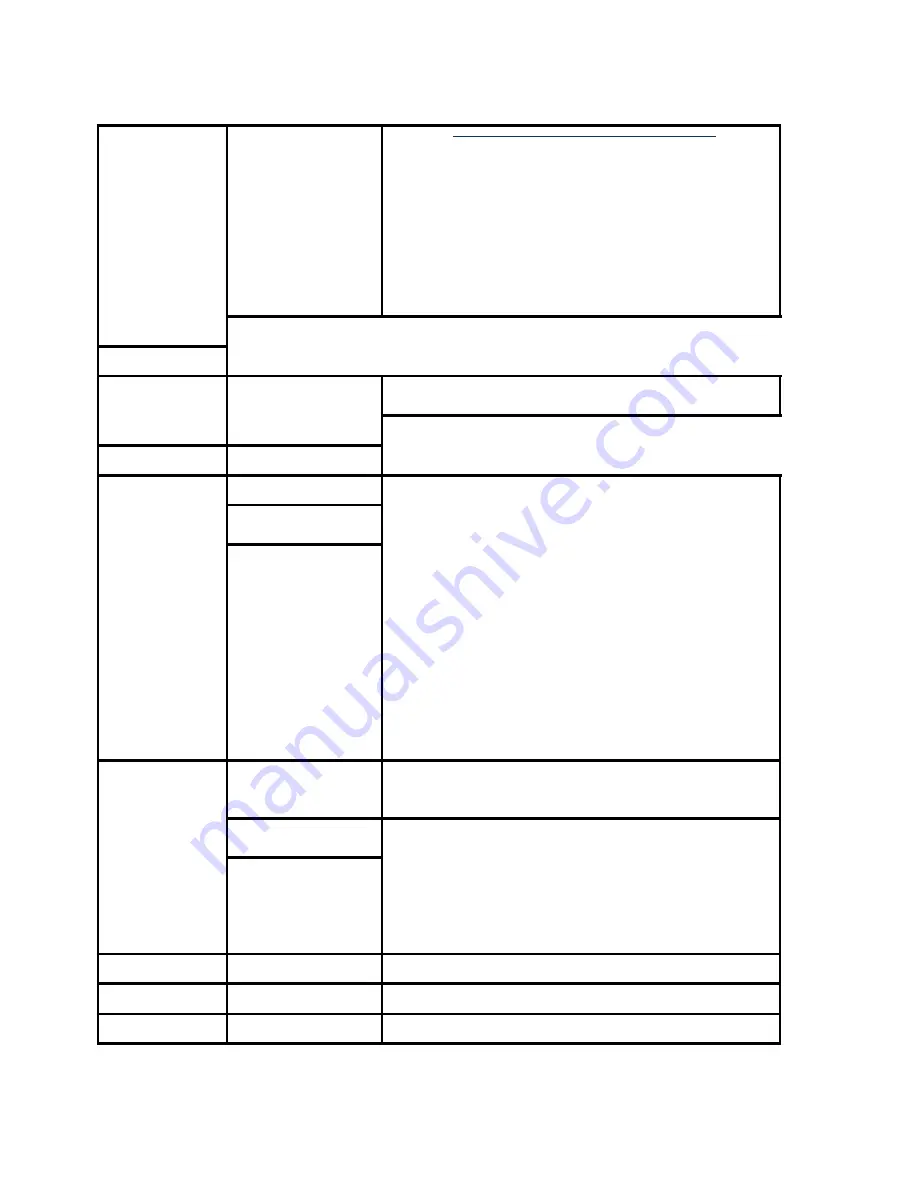
© Precor Incorporated, Unauthorized Reproduction and Distribution Prohibited by Law
Page 18
Note: If power is lost or the unit
is no longer being pedaled
during the rest process, the
update process will be
interrupted, displaying a error 70
(Belt replacement, LPCA not
read). If a error is displayed, the
Stride Count Reset process
must be repeated.
Incline/Crossr
amp
Press the
key
Incline/ Crossramp will be displayed.
Two numbers will be displayed, the percent of lift and
A/D number related to the current lift position. The
A/D (analog to digital) number represents the lift
potentiometer reading. The A/ D number will be in
the range of 0 to 255 or 0 to 32769.
The lift may be operated using the
INCLINE/CROSSRAMP
keys. The incline
percentage and A/D numbers will change
accordingly. Care must be taken while operating the
lift in this mode because the normal upper and lower
range limits are not in effect. It is possible to operate
the lift to its physical limits and may cause the lift
motor to jam.
Press the
OK
key
Press the
CLEAR
key to return to
Hardware
Validation
Auto Stop
(Treadmill
Only)
Press the
key
User Detected or User Not Detected will be
displayed.
Press the
OK
key
A magnet is attached to the running deck and a
sensor is attached to the frame. If the sensor detects
motion from the running deck, User Detected will be
displayed. If the sensor does not detect motion from
the running deck, User Not Detected will be
displayed.
Press the
CLEAR
key to return to
Hardware
Validation
Summary of Contents for AMT 823
Page 2: ......
Page 61: ...Precor Incorporated Unauthorized Reproduction and Distribution Prohibited by Law Page 59...
Page 81: ...Precor Incorporated Unauthorized Reproduction and Distribution Prohibited by Law Page 79...
Page 107: ...Precor Incorporated Unauthorized Reproduction and Distribution Prohibited by Law Page 105...
Page 199: ...Precor Incorporated Unauthorized Reproduction and Distribution Prohibited by Law Page 197...
Page 379: ...rfJ R BK BR Bl 0 d I w l 0 1 LO iftMotor...
Page 380: ......
Page 382: ......