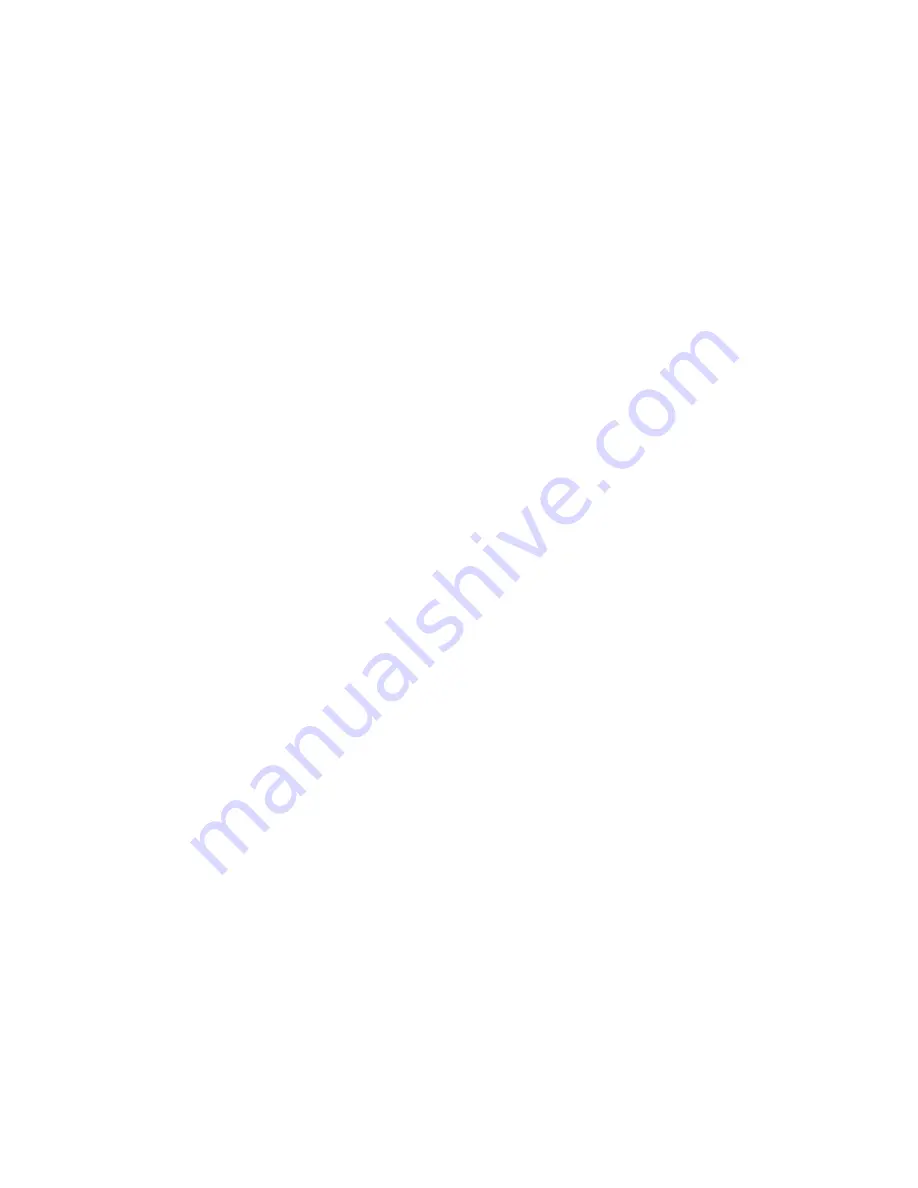
Safety Guidelines for the Application, Installation and Maintenance of Solid State Control
E116P
12
3.4.3 Design of Wiring for Maximum Protection
Once the installation site and power conductors have
been examined, the system wiring plans that will provide
noise suppression should be considered.
Conducted noise enters solid state control at the points
where the control is connected to input lines, output lines,
and power supply wires.
Input circuits are the circuits most vulnerable to noise.
Noise may be introduced capacitatively through wire to
wire proximity, or magnetically from nearby lines carrying
large currents. In most installations, signal lines and
power lines should be separate. Further, signal lines
should be appropriately routed and shielded according to
manufacturer’s recommendations.
When planning system layout, care must be given to
appropriate grounding practice. Because design
differences may call for different grounding, the control
manufacturer’s recommendations should be followed.
C.3.4.3 Design of Wiring for Maximum Protection
Noise can also occur in the form of electromagnetic radiation.
Examples include radio frequency (RF) energy emanating
from portable transceivers (walkie-talkie) and fixed station
transmitters of various types. Close coupling is not required;
the various lines entering the system act as receiving
antennas. Tests described in 3.4.2 may not be sufficient to
demonstrate noise immunity to radio frequency signals.
Variations in building construction and equipment installation
make it impossible for equipment manufacturers to perform
meaningful tests of radio frequency sources. RF fields are
affected by concentrating masses of metal such as steel
beams, piping, conduit, metal enclosures, and equipment
used in production such as fork lift trucks and products
being transported on conveyors.
If the installation site will be subjected to this type of
noise, thorough testing should be performed to assure
that the solid state system has sufficient noise immunity
for the expected levels of radio frequency energy.
Corrective measures should be taken if necessary. These
include shielding of solid state circuits and/or connected
wiring and the establishment of restrictions to provide
safe operating distances between the solid state
equipment and the RF sources.
Grounding practices in industry are frequently
misunderstood and often ignored. Poor grounding can
lead to many problems in solid state systems. Intentionally
grounding one circuit conductor of any electrical supply
system is widely accepted and is generally required by
electrical codes.
However, the non-current carrying parts of a system which
enclose equipment and conductors must also be grounded.
In addition to complying with various codes and standards,
proper equipment grounding achieves several desirable
objectives:
1. It reduces the potential difference between conductive
surfaces to minimize electric shock hazard exposure
for personnel.
2. It provides a path for passage of fault current to operate
protective devices in the supply circuit.
3. It attenuates the electrical noise and transients which
can reach enclosed equipment and also reduces the
electrical noise which the equipment can contribute to
its surroundings.
Summary of Contents for H Series
Page 135: ...DeviceNet Media Design and Installation Guide...
Page 144: ...Publication DNET UM072C EN P July 2004 Table of Contents iv...
Page 170: ...Publication DNET UM072C EN P July 2004 1 26 Get Started Notes...
Page 194: ...Publication DNET UM072C EN P July 2004 2 24 Identify Cable System Components Notes...
Page 212: ...Publication DNET UM072C EN P July 2004 3 18 Make Cable Connections Notes...
Page 238: ...Publication DNET UM072C EN P July 2004 4 26 Determine Power Requirements Notes...
Page 248: ...Publication DNET UM072C EN P July 2004 5 10 Correct and Prevent Network Problems Notes...
Page 250: ...Publication DNET UM072C EN P July 2004 A 2 Understand Select NEC Topics Notes...
Page 263: ......
Page 267: ...Isysnet Serial Bus System Selection Guide Pneumatic...
Page 287: ...H Series Fieldbus DeviceNet Adapters PSSCDM12A PSSCDM18PA User Manual...