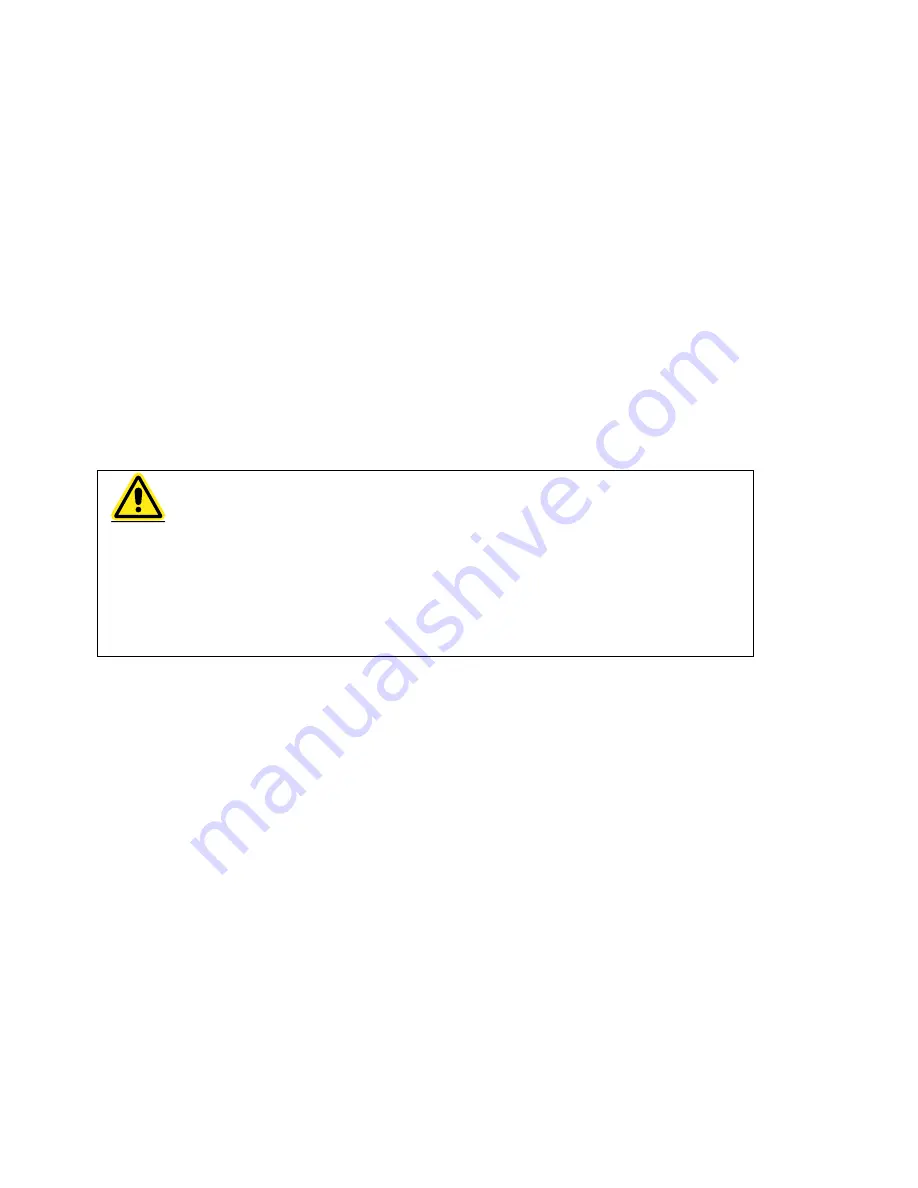
Installation
103
1. Install the Air Dryer Filter as described in the instructions that are included with
the filter.
2. Locate the air hose (Part No. N0770348, which uses 1/4-in. Swagelok fittings at
each end). Connect the air hose from the air compressor to the AIR IN fitting on
the Air Dryer Filter using a 1/4-in. space collar at both ends. Make sure the air
flow is in the proper direction, as indicated by arrows on top of the filters.
3. Locate the second air hose (Part No. N0770348, uses 1/4-in. Swagelok fittings
at each end) that is shipped with the instrument in the hose kit. Connect the air
hose from the AIR OUT fitting on the Air Dryer Filter using a 1/4-in. space
collar at both ends.
Setting the Shear Gas
Pressure
The following procedure describes how to set the shear gas pressure when using the
PerkinElmer Air Dryer Filter.
1. Make sure the shut-off valve on the Air Dryer Filter is closed (knob turned fully
clockwise), then set the air pressure on the air compressor to between 550 kPa
and 825 kPa (5.5 to 8.25 bar or 80-120 psig).
2. Check that the metal covers are in position on the filter bowls and the filter bowl
holding rings are properly locked.
Do not set the air compressor pressure higher than 690 kPa (100 psig). The
maximum pressure and temperature that the filter bowls can withstand is 1035
kPa (150 psig) at 50 °C (125 °F). At a higher pressure, the filter bowls can be
blown off and cause injury.
Avertissement: Ne pas régler la pression du compresseur d'air supérieure à 690
kPa (100 psig). La pression et la température maximale que les cuvettes de filtre
peut supporter est de 1035 kPa (150 psi) à 50 ° C (125 ° F). Lors d'une pression
plus élevée, les bols de filtre peuvent être arrachés et causer des blessures.
!
Warning
Summary of Contents for AVIO 200
Page 1: ...AVIO 200 SPECTROMETER Hardware Guide ICP OPTICAL EMISSION ...
Page 2: ......
Page 3: ...AvioTM 200 Spectrometer Customer Hardware and Service Guide ...
Page 12: ...Contents 10 ...
Page 30: ...28 ...
Page 31: ...Safety Practices 1 ...
Page 32: ...30 Safety Practices ...
Page 56: ...54 Safety Practices ...
Page 57: ...Preparing Your Laboratory 2 ...
Page 58: ...Preparing Your Laboratory 56 ...
Page 70: ...Preparing Your Laboratory 68 ...
Page 71: ...System Description 3 ...
Page 72: ......
Page 97: ...Installation 4 ...
Page 98: ......
Page 119: ...Installation 117 Figure 4 8 Replacing the torch 1 3 4 6 8 2 9 10 5 7 ...
Page 121: ...Installation 119 1 2 7 9 8 10 3 4 5 6 ...
Page 164: ...Installation 162 ...
Page 165: ...Maintenance 5 ...
Page 166: ......
Page 184: ...Maintenance 182 1 2 7 9 8 10 3 4 5 6 ...
Page 188: ...Maintenance 186 Figure 5 8 Replacing the Torch 1 3 4 6 8 2 9 10 5 7 ...
Page 272: ...Maintenance 270 ...
Page 273: ...Troubleshooting 6 ...
Page 274: ......
Page 293: ...Troubleshooting 291 Figure 6 1 Normal Plasma Conditions at 0 torch position ...
Page 294: ...Troubleshooting 292 Figure 6 2 Normal Plasma at 3mm position ...
Page 297: ...Troubleshooting 295 Figure 6 5 Injector too far forward ...
Page 298: ...Troubleshooting 296 Figure 6 6 No Aux Gas Torch may be glowing ...
Page 299: ...Troubleshooting 297 Figure 6 7 Air Leak or Spray Chamber Temperature too high ...
Page 300: ...Troubleshooting 298 Figure 6 8 Thin Plasma due to leak in Plasma Gas Line ...
Page 308: ......