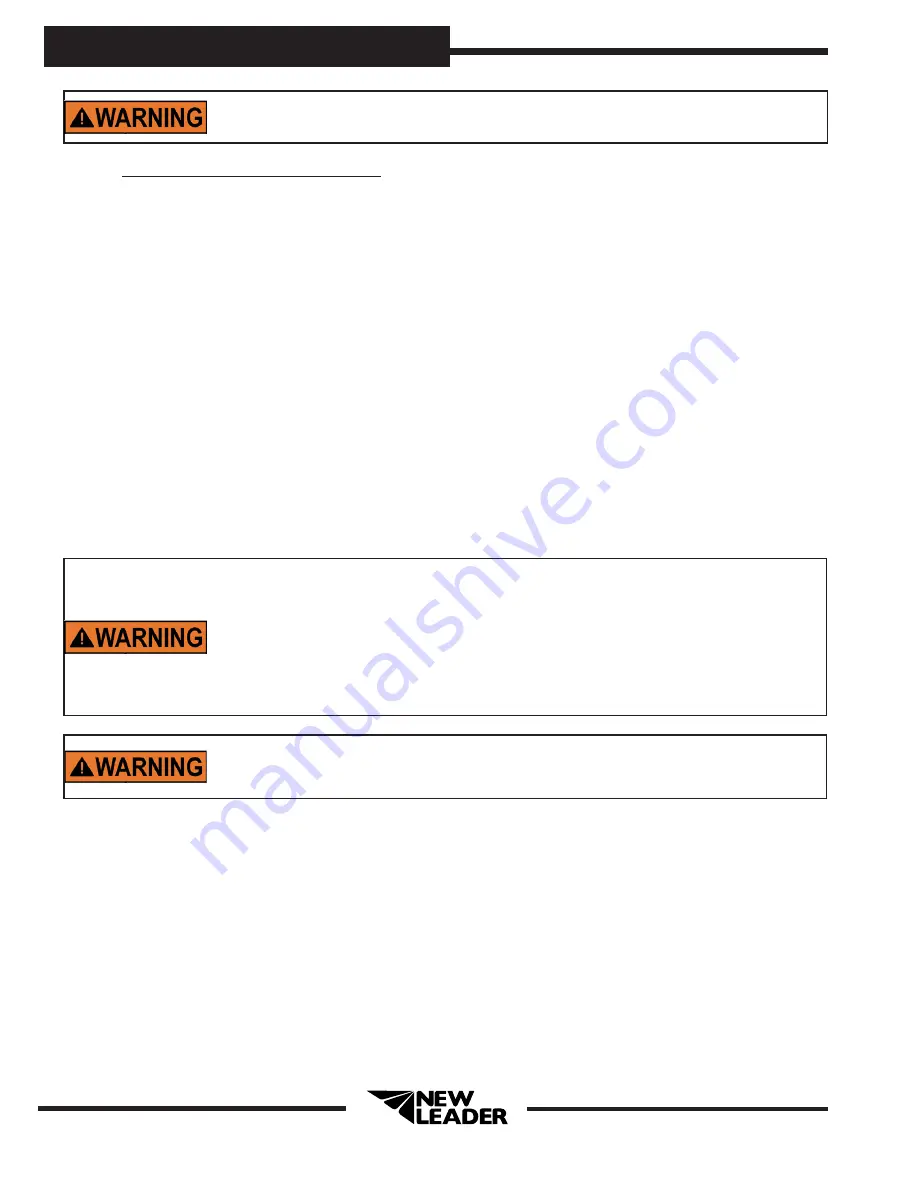
- 60 -
www.NewLeader.com
(800) 363-1771
317314-C
Raven OMNiPOWER NL5000 G5
Initial Start-Up
Unit is now ready for field testing.
