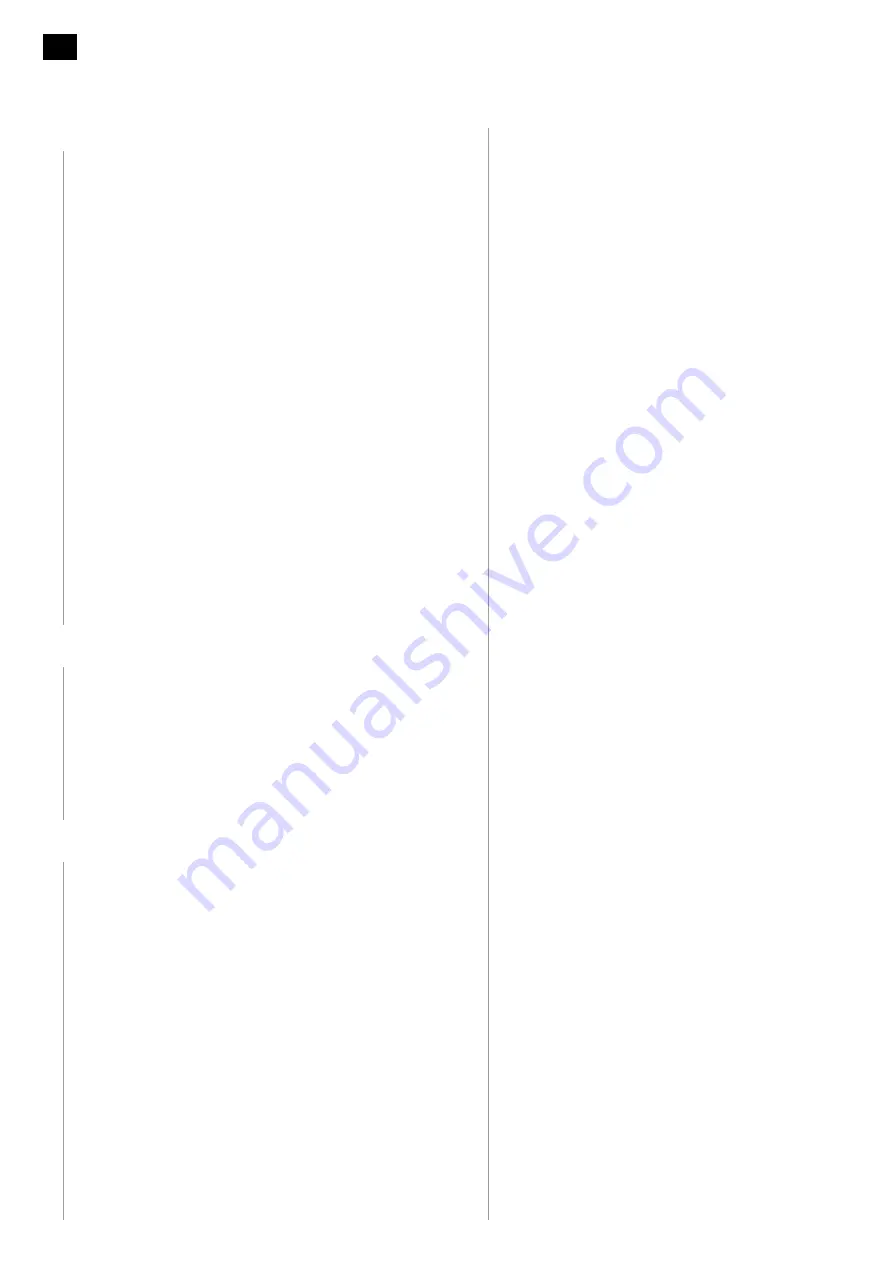
Installa
ti
on instruc
ti
ons for the IMM'Ax automa
ti
c immersed safety cover - 32/36
32
8.2 Checking the power supply cable between
the electric box and the roller motor
8.2.1 Reconnect the roller power cable to the box and
disconnect it from the junc
ti
on box.
8.2.2 Step by step, measure the presence of the indicated
voltage on the following terminals:
8.2.3
Connec
ti
ng cable test: 24 V DC on the electric box
terminals marked "+" and "-" at the connec
ti
ng cable
connec
ti
ons. Then 24 V DC on the terminals for the 2
wires arriving at the junc
ti
on box. If the voltage is below
22V, this voltage will not be su
ffi
cient for the correct
opera
ti
on of the motor.
8.2.4 Check
that the cable sec
ti
ons correspond to what is indicated
on
fi
g. 1,
the quality of the connec
ti
ons (make sure of the
con
ti
nuity of the connec
ti
ons in the junc
ti
on box and the
box),
the absence of humidity or even water in the connec
ti
on
box (Reminder: the connec
ti
on box must always be
fi
lled
with gel).
8.2.5 If the voltage is not present or the value is di
ff
erent,
this means that your cable is defec
ti
ve, cut, damaged
or has the wrong resistance, or is located too near to a
cable with a di
ff
erent voltage that disrupts its opera
ti
on.
Replace the cable. Make a temporary connec
ti
on using
another cable directly between the electric box and the
motor to carry out new tests.
8.3 Checking the key switch
8.3.1 Use the con
ti
nuity measurement of your mul
ti
meter to
check that the contacts (NO) located behind the switch
close one a
ft
er the other when the key is turned
fi
rst in
one direc
ti
on and then in the other.
8.3.2 In the box
Measure 24 V DC between the "com" and the "open"
when the key is on "open".
Measure 24 V DC between the "com" and the "close"
when the key is in the "close" posi
ti
on.
8.4 Direct check of the motor
8.4.1 If the cover does not move, check the motor sensor
opera
ti
on (return data) by checking:
• the good condi
ti
on of the motor cable
• the correct placement of the stainless steel blocking
ring against the roller tube so that the
fl
anges are
correctly
fl
a
tt
ened against the pool walls.
8.4.2 If these elements are correct, the motor sensor is out
of order (this can be due to a power surge related to a
faulty connec
ti
on, a storm or a defec
ti
ve component. The
motor must be returned to AS POOL for analysis).