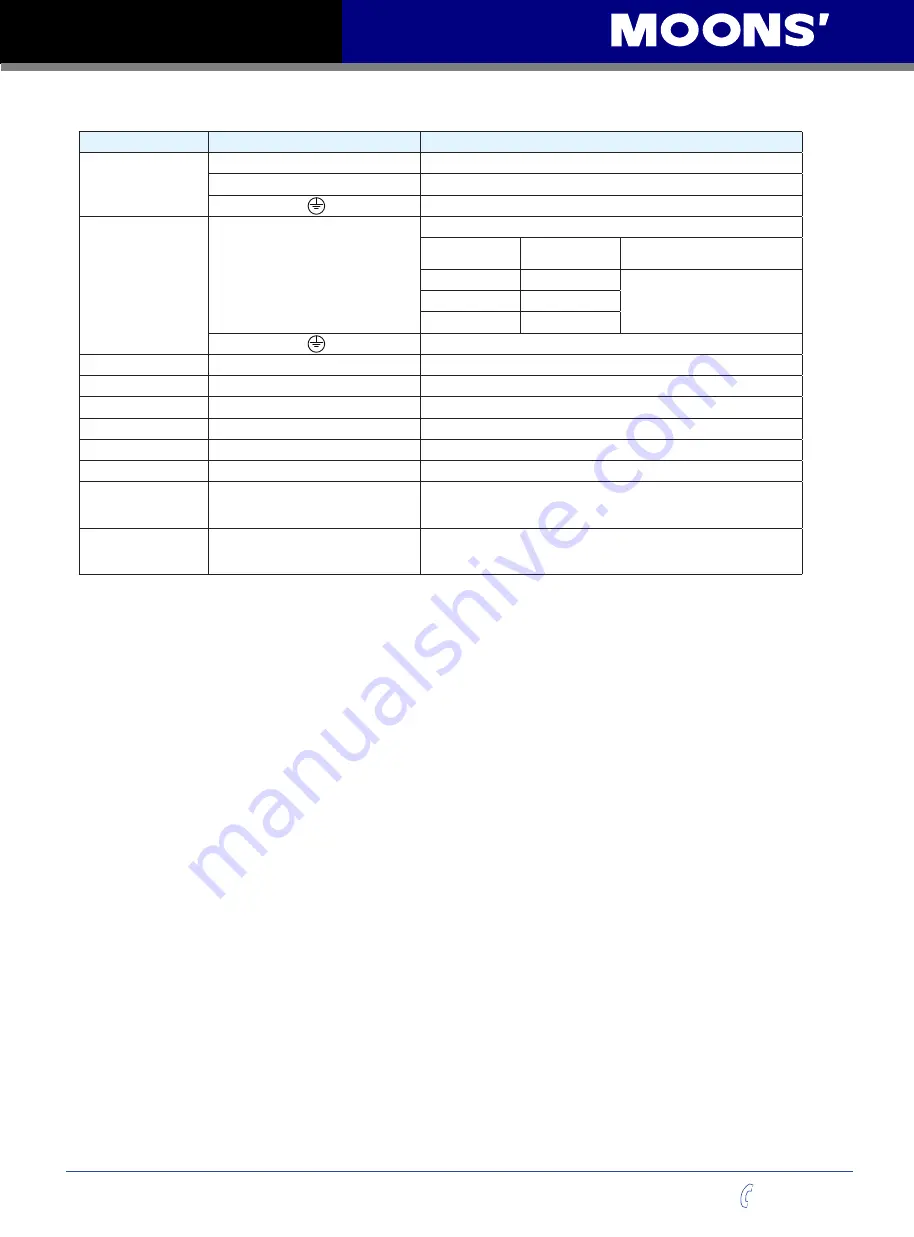
M2DC Series Hardware Manual
28
Rev. 1.1
2018/04
400-820-9661
4.1.2 Servo Drive Connectors and Terminals
Terminal Identification
Description
Details
P1
V+, V-
Used to connect DC main circuit power
AUX
Used to connect an auxiliary circuit power
Ground
P2
U, V, W
Used to connect servo motor
Terminal
Symbol
Wire color
Description
U
Red
Connects to servo motor
V
Yellow
W
Blue
Ground
P3
External regeneration resistor port
Conect to external regeneration absorbing resistor
CN1
Communication Port
User to connect PC
CN2
I/O Connector
Used to connect external controllers
CN3
Encoder Feedback Connector
Used to connect servo motor encoder
CN4
Reserved
CN5
STO Connector
Used to connect STO (Safe Torque Off)
CN6
RS-485/CANopen Port
Ethernet Port
*RS-232 Communication Port
RJ45 connector, Daisy Chain, Used for RS-485/CANopen/
Ethernet
*RS-232 Communication Port (-Q Type Only)
CN7
RS-485/CANopen Port
Ethernet Port
Communication Port
RJ45 connector, Daisy Chain, Used for RS-485/CANopen /
Ethernet
Communication
4.1.3 Connections and Wiring Notes
•
Ensure the grounding wires are securely connected. Wire with a cross section of more than 2.0mm
2
is
recommended.
•
Grounding method must be single point grounding.
• Ensure V+ and V- are correctly wired, and voltage supplies are within the specified range.
• Auxiliary power V+ connects to drive AUX connector, auxiliary power V- connects to drive V-.
• Ensure U/V/W is wired following the order of RED/YELLOW/BLUE.
• An isolation transformer or EMI filter is recommended on drive’s power supply to ensure the drive’s
safety and improve its anti-interference level.
•
Set up emergency stop circuitry to switch off the power supply when a fault occurs.
•
DO NOT touch the drive or motor’s connector terminals for at least 5 minutes after the drive and motor
have been powered off. There are electrical charge components in the circuitry which discharge slowly.
•
Install the encoder cables in a separate conduit from the motor power cables to avoid signal noise.
Separate the conduits by at least 30cm (11.8 inches).
• Use multi-stranded twisted-pair wires or multi-core shielded-pair wires for the encoder feedback cables.
• The maximum length of the signal input/output cable should be no more 5 meters, and the encoder
(PG) feedback cable no more than 15 meters.