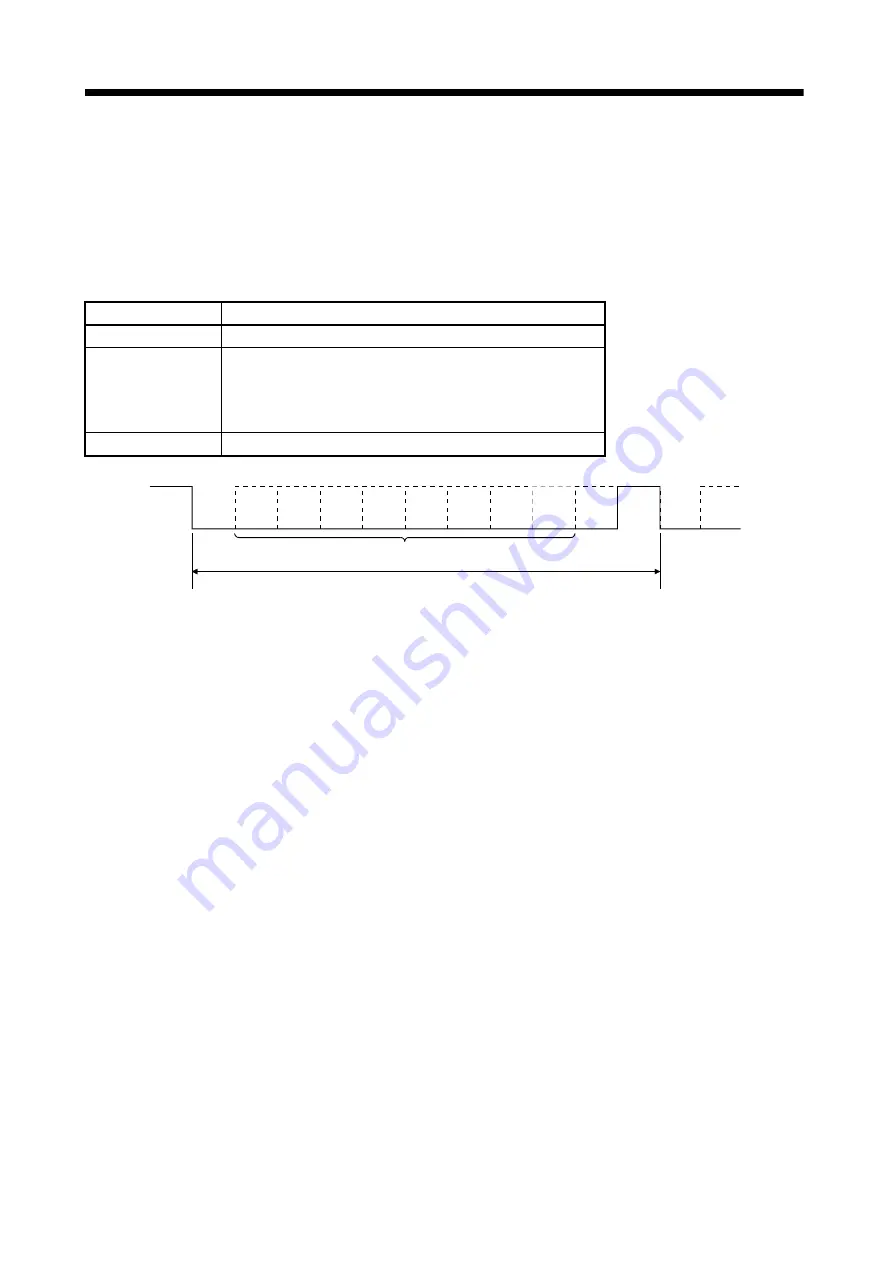
13 - 3
13. COMMUNICATION FUNCTIONS
13.2 Communication Specifications
13.2.1 Communication overview
The MELSERVO-J2 series is designed to send a reply on receipt of an instruction. The device which gives
this instruction (e.g. personal computer) is called a master station and the device which sends a reply in
response to the instruction (servo amplifier) is called a slave station. When fetching data successively, the
master station repeatedly commands the slave station to send data.
Item
Description
Baudrate
4800/9600/19200 asynchronous system
Transfer code
Start bit : 1 bit
Data bit : 8 bits
Parity bit : 1 bit (even)
Stop bit
: 1 bit
Transfer protocol
Character system, half-duplex communication system
1 frame (11bits)
Data
0
1
2
3
4
5
6
7
(LSB)
(MSB)
Start
Parity
Stop
Next
start