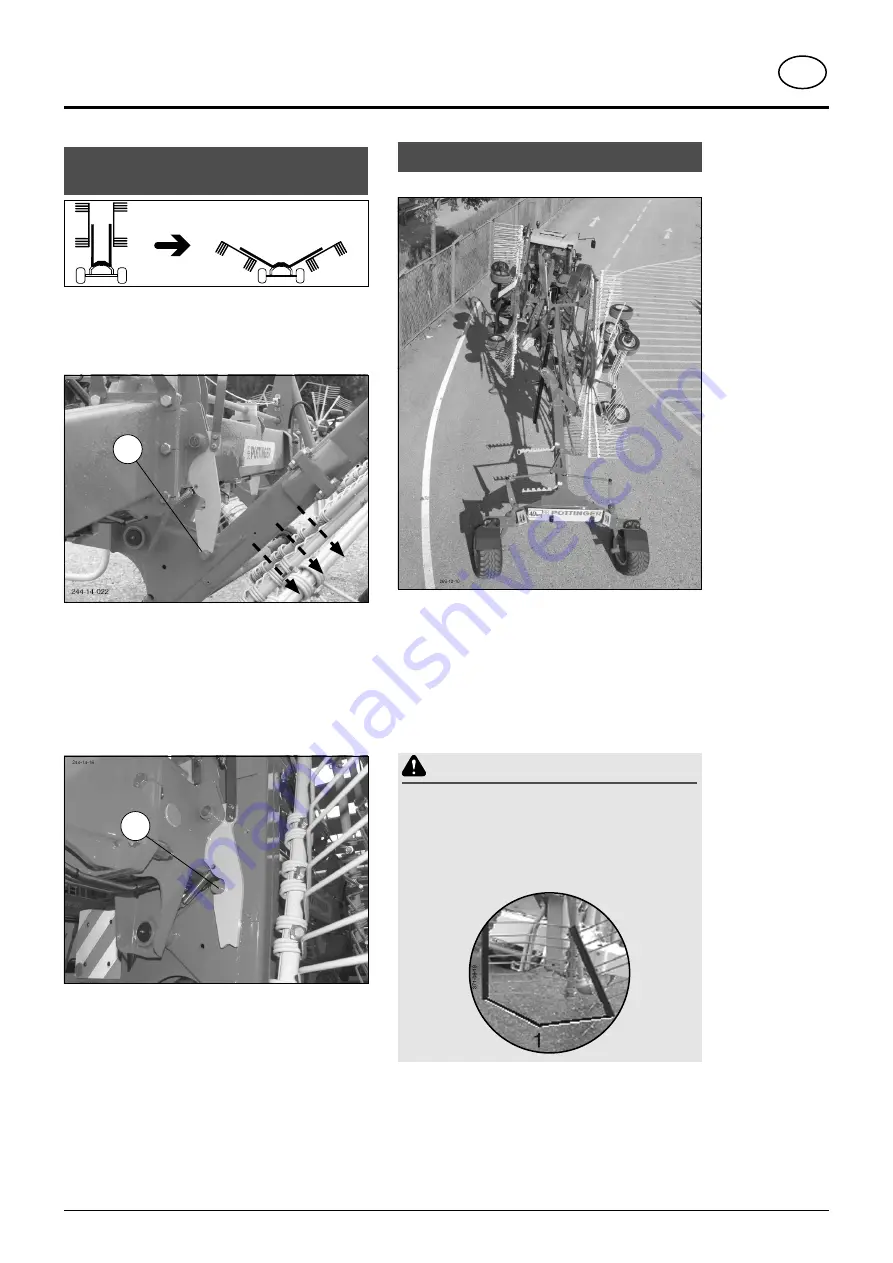
EN
TransporT
1700_EN-TRANSPORT_2860
- 18 -
Changing from headland to transport
position
075-09-39
1. lifting the rotors
- use the single-action control unit to lower the rotor arm
until the transport securing device (1) can be released.
1
- Release the transport securing device by pulling the
rope and holding.
- Raise the rotors into transport position with the single-
action control unit
- Release rope to allow transport securing device to lock
in place
- Check correct locking of the transport securing device
(2) at both rotors.
2
Driving on public roads
• Only transport the machine in the transport position!
• Observe the statutory regulations for your country.
• Driving on public roads may only be carried out as
described in chapter “Transport position”.
• Safety devices must be in proper condition.
• Before driving off, bring swivelling parts to correct
position and secure against dangerous position
changes.
• Check that the lighting functions before driving off.
WARNING
Risk of serious injury from protruding tines in
transport position.
•
Put the protective strips (1) onto the tines
before lifting the rotor arms into transport
position.
Hydraulic lower link
• Secure the hydraulic lower link (U) so that machine
cannot swing out sideways.