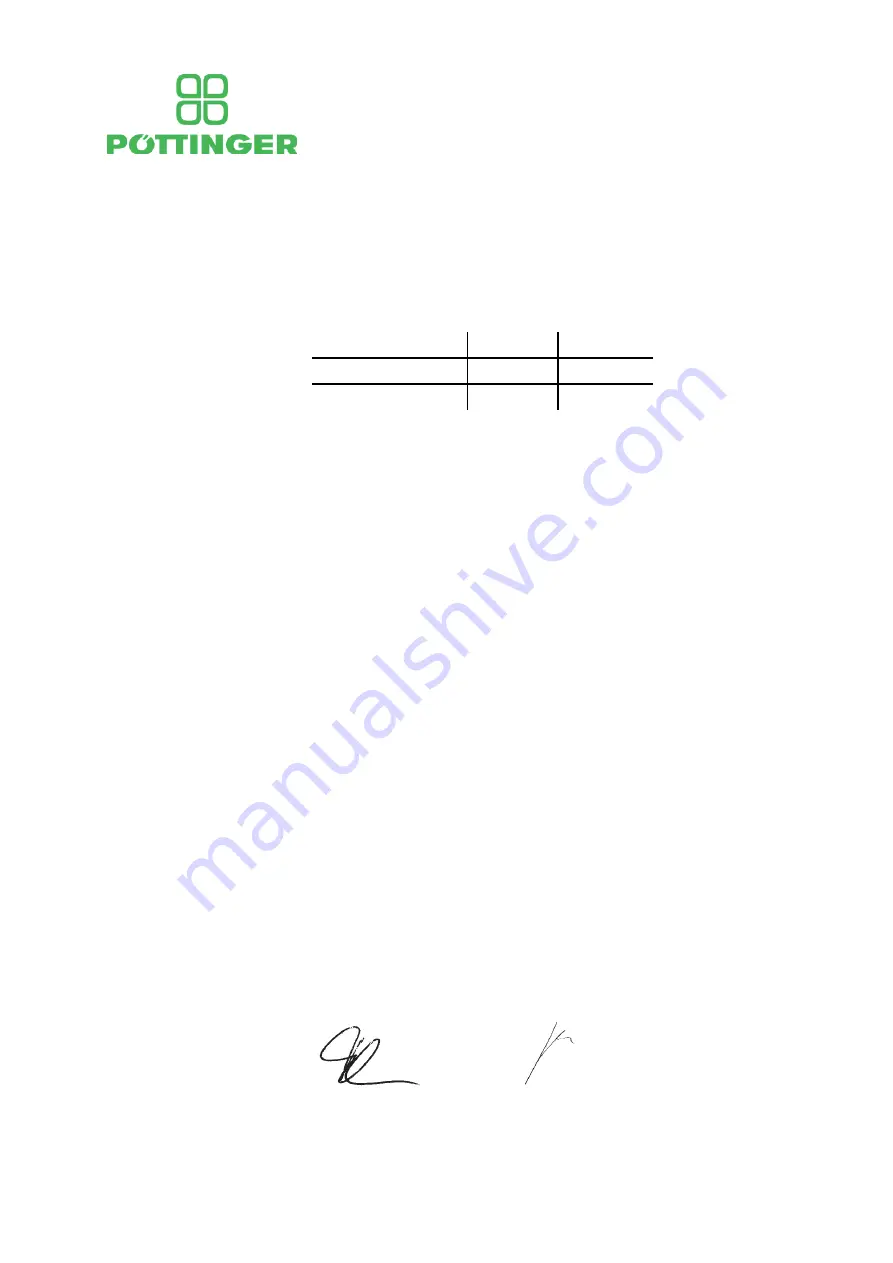
Name and address of the manufacturer:
PÖTTINGER Landtechnik GmbH
Industriegelände 1
AT - 4710 Grieskirchen
Machine (interchangeable equipment)
:
mower
Type
Serial no.
The manufacturer declares that the machines adhere to all relevant provisions in the
following EU directive:
machinery 2006/42/EG
In addition to this, the manufacturer also declares adherence to the other following EU
directives and/or relevant provisions
Source of applied, harmonised norms:
EN ISO 12100
EN ISO 4254-1
EN ISO 4254-12
Source of applied miscellaneous technical norms and / or specifications:
Person responsible for documentation:
Andreas Gadermayr
Industriegelände 1
A-4710 Grieskirchen
EC Conformity Declaration
Original Conformity Declaration
Markus Baldinger,
CTO R&D
Grieskirchen, 01.08.2016
Jörg Lechner,
CTO Production
7KH&(QRUPLVQRWYDOLGLQWKH8QLWHG6WDWHVRI$PHULFDDQG&DQDGD
Novacat V10
V10 ED
V10 RC
3846
3846
3846