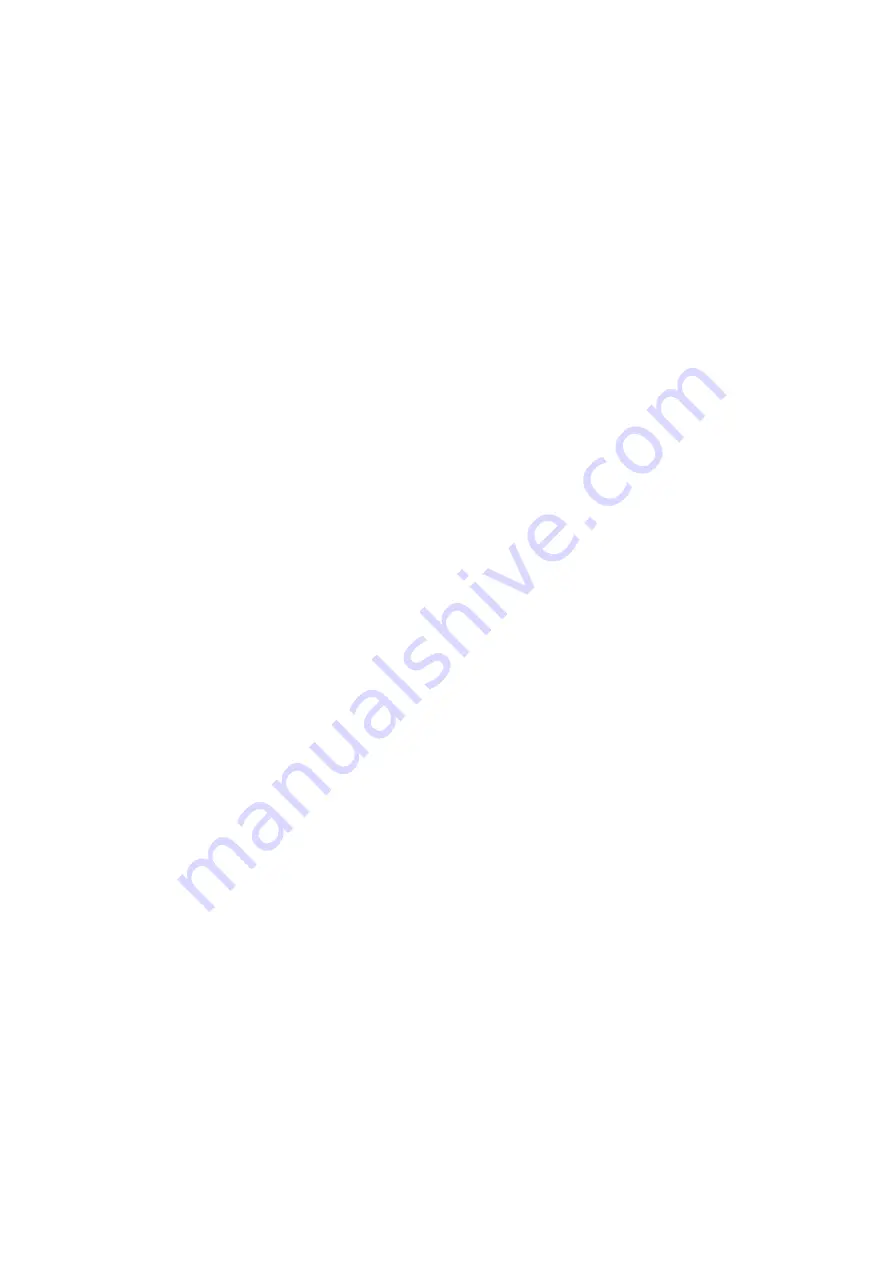
• To reduce the hazards for people or equipment, the user must
include in the machine design measures that restrict the conse-
quences of a malfunction or failure of the drive (increased motor
speed or sudden standstill of motor). These measures include:
– Other independent devices for monitoring safety-related vari-
ables (speed, travel, end positions etc.).
– Electrical or non-electrical system-wide measures (electrical or
mechanical interlocks).
– Never touch live parts or cable connections of the frequency
inverter after it has been disconnected from the power supply.
Due to the charge in the capacitors, these parts may still be
live after disconnection. Fit appropriate warning signs on the
frequency inverter.
• The decentralised power distribution systems must only be
utilised in accordance with the operating manual for their
intended use in technically perfect condition, taking into account
safety requirements and any possible hazards.
• Proper transport, storage, installation, careful operation and
maintenance must be ensured for the trouble-free and safe oper-
ation of the control system. Any faults that may impair safety
must be rectified immediately.
• If the decentralised power distribution systems are part of the
electrical equipment of a machine, they must be included by the
machine manufacturer in the conformity assessment procedure.
The IEC/EN 60204-1 standard must be observed.
• The safety requirements of the Machine Directive 89/392/EC
must be observed when engineering, installing and commis-
sioning the decentralised power distribution systems as part of
the power supply of machines and their control systems. The
national occupational safety regulations apply in the specific
application. Observe the relevant safety and accident prevention
regulations for the application, such as the Safety of Machinery
standards. All safety devices of the controlled machine must be
implemented so that they operate independently of the control
system. Emergency-Stop devices complying with IEC/EN 60204
must be effective in all operating modes of the system. The
power supplies of all the switching elements of the control
system must be disconnected in the event of an Emergency-Stop.
Uncontrolled and undefined startups must not occur, e.g.
– Startup after unlatching the Emergency-Stop devices and/or
– Startup of the control systems without the DP master or DP
slave responding.
• For stationary installations or systems without all-pole mains
switches, the building installation must be provided with a
mains switch or fuse.
• The rated voltage range set for load current power supplies and
power supply modules must comply with the local mains supply.
• With the 24 V power supply ensure that
– lightning protection measures are provided and/or
– the 24 V SELV voltage is provided with safe electrical isolation.
• Measures should be taken to ensure the proper restart of
programs interrupted after a voltage dip or failure. This should
not cause dangerous operating states even for a short time.
If necessary, Emergency-Stop devices should be implemented.
• Transport, installation, commissioning and maintenance work
must only be carried out by qualified personnel (in accordance
with IEC 60364, HD 384 and national occupational safety regu-
lations).
• Before installation and before touching the device ensure
that you are free of electrostatic charge.
• Suitable safety hardware and software measures should be
implemented for the I/O interface so that an open circuit on the
signal side does not result in undefined states in the automation
devices.
• A suitable electrical tool should be used. The mains supply
connection should always be disconnected (remove mains plug
or open isolating switch) before opening the device. Fuses
should only be replaced with those specified in the technical
data.
• The highest permissible operating temperature of the decentral-
ised power supply systems is 50 °C. Cables must be protected
from impermissible temperatures by means of shielding or suffi-
cient clearance from the heat source.
• Cables should be laid in a cable duct in areas where there is a
risk of mechanical damage to cables or conductors, e.g. with
forklift trucks.
Summary of Contents for Rapid Link
Page 10: ...01 08 AWB2190 1430GB 6 ...
Page 40: ...01 08 AWB2190 1430GB 36 ...
Page 48: ...01 08 AWB2190 1430GB 44 ...
Page 70: ...01 08 AWB2190 1430GB 66 ...
Page 146: ...01 08 AWB2190 1430GB 142 ...
Page 162: ...01 08 AWB2190 1430GB 158 ...