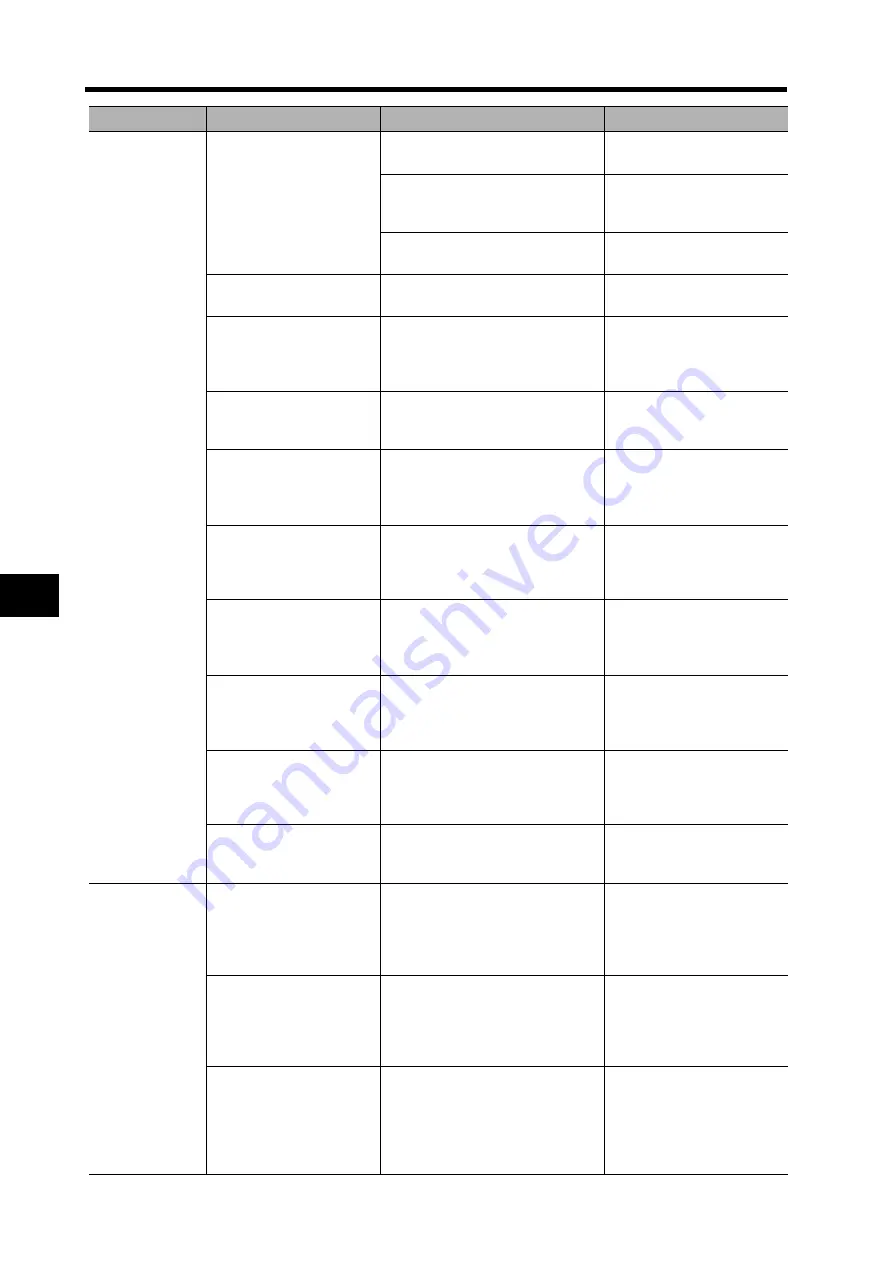
8-15
8-3 Troubleshooting
8
Troubleshooting
The Servomotor
is producing un-
usual noises or
the machine is
vibrating.
(Continued on
next page.)
There are problems with
the machine’s installation.
Check whether the Servomotor’s
mounting screws are loose.
Tighten the mounting
screws.
Check whether the axes are mis-
aligned in the mechanical coupling
system.
Align the mechanical cou-
plings.
Check whether the coupling is un-
balanced.
Adjust the coupling’s bal-
ance.
There is a problem with the
bearings.
Check for noise or vibration around
the bearings.
Contact your OMRON repre-
sentative.
The gain is doesn’t match.
According to load (non-load is in-
cluded), adjust an inertia ratio and
a gain to a suitable value from fac-
tory setting.
•
Use autotuning.
•
Perform manual tuning.
The Speed Feedback Fil-
ter Time Constant (Pn13)
is wrong.
Check the setting of Pn13.
Return the setting to 4 (de-
fault) or increase the setting.
Noise is entering the Con-
trol I/O Cable because the
cable does not meet spec-
ifications.
Check that the cable wire is a twist-
ed-pair wire or shielded twisted-
pair cable with wires of at least
0.08 mm
2
.
Use the Control I/O Cable
that meets specifications.
Noise is entering the Con-
trol I/O Cable because the
cable is longer than the
specified length.
Check the length of the Control I/O
Cable.
Shorten the Control I/O Ca-
ble to 3 m or less.
Noise is entering the cable
because the Encoder Ca-
ble does not meet specifi-
cations.
Check that the cable wires are
twisted-pair wires or shielded twist-
ed-pair wires that are at least
0.12 mm
2
.
Use the Encoder Cable that
meets specifications.
Noise is entering the En-
coder Cable because the
cable is longer than the
specified length.
Check the length of the Encoder
Cable.
Shorten the Encoder Cable
to 20 m or less.
Noise is entering the signal
wires because the Encod-
er Cable is stuck or the
sheath is damaged.
Check whether the Encoder Cable
is damaged.
Correct the Encoder Cable’s
pathway to prevent damage.
Too much noise is entering
the Encoder Cable.
Check whether the Encoder Cable
is tied up in a bundle with or too
close to high current lines.
Lay the Encoder Cable in a
way surges are not applied.
The Servomotor
is producing
unusual noises
or the machine is
vibrating.
(Continued from
previous page.)
The FG’s potential is fluc-
tuating due to devices near
the Servomotor, such as a
welding machine.
Check for grounding problems (fail-
ure to ground or incomplete
grounding) at devices such as a
welding machine near the Servo-
motor.
Ground the equipment prop-
erly and prevent currents
from flowing to the encoder
FG.
Errors are being caused by
excessive vibration or
shock on the encoder.
There are problems with mechani-
cal vibration or motor installation
(such as the mounting surface pre-
cision, attachment, or axial mis-
alignment).
Reduce the mechanical vi-
bration or correct the Servo-
motor’s installation.
The machine and the Ser-
vomotor are resonating.
Check whether the machine is res-
onating.
•
Readjust the Torque Com-
mand Filter Time Constant.
•
If there is resonance, set
the Notch Filter 1 Frequen-
cy (Pn1D) and Notch Filter
1 Width (Pn1E).
Symptom
Probable cause
Items to check
Countermeasures