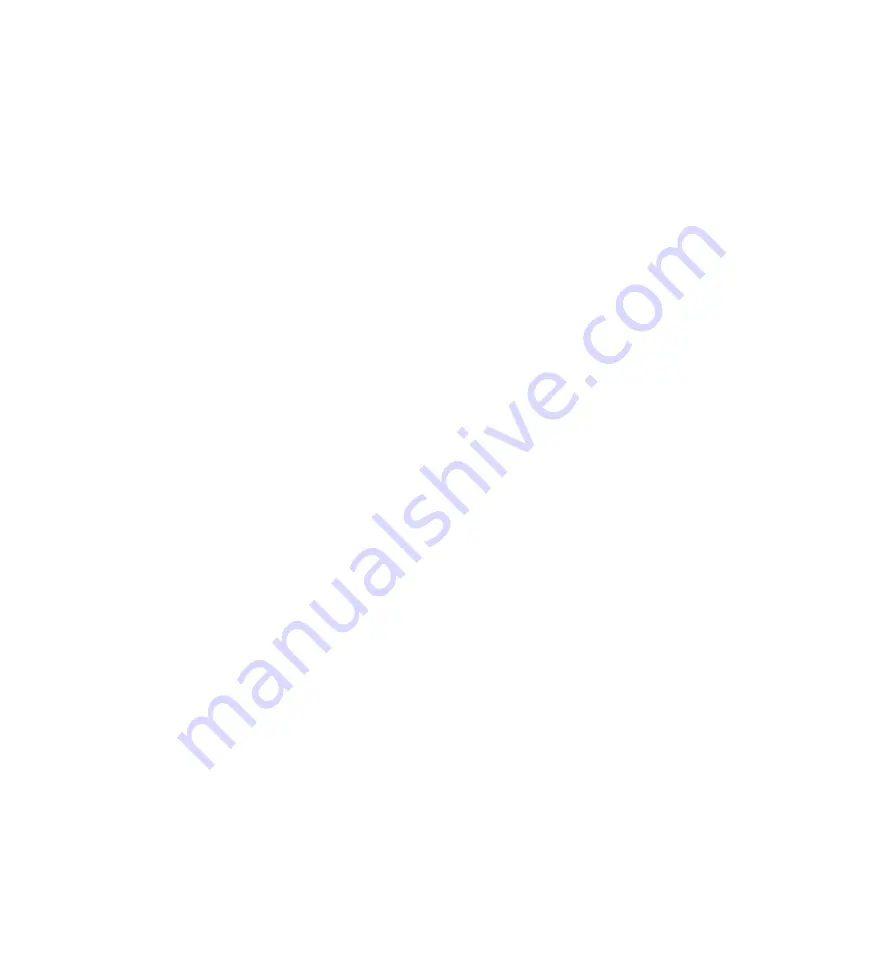
Preparing Your Laboratory
59
is used, a stronger blower may be necessary to provide sufficient exhaust volume.
Alternatively, smooth stainless-steel may be used instead of flexible stainless-steel
where flexibility is not required to reduce system friction loss or “drag.” If smooth
stainless steel is used, there must be a way to move the vent hood out of the way for
servicing. A length of smooth stainless-steel ducting has 20-30% less friction loss
than a comparable length of flexible ducting. When smooth stainless-steel is used,
elbows must be used to turn corners. These elbows should turn at a center line radius
of 150 mm with a maximum bend angle of 45 degrees to reduce friction losses, and
the number of elbows should be minimized.
Additional recommendations on the venting system include:
•
Make sure duct casing is installed using fireproof construction. Route ducts
away from sprinkler heads.
•
Locate the blower as close to the discharge outlet as possible. All joints on the
discharge side should be airtight, especially if toxic vapors are being carried.
•
Equip the outlet end of the system with a back draft damper and take the
necessary precautions to keep the exhaust outlet away from open windows or
inlet vents and to extend it above the roof of the building for proper dispersal of
the exhaust.
•
Equip the exhaust end of the system with an exhaust stack to improve the overall
efficiency of the system.
•
Make sure the length of the duct that enters into the blower is a straight length at
least ten times the duct diameter. An elbow entrance into the blower inlet causes
a loss in efficiency.
•
Provide make-up air in the same quantity as is exhausted by the system. An
"airtight" lab will cause an efficiency loss in the exhaust system.
•
Ensure that the system is drawing properly by using an air flow meter.
•
Equip the blower with a pilot light located near the instrument to indicate to the
operator when the blower is on.
Summary of Contents for AVIO 200
Page 1: ...AVIO 200 SPECTROMETER Hardware Guide ICP OPTICAL EMISSION ...
Page 2: ......
Page 3: ...AvioTM 200 Spectrometer Customer Hardware and Service Guide ...
Page 12: ...Contents 10 ...
Page 30: ...28 ...
Page 31: ...Safety Practices 1 ...
Page 32: ...30 Safety Practices ...
Page 56: ...54 Safety Practices ...
Page 57: ...Preparing Your Laboratory 2 ...
Page 58: ...Preparing Your Laboratory 56 ...
Page 70: ...Preparing Your Laboratory 68 ...
Page 71: ...System Description 3 ...
Page 72: ......
Page 97: ...Installation 4 ...
Page 98: ......
Page 119: ...Installation 117 Figure 4 8 Replacing the torch 1 3 4 6 8 2 9 10 5 7 ...
Page 121: ...Installation 119 1 2 7 9 8 10 3 4 5 6 ...
Page 164: ...Installation 162 ...
Page 165: ...Maintenance 5 ...
Page 166: ......
Page 184: ...Maintenance 182 1 2 7 9 8 10 3 4 5 6 ...
Page 188: ...Maintenance 186 Figure 5 8 Replacing the Torch 1 3 4 6 8 2 9 10 5 7 ...
Page 272: ...Maintenance 270 ...
Page 273: ...Troubleshooting 6 ...
Page 274: ......
Page 293: ...Troubleshooting 291 Figure 6 1 Normal Plasma Conditions at 0 torch position ...
Page 294: ...Troubleshooting 292 Figure 6 2 Normal Plasma at 3mm position ...
Page 297: ...Troubleshooting 295 Figure 6 5 Injector too far forward ...
Page 298: ...Troubleshooting 296 Figure 6 6 No Aux Gas Torch may be glowing ...
Page 299: ...Troubleshooting 297 Figure 6 7 Air Leak or Spray Chamber Temperature too high ...
Page 300: ...Troubleshooting 298 Figure 6 8 Thin Plasma due to leak in Plasma Gas Line ...
Page 308: ......