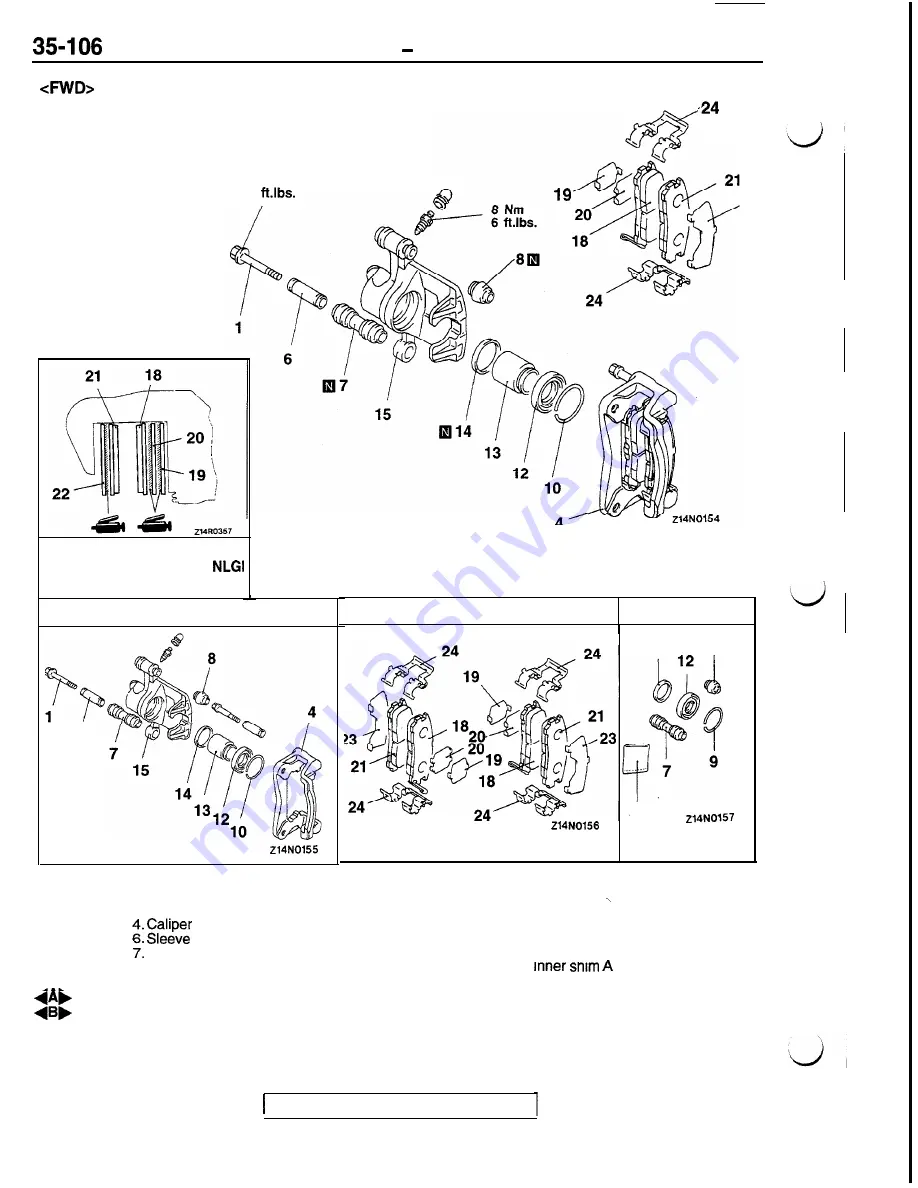
SERVICE BRAKES Rear Disc Brake
27 Nm
20
23
Grease:
Brake grease SAE 5310,
No. 1
Brake caliper kit
6
Caliper disassembly steps
1. Lock pin
support (pad, clip, shim)
Lock pin boot
8. Guide pin boot
10. Boot ring
12. Piston boot
13. 14. Piston Piston seal
15. Caliper body
00002147
Pad kit
Seal and
boot
kit
‘4 8
Grease
Pad
assembly disassembly steps
1. Lock pin
4. Caliper support (pad, clip, shim)
18. Pad and wear indicator assembly
19. Inner shim B
. .
20.
21. Pad assembly
23. Outer shim
24. Clip
TSB
Revision
Summary of Contents for 1992 3000GT
Page 1: ......
Page 2: ......
Page 104: ...13 2...
Page 118: ...13A 14 MULTIPORT FUEL INJECTION Special Tools TSB Revision...
Page 394: ...NOTES...
Page 460: ...NOTES...
Page 532: ...NOTES...
Page 536: ...21 4 CLUTCH Troubleshooting Excessive wear of clutch disc facin I LJ 1 TSB Revision...
Page 556: ...NOTES...
Page 570: ...22 14 MANUAL TRANSAXLE AWD Special Tools SPECIAL TOOLS Oil seal installer TSB Revision...
Page 582: ...i...
Page 584: ...I di...
Page 586: ......
Page 588: ......
Page 590: ......
Page 592: ......
Page 594: ......
Page 596: ......
Page 598: ......
Page 600: ...I I I LJ LJ I L...
Page 609: ...AUTOMATIC TRANSAXLE Troubleshooting 23 I 9 L L 1 TSB Revision...
Page 668: ...NOTES...
Page 692: ...NOTES...
Page 752: ...33 2 NOTES...
Page 766: ...NOTES...
Page 809: ...REAR SUSPENSION AWD Special Tools 34 23 B lMB990244 i TSB Revision...
Page 810: ...34 24 REAR SUSPENSION AWD Troubleshooting TROUBLESHOOTING TSB Revision...
Page 946: ...NOTES...
Page 958: ...NOTES...
Page 960: ...37 2...
Page 964: ...37A 4 STEERING Snecial Tools SPECIAL TOOLS Preload socket General service TSB Revision...
Page 994: ...NOTES...
Page 1006: ...NOTES...
Page 1068: ...42 62 BODY Sunroof SUNROOF SWITCH CONTINUITY CHECK 18FO403 TSB Revision...
Page 1070: ...NOTES I...
Page 1103: ...52 1 i INTERIOR CONTENTS INTERIOR 52A SUPPLEMENTAL RESTRAINT SYSTEM SRS 528 i...
Page 1104: ...52 2 NOTES...
Page 1220: ...NOTES dl...
Page 1307: ...1 1 I I I 1 I 1 1 I I I j I i i i I i I j j...
Page 1308: ......