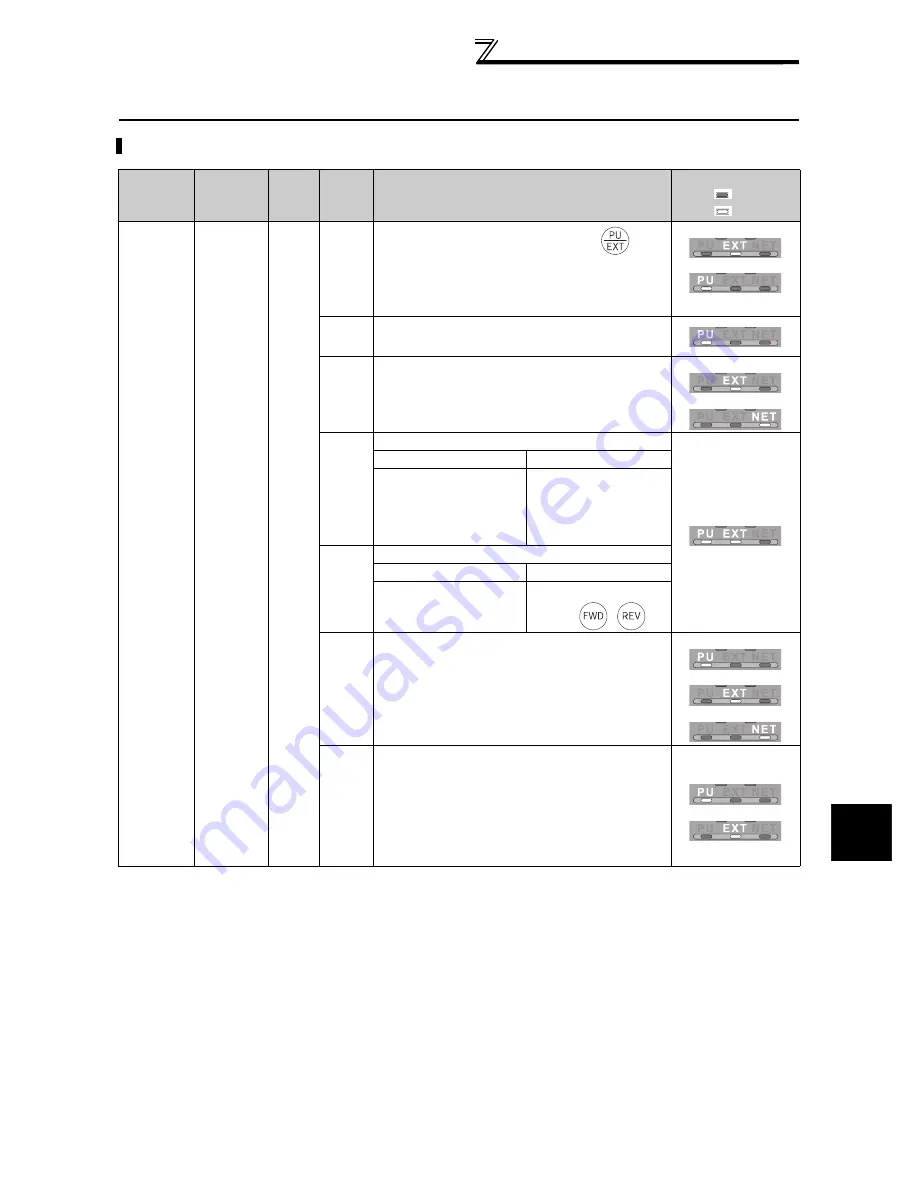
57
Selection of the operation command and
frequency command locations (Pr.79)
4
ADJ
US
TME
N
T
4.6 Selection of the operation command and frequency
command locations (Pr.79)
* For the terminal used for the X12 signal (PU operation interlock signal) input, assign "12" in
Pr. 178 to Pr. 189 (input terminal function selection)
to
assign functions.
For
Pr. 178 to Pr. 189
, refer to
the Instruction Manual (applied)
.
When the X12 signal is not assigned, function of the MRS signal switches from MRS (output stop) to PU operation interlock signal.
Select the operation command location and frequency command location.
Parameter
Number
Name
Initial
Value
Setting
Range
Description
LED Indication
: Off
: On
79
Operation
mode
selection
0
0
Use external/PU switchover mode (press
to
switch between the PU and external operation mode.
(Refer to page 34)
)
At power on, the inverter is in the external operation
mode.
External operation mode
PU operation mode
1
Fixed to PU operation mode
2
Fixed to external operation mode
Operation can be performed by switching between the
external and NET operation mode.
External operation mode
NET operation mode
3
External/PU combined operation mode 1
Running frequency
Start signal
PU (FR-DU07/FR-PU04)
setting or external signal
input (multi-speed setting,
across terminals 4-5 (valid
when AU signal turns on)).
External signal input
(terminal STF, STR)
4
External/PU combined operation mode 2
Running frequency
Start signal
External signal input
(Terminal 2, 4, 1, JOG,
multi-speed selection, etc.)
Input from the PU (FR-
DU07) (
,
)
6
Switchover mode
Switch among PU operation, external operation, and
NET operation while keeping the same operation
status.
PU operation mode
External operation mode
NET operation mode
7
External operation mode (PU operation interlock)
X12 signal ON*
Operation mode can be switched to the PU
operation mode.
(output stop during external operation)
X12 signal OFF*
Operation mode can not be switched to the PU
operation mode.
PU operation mode
External operation mode
Summary of Contents for FR-F700 Series
Page 134: ...MEMO ...