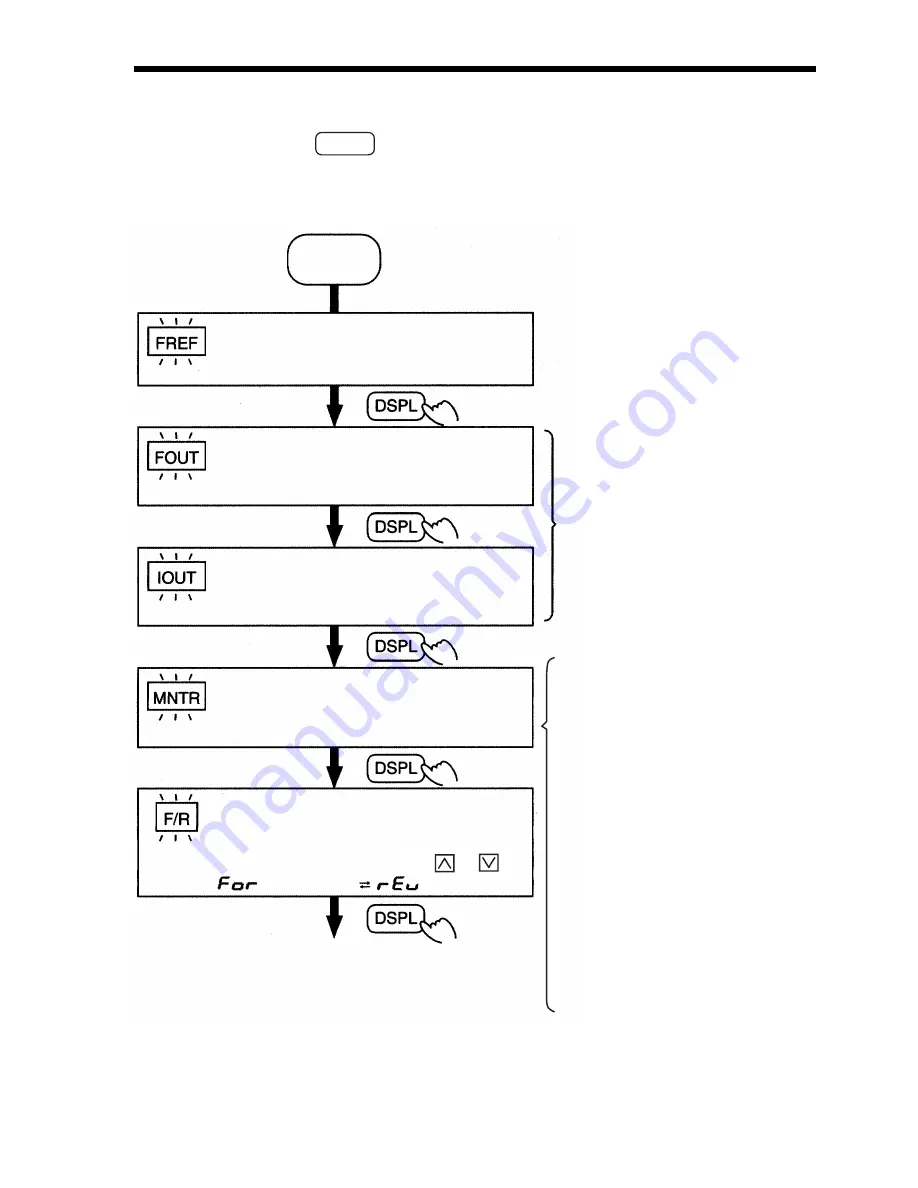
5 Operating the Inverter
43
Function Indicator Description
By pressing
on the Digital Operator, each of the function indi-
cators can be selected.
The following flowchart describes each function indicator.
DSPL
(forward run) (reverse run)
Monitor No.
U-01: Frequency reference (FREF)
U-02: Output frequency (FOUT)
U-03: Output current (IOUT)
U-04: Output voltage reference (Unit: 1V)
U-05: DC voltage (Unit: 1V)
U-06: Input terminal status
U-07: Output terminal status
U-08: Torque monitor
U-09: Fault history (last 4 faults)
U-10: Software number
U-11: Output power
U-12: Frequency offset monitor
U-14: ASCII code from PLC
U-15: Data reception error
U-16: PID feedback
U-17: PID input
U-18: PID output
U-19: Frequency reference bias
Frequency reference setting/monitoring
(Hz)
Sets V7TZ operating speed.
Power ON
Output frequency monitoring (Hz)
Displays frequency that V7TZ is currently
outputting.
Setting disabled.
Output current monitoring (A)
Displays current that V7 IP65 is currently
outputting.
Setting disabled.
A Multi-function monitoring
Description of the selected monitor is
displayed.
FWD/REV Run selection
Sets the motor rotation direction when the RUN
command is given from the Digital Operator
Setting can be changed using the or key
If the V7 IP65 loses power
while in one of these
modes, it will return to
the same mode once
power is restored.
44
(forward run) (reverse run)
Monitor No.
U-01: Frequency reference (FREF)
U-02: Output frequency (FOUT)
U-03: Output current (IOUT)
U-04: Output voltage reference (Unit: 1V)
U-05: DC voltage (Unit: 1V)
U-06: Input terminal status
U-07: Output terminal status
U-08: Torque monitor
U-09: Fault history (last 4 faults)
U-10: Software number
U-11: Output power
U-12: Frequency offset monitor
U-14: ASCII code from PLC
U-15: Data reception error
U-16: PID feedback
U-17: PID input
U-18: PID output
U-19: Frequency reference bias
Frequency reference setting/monitoring
(Hz)
Sets V7TZ operating speed.
Power ON
Output frequency monitoring (Hz)
Displays frequency that V7TZ is currently
outputting.
Setting disabled.
Output current monitoring (A)
Displays current that V7 IP65 is currently
outputting.
Setting disabled.
A Multi-function monitoring
Description of the selected monitor is
displayed.
FWD/REV Run selection
Sets the motor rotation direction when the RUN
command is given from the Digital Operator
Setting can be changed using the or key
If the V7 IP65 loses power
while in one of these
modes, it will return to
the same mode once
power is restored.