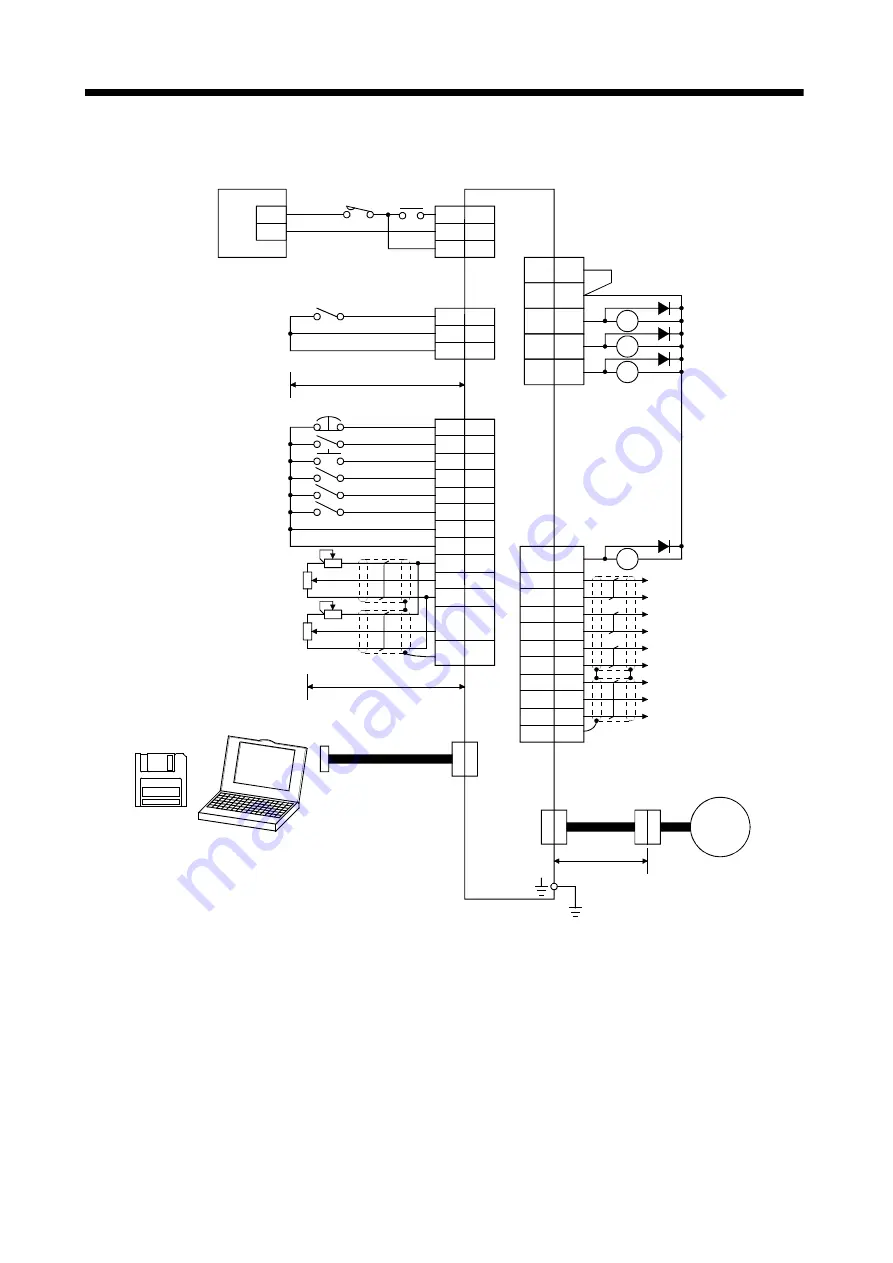
3 - 5
3. SIGNALS AND WIRING
3.1.3
Torque control mode
(Note1)
2m (6.5ft) max.
10m(32ft) max.
Personal
computer
(Note 7)
Servo configuration
software
Zero speed
Limiting torque
(Note 2)
Trouble
30m (98ft) max.
Encoder Z-phase pulse
(differential line driver)
Encoder A-phase pulse
(differential line driver)
Encoder B-phase pulse
(differential line driver)
Control common
Encoder Z-phase pulse
(open collector)
Circuit
protector
Speed Selection 1
RA1
RA2
RA3
18
10
20
SP1
SG
SG
1
2
3
P24M
P24G
P24L
+
−
CN1A
15
5
14
8
9
Plate
20
1
11
EMG
SON
RES
RS1
RS2
SD
SG
P15R
SG
LG
10
12
ALM
19
ZSP
6
TLC
15
5
14
7
16
17
4
LZ
LZR
LA
LAR
LB
LBR
LG
OP
P15R
SD
1
6
Plate
CNP1
Servo amplifier
CN1B
CNP2
CNP3
13
+
8
7
SP2
TC
2
VLA
19 RD
RA4
CN1A
Ready
3
VDD
COM
RA
Servo
motor
CN1B
(Note 4,6)
(Note 4,6)
(Note 4,6)
Forward rotation selection
Forced stop
Servo on
Reset
Reverse rotation selection
(Note 3)
Analog speed limit
0 to
+
10V/max. speed
Analog torque command
±
8V/max. current
Upper limit setting
Upper limit setting
24VDC power supply
(Note 4)
(Note 5)
Speed selection2
Note: 1. To prevent an electric shock, fit the supplied earth terminal (E) to the servo amplifier and always
connect it to the earth (E) of the control box. (Refer to section 3.9.)
2. Connect the diode in the correct direction. If it is connected reversely, the servo amplifier will be
faulty and will not output signals, disabling the forced stop and other protective circuits.
3. The forced stop switch must be installed.
4. CN1A and CN1B have the same shape. Wrong connection of the connectors will lead to a fault.
5. Trouble (ALM) is connected with COM in normal alarm-free condition.
6. The pins with the same signal name are connected in the servo amplifier.
7. Use MRZJW3-SETUP61E or later.