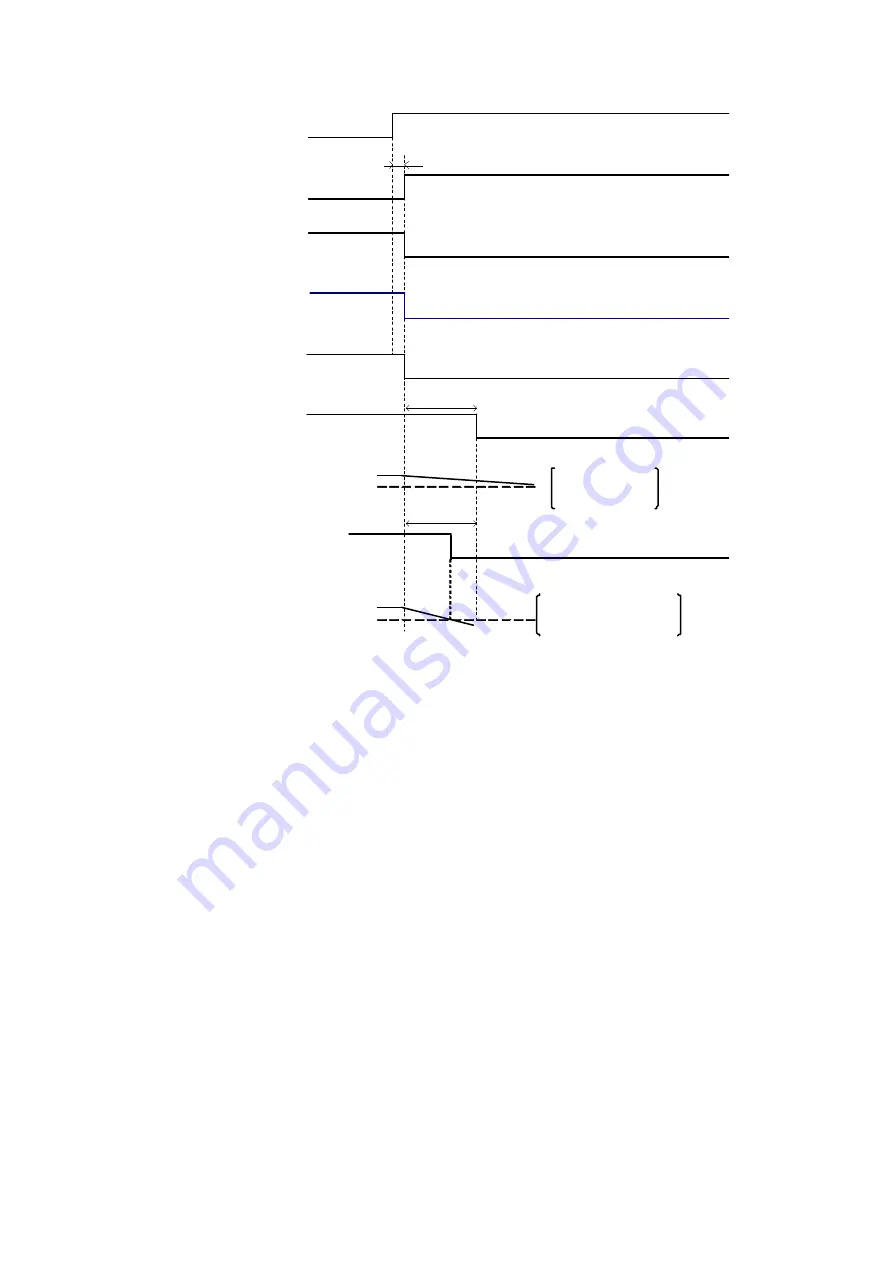
№
SR-ZSV00039
-
75
-
Motor Business Unit, Appliances Company, Panasonic Corporation
8
-
2
-
4
Timing Chart of Operations When Alarm is Issued (Servo-On Command Status)
Whether there is a fault
Dynamic brake
Power to the motor
Brake release output
(BRK-OFF)
Normal
Abnormal
Applied
No power
Output Tr ON
(Break Rel eased)
Power to t he
motor
Released
0. 5~ 5ms
*2
Setting value f or
P
r
4.39 for the motor
speed
Setting value for Pn4.38
t1
*1
Setting value for P
r
4.39
f or the motor spee d
In case t he setti ng
value for Pr4.38 is
reached fi rs t
In case the setting value for
Pr4.39 is reach ed first
Output Tr ON
(Not alarm)
Servo
alarm
output
(ALM)
Setting value for
t1
*1
Output Tr OFF
(Alarm)
Outpu t Tr OFF (Break Applied)
Output Tr ON
(Break Releas ed)
Output Tr OFF (Break Applied)
Servo ready ou tput
(
S-RDY
)
O utput Tr ON
(Ready)
Output Tr OFF
(Not ready)
*1. The time t1 will be either the value used to set Pr4.38 “Mechanical brake action at running setup” or when the
motor speed is reduced to the setting for Pr4.39 “Brake release speed setup” or less, whichever comes first.
*2. The operation of the dynamic brake when an alarm has occurred is according to the setting value for Pr5.10
“Sequence at alarm”.