Stand clear of moving machinery� Failure to comply with this requirement could result in
death or serious injury�
NOTE: Do not load spreader with material�
1� Check entire unit to make sure all fasteners are in place and properly tightened per “Standard
Torques” section in this manual�
2� Make sure no other persons are in vicinity of spreader�
3� Make sure no loose parts are in unit or on conveyor or spinner�
4�
Check oil level in hydraulic reservoir; fill as necessary. Refer to “Lubricant & Hydraulic Oil
Specifications” in Lubrication & Maintenance section of this manual for proper oil. Completely open
reservoir valves�
5� Start engine and turn on hydraulics� Allow hydraulics to circulate until oil is warm�
6� Perform hydraulic bleed procedure via the display� Refer to “Hydraulic Bleeding” in Controller
Operations section of this manual�
7� Perform all calibration procedures for spinners and all installed bins� Refer to “Component
Calibration” in Controller Operations section�
8� Run spinner at 300 RPM� Allow to run until spinner is operating smoothly�
9� Run conveyor at 20 RPM and spinner at 300 RPM� Run until conveyor is operating smoothly�
10� Run conveyor at 20 RPM and spinner at 700 RPM� Allow both conveyor and spinner to run until
operating smoothly�
11� Enable boundary left and right and verify that RPM adjust accordingly�
12� Run conveyor at 0 RPM and spinner at 0 RPM� Make sure both conveyor and spinner do not move�
13� Shut system down�
DO NOT check leaks with hands while system is operating as high pressure oil leaks can be
dangerous! If skin is pierced with hydraulic fluid at high pressure seek immediate medical
attention as fluid injected into the skin could cause gangrene if left untreated. Relieve
pressure before disconnecting hydraulic lines or working system� Make sure all hydraulic
fluid connections are tight and all hydraulic hoses and lines are in good condition before
applying pressure to the system� Wear protective gloves and safety glasses or goggles
when working with hydraulic systems� Failure to comply with this requirement could result
in death or serious injury�
DO NOT check for leaks adjacent to moving parts while system is operating as there may
be danger of entanglement! Failure to comply with this requirement could result in death
or serious injury�
14� Check all connections in hydraulic system to make sure there are no leaks�
15�
Check hydraulic oil reservoir and refill to maintain level at mid-point of gauge.
Summary of Contents for Raven OMNiPOWER NL5000 G5
Page 8: ...Insert Current New Leader Warranty Warranty ...
Page 9: ...SAFETY ...
Page 28: ...INSTALLATION ...
Page 45: ... 43 Raven OMNiPOWER NL5000 G5 www NewLeader com 800 363 1771 317314 C Insert Installation ...
Page 46: ... 44 www NewLeader com 800 363 1771 317314 C Raven OMNiPOWER NL5000 G5 Insert Installation ...
Page 47: ... 45 Raven OMNiPOWER NL5000 G5 www NewLeader com 800 363 1771 317314 C Insert Installation ...
Page 53: ...OPERATIONS ...
Page 66: ...MAINTENANCE ...
Page 83: ...HYDRAULICS ...
Page 90: ...CONTROLLER ...
Page 147: ...SPREAD PATTERN ...
Page 158: ...PARTS ...
Page 162: ... 154 www NewLeader com 800 363 1771 317314 C Raven OMNiPOWER NL5000 G5 Mounting Body ...
Page 166: ... 158 www NewLeader com 800 363 1771 317314 C Raven OMNiPOWER NL5000 G5 Subframe Subframe ...
Page 168: ... 160 www NewLeader com 800 363 1771 317314 C Raven OMNiPOWER NL5000 G5 Scale Scale ...
Page 169: ... 161 Raven OMNiPOWER NL5000 G5 www NewLeader com 800 363 1771 317314 C Scale Scale ...
Page 170: ... 162 www NewLeader com 800 363 1771 317314 C Raven OMNiPOWER NL5000 G5 Scale Scale ...
Page 198: ... 190 www NewLeader com 800 363 1771 317314 C Raven OMNiPOWER NL5000 G5 Connection Hydraulics ...
Page 199: ... 191 Raven OMNiPOWER NL5000 G5 www NewLeader com 800 363 1771 317314 C Connection Hydraulics ...
Page 200: ... 192 www NewLeader com 800 363 1771 317314 C Raven OMNiPOWER NL5000 G5 Connection Hydraulics ...
Page 232: ... 224 www NewLeader com 800 363 1771 317314 C Raven OMNiPOWER NL5000 G5 Tarp ...
Page 258: ... 250 www NewLeader com 800 363 1771 317314 C Raven OMNiPOWER NL5000 G5 Hydraulics MultApplier ...
Page 259: ... 251 Raven OMNiPOWER NL5000 G5 www NewLeader com 800 363 1771 317314 C Hydraulics MultApplier ...
Page 260: ... 252 www NewLeader com 800 363 1771 317314 C Raven OMNiPOWER NL5000 G5 Hydraulics MultApplier ...