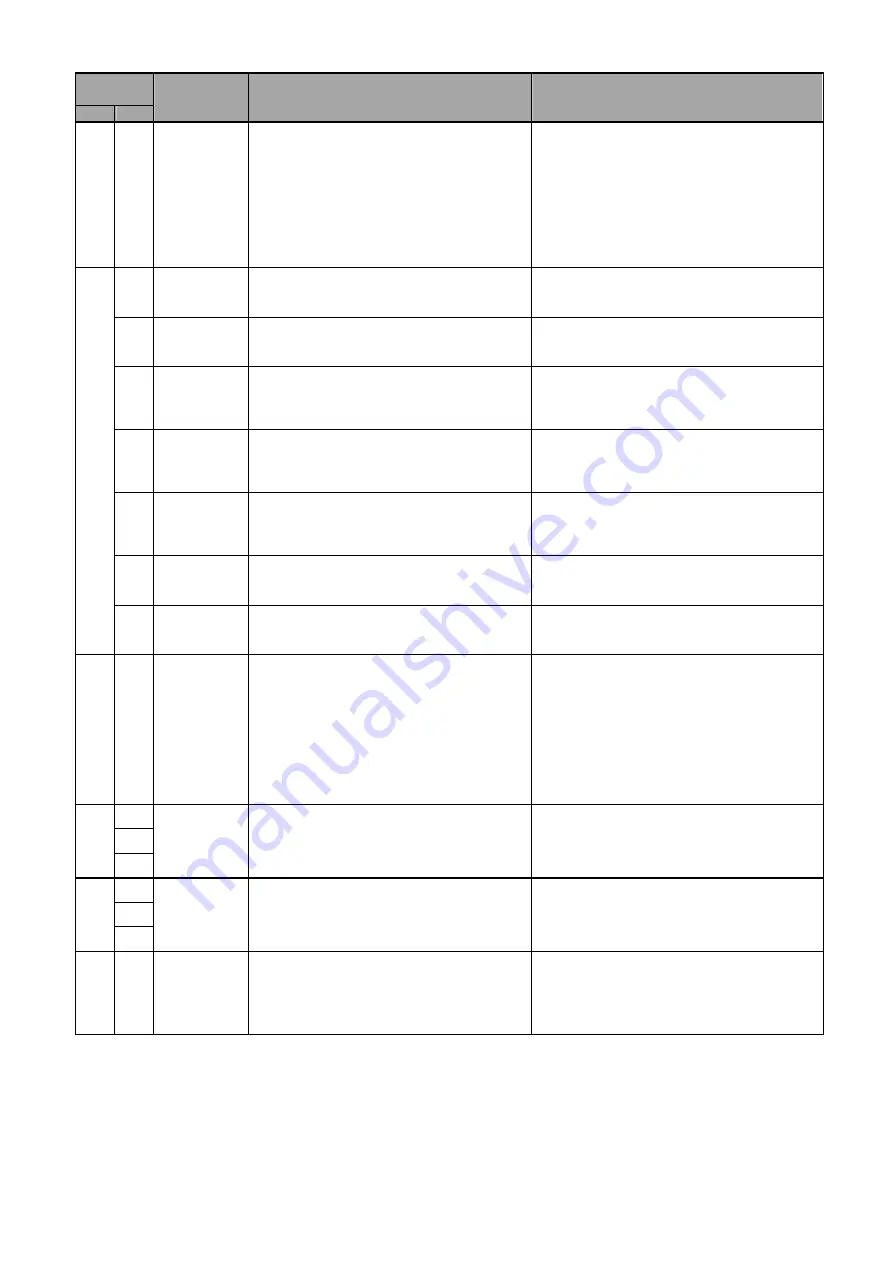
№
SR-ZSV00039
-
62
-
Motor Business Unit, Appliances Company, Panasonic Corporation
Protective
function
Main
Sub
Name
Cause
Action
29
0
Deviation
counter overflow
protection
The position deviation value based on the encoder
pulse has exceeded 2
29
(536870912).
・
Check if the motor runs according to the position
command.
・
Check the torque monitor to see if the output torque
has saturated.
・
Perform a gain tuning.
・
Set the upper limit in Pr0.13 “1
st
torque limit” and
Pr5.24 “2
nd
torque limit”.
・
Make the encoder wiring connections to the wiring
diagram.
0
IF overlaps
allocation error
1 protection
Duplicate assignment of a function to the input signals (SI1,
SI2, SI3, SI4, and SI5).
・
Correct the function assignment to the connector pins.
1
IF overlaps
allocation error
2 protection
Duplicate assignment of a function to the input signals (SI6,
SI7, SI8, SI9, and SI10).
・
Correct the function assignment to the connector pins.
2
IF input
function number
error 1
protection
Undefined numbers are used for the function assignment of
the input signals (SI1, SI2, SI3, SI4, and SI5).
・
Correct the function assignment to the connector pins.
3
IF input
function number
error 2
protection
Undefined numbers are used for the function assignment of
the input signals (SI6, SI7, SI8, SI9, and SI10).
・
Correct the function assignment to the connector pins.
4
IF output
function number
error 1
protection
Undefined numbers are used for the function assignment of
the output signals (SO1, SO2, and SO3).
・
Correct the function assignment to the connector pins.
6
CL fitting error
protection
The deviation counter clear function is assigned to an input
signal other than SI7.
・
Correct the function assignment to the connector pins.
33
7
INH fitting error
protection
The command pulse inhibition input enable function is
assigned to an input signal other than SI10.
・
Correct the function assignment to the connector pins.
34
0
Software limit
protection
The motor has exceeded the allowable motor operation
range specified in Pr5.14 “Motor working range setup”
against the position command input range.
1) The gain is not appropriate.
2) The set value specified in Pr5.14 is too small.
①
Verify the gain (the balance between the position loop gain
and velocity loop gain) and the inertial ratio.
②
Set a greater value in Pr5.14. Or, set Pr5.14 to 0 to disable
the protection function.
0
1
36
2
EEPROM
parameter error
protection
When the EEPROM was read out when the power was
turned on, the data in the parameter storage area was
destroyed.
・
Redo the entire parameter setting.
・
If the problem persists, there may be a failure. Replace the
servo drive with a new one and return the old one to the
dealer of the product for investigation (repair).
0
1
37
2
EEPROM check
code error
protection
When the EEPROM was read out when the power was
turned on, the data that has been confirmed for writing was
destroyed.
There may be a failure. Change the servo drive. Return
them to the dealer for investigation (and repair).
38
0
Over-travel
inhibit input
protection
When Pr5.04 “Over-travel inhibit input setup” is set to 0,
both of the positive/negative-direction drive prohibition
inputs (POT /NOT) were turned on.
When Pr5.04 is set to 2, either of the
positive/negative-direction drive prohibition inputs was
turned on.
・
Check for malfunctions of switches, wires and power
supplies connected to the positive/negative overtravel limits.
Pay special attention to the power supply (DC 12 - 24 V) to
see if it is taking too much time to start.
(Continued)