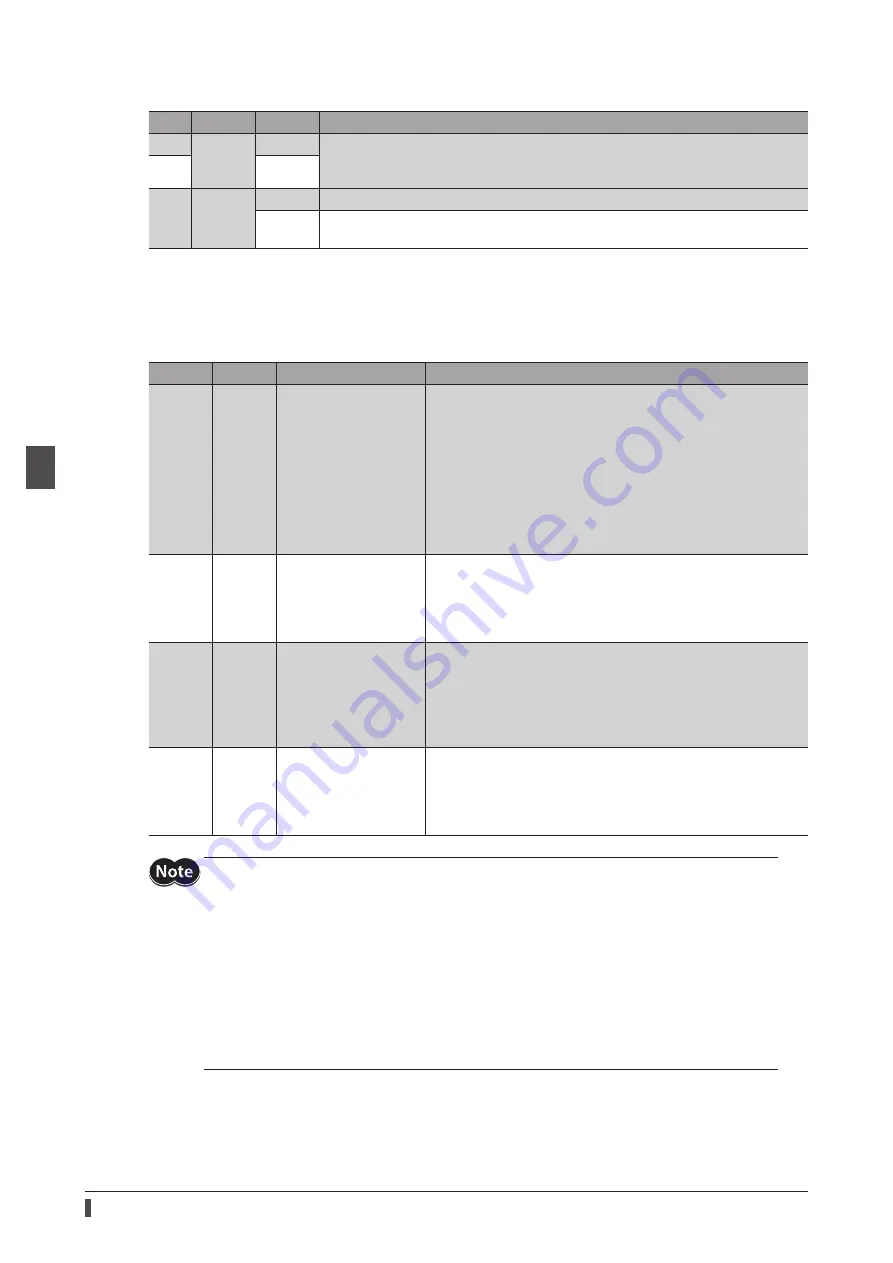
Drive profile
64
3 E
therC
Details of Controlword
Bit
Name
Value
Description
13
Type
−
Selects the operation mode of the Profile velocity mode. The operation mode
changed is updated immediately. For details, refer to “Operation mode of Profile
velocity mode”.
12
−
8
Halt
0
Operation is allowed.
1
Stops the operation. The stopping method is in accordance with the setting of the
Halt option code (605Dh).
For Bit 7 and Bit 3 to Bit 0, refer to “State transition of drive state machine” on p.46.
Operation mode of Profile velocity mode
The operation mode of the Profile velocity mode is set with the Type (6040h: Bit 13, Bit 12). The operation modes are
listed in the table.
Bit 13
Bit 12
Operation mode
Description
0
0
Continuous operation
(position control)
The motor starts rotating at the Starting speed (4142h) and
accelerates until the Target velocity (60FFh) is reached. Once the
Target velocity (60FFh) is reached, operation is continued with the
speed maintained. Since operation is performed while the
position deviation is monitored, an alarm of Overload or Excessive
position deviation is generated when a load exceeding the motor
torque is applied.
If the position deviation suddenly occurs, for example, when a
large load is removed, the motor accelerates suddenly or puts into
a state of overspeed to remove the deviation.
0
1
Continuous operation
(speed control)
The motor starts rotating at the Starting speed (4142h) and
accelerates until the Target velocity (60FFh) is reached. Once the
Target velocity (60FFh) is reached, operation is continued with the
speed maintained. When a load exceeding the motor torque is
applied, an alarm of Overload is generated.
1
0
Continuous operation
(push-motion) *
The motor starts rotating at the Starting speed (4142h) and
accelerates until the Target velocity (60FFh) is reached. Once the
Target velocity (60FFh) is reached, operation is continued with the
speed maintained. When a mechanism installed to the motor
presses against a load, pressure is continuously applied to the
load.
1
1
Continuous operation
(torque control) *
The motor performs self-start operation (rectangular operation) at
the Target velocity (60FFh) and continues the operation with the
speed maintained. When a mechanism installed to the motor
presses against a load, pressure is continuously applied to the
load.
*When continuous operation (push-motion) or continuous operation (torque control) is performed,
note the following.
•
When a mechanism installed to the motor pressed against a load, push-motion operation is
performed while a position deviation of 2.7° generates. Since an alarm of Overload may be
generated if the operation is stopped in this state, perform operation to return the actual position
by 3.6° before push-motion operation is stopped.
•
Do not perform push-motion operation with geared motors and the
DGII
Series. Doing so may
cause damage to the motor or gear part.
•
When push-motion operation is stopped in a state where a load is pressed, set the Operating
current (4120h) of the next operation to be executed, to a value in the Push current (4121h) or less.
If a higher current value than the Push current (4121h) is set, the push current may increase when
the operation transitions, causing an unexpected push force to apply.
Summary of Contents for aSTEP AZ mini Driver
Page 14: ...14 1 Introduction...
Page 128: ...128 3 EtherCAT communication...
Page 146: ...146 4 Object list...
Page 164: ...164 5 Troubleshooting...
Page 170: ...170 6 Reference materials...
Page 171: ...171 6 Reference materials...