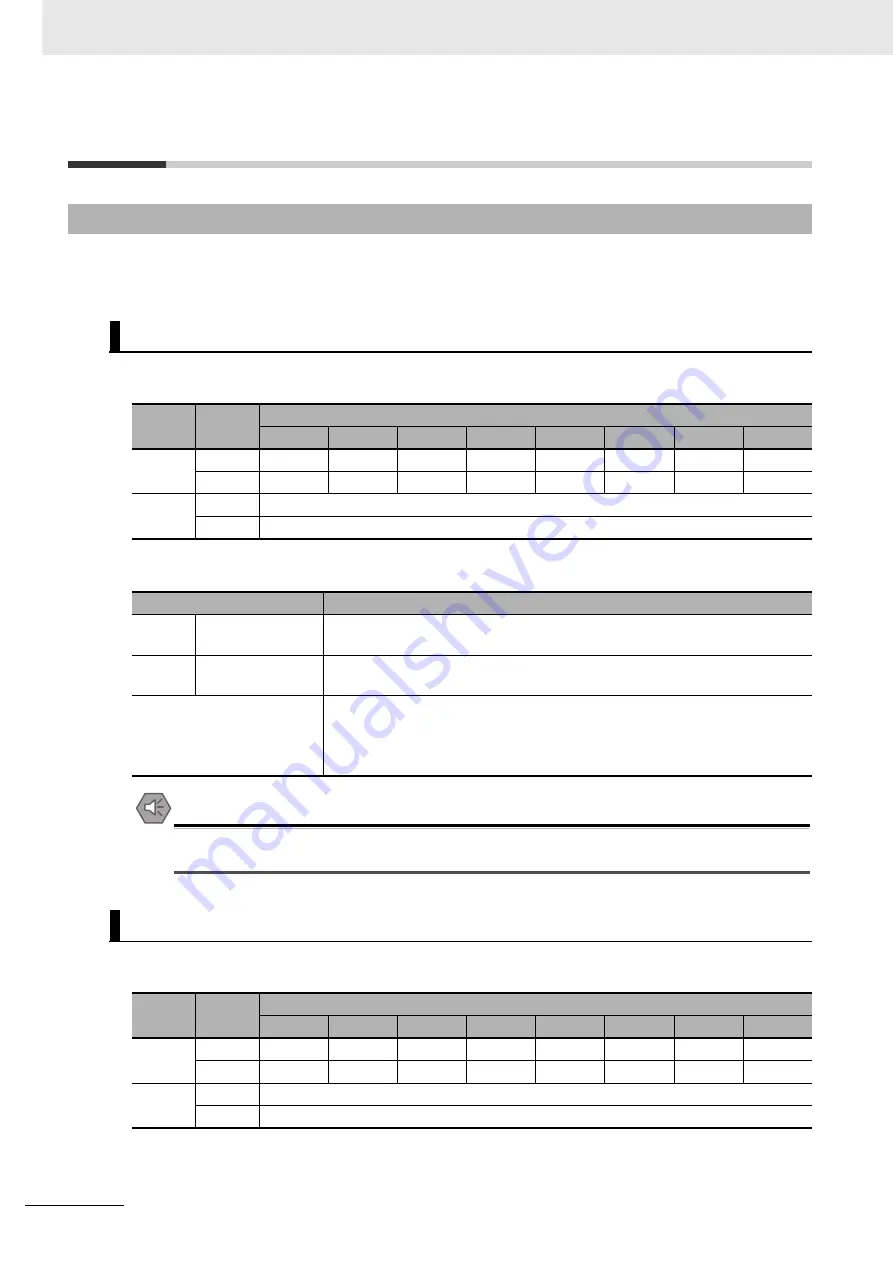
4 Remote I/O
4 - 4
CompoNet Communications Unit User’s Manual (I582-E1)
4-2
Basic and Extended Speed I/O
Basic Speed I/O is a type of Remote I/O included as standard for CompoNet communications.
This Remote I/O offers more limited functions than Extended Speed I/O.
Output Format (CS/CJ-series
→
Inverter)
Output Bit/Data Details
Precautions for Safe Use
For safety reasons, the FW, RV, and RS command must be output after the cause of fault/trip
is removed.
Input Format (CS/CJ-series
←
Inverter)
4-2-1
Basic Speed I/O (20/70)
Basic Remote Output Assembly ID: 20 Dec (14 hex)
Word
No.
Byte
No.
Bit Allocation
bit 7
bit 6
bit 5
bit 4
bit 3
bit 2
bit 1
bit 0
n
0
–
–
–
–
–
RS
–
FW
1
–
–
–
–
–
–
–
–
n + 1
2
Rotation Speed Reference (Low byte)
3
Rotation Speed Reference (High byte)
Name
Description
FW
Forward/Stop
0: Stop
1: Forward
RS
Reset
0: –
1: Fault reset
Rotation Speed Reference
If parameter P049 (Number of Poles for Rotation Speed Setting) is set appropri-
ately, the rotational speed unit is [min
-1
].
If parameter P049 (Number of Poles for Rotation Speed Setting) is set to 0, the
frequency unit is [0.01 Hz].
Basic Remote Input Assembly ID: 70 Dec (46 hex)
Word
No.
Byte
No.
Bit Allocation
bit 7
bit 6
bit 5
bit 4
bit 3
bit 2
bit 1
bit 0
n
0
–
–
–
–
–
FWR
–
AL
1
–
–
–
–
–
–
–
–
n + 1
2
Rotation Speed Monitor (Low byte)
3
Rotation Speed Monitor (High byte)
Summary of Contents for 3G3AX-MX2-CRT-E
Page 94: ...3 Network Startup 3 36 CompoNet Communications Unit User s Manual I582 E1...
Page 118: ...4 Remote I O 4 24 CompoNet Communications Unit User s Manual I582 E1...
Page 134: ...5 Message Communications 5 16 CompoNet Communications Unit User s Manual I582 E1...
Page 167: ...I 1 I CompoNet Communications Unit User s Manual I582 E1 Index...
Page 171: ......