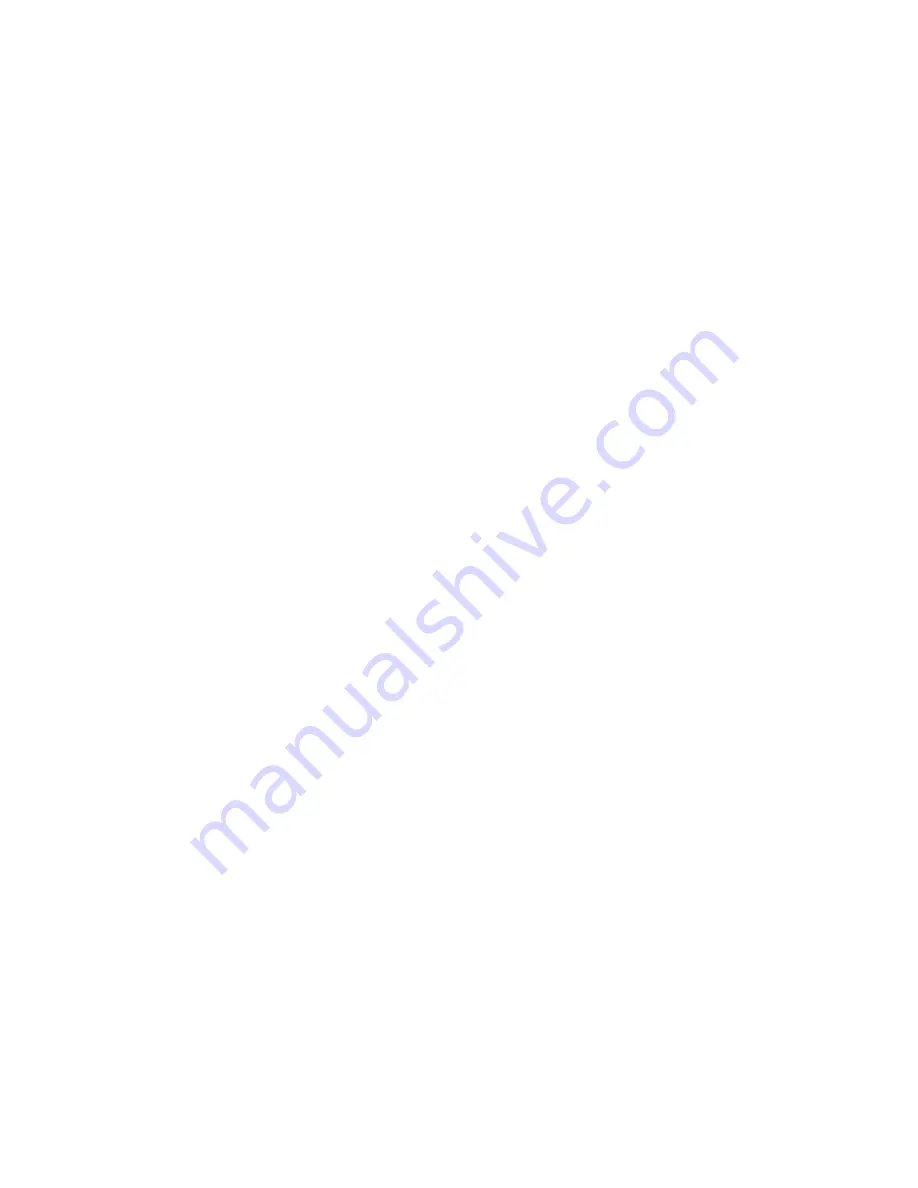
Installation
105
Connecting the Chiller to the Instrument
Teflon tape (PTFE tape) should be used for all pipe-thread (NPT) fittings.
Use of Teflon tape can prevent leaks.
Connect the instrument to the chiller inlet using coolant drain hose. The direction of
the flow through the system can be controlled by the way the hoses are connected to
the chiller. The "INLET" port will draw liquid into the chiller; the “OUTLET" port
will pump liquid out. See the following figure for the location of the cables.
1. Locate the instrument return/Output coolant line (Part No. N0770342) and
connect to the chiller "INLET" fitting. The instrument water outputs have a
fitting and tubing to connect them to the return or drain. Use 3/8-in. space collars
(Part No. 09920584) at the instrument. The following figure shows the water
supply connections at the instrument.
2. Locate the instrument Input coolant lines (Part No. N0770341), which uses 3/8-
in Swagelock fittings) and connect to the chiller “OUTLET” fitting. Use a 3/8-
in. space collars (Part No. 09920584) at the instrument. The following figure
shows the chiller connections.
shows the water supply
connections at the instrument.
3. Make sure that the hoses and fittings are tight and that there are no bends or
crimps in the hoses.
Remote Chiller Connections
The chiller can be turned on or off via the software. Your service engineer will
connect the remote cable (Part No. N0770175) from the chiller to the Avio 200 so
that the chiller can be operated remotely. To make sure that the chiller can be
operated remotely the red wire must be connected to position 9 and the black wire
connected to position 11. See the following two figure for the location of the cable
connections.
Summary of Contents for AVIO 200
Page 1: ...AVIO 200 SPECTROMETER Hardware Guide ICP OPTICAL EMISSION ...
Page 2: ......
Page 3: ...AvioTM 200 Spectrometer Customer Hardware and Service Guide ...
Page 12: ...Contents 10 ...
Page 30: ...28 ...
Page 31: ...Safety Practices 1 ...
Page 32: ...30 Safety Practices ...
Page 56: ...54 Safety Practices ...
Page 57: ...Preparing Your Laboratory 2 ...
Page 58: ...Preparing Your Laboratory 56 ...
Page 70: ...Preparing Your Laboratory 68 ...
Page 71: ...System Description 3 ...
Page 72: ......
Page 97: ...Installation 4 ...
Page 98: ......
Page 119: ...Installation 117 Figure 4 8 Replacing the torch 1 3 4 6 8 2 9 10 5 7 ...
Page 121: ...Installation 119 1 2 7 9 8 10 3 4 5 6 ...
Page 164: ...Installation 162 ...
Page 165: ...Maintenance 5 ...
Page 166: ......
Page 184: ...Maintenance 182 1 2 7 9 8 10 3 4 5 6 ...
Page 188: ...Maintenance 186 Figure 5 8 Replacing the Torch 1 3 4 6 8 2 9 10 5 7 ...
Page 272: ...Maintenance 270 ...
Page 273: ...Troubleshooting 6 ...
Page 274: ......
Page 293: ...Troubleshooting 291 Figure 6 1 Normal Plasma Conditions at 0 torch position ...
Page 294: ...Troubleshooting 292 Figure 6 2 Normal Plasma at 3mm position ...
Page 297: ...Troubleshooting 295 Figure 6 5 Injector too far forward ...
Page 298: ...Troubleshooting 296 Figure 6 6 No Aux Gas Torch may be glowing ...
Page 299: ...Troubleshooting 297 Figure 6 7 Air Leak or Spray Chamber Temperature too high ...
Page 300: ...Troubleshooting 298 Figure 6 8 Thin Plasma due to leak in Plasma Gas Line ...
Page 308: ......