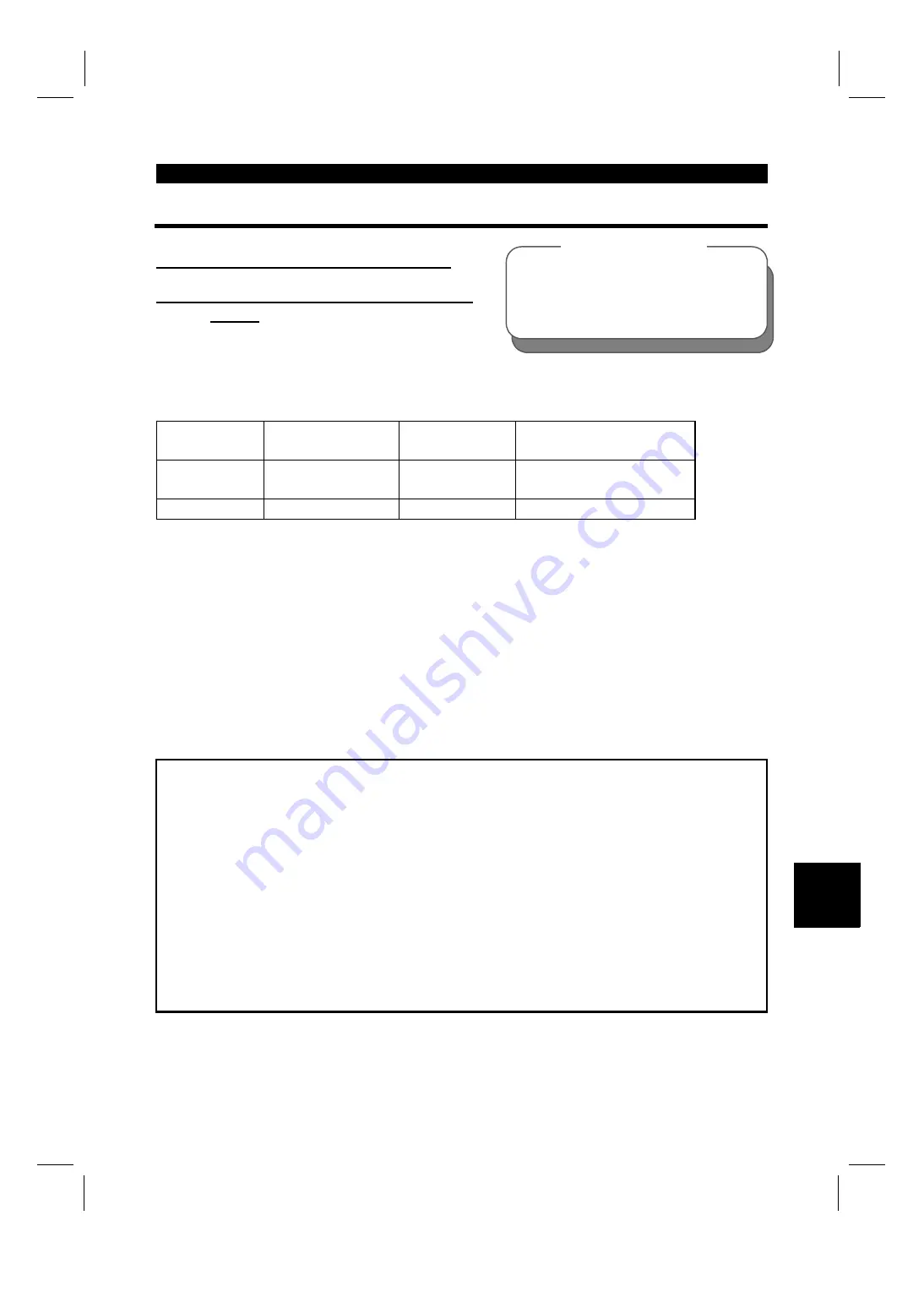
PARAMETERS
75
4.2.6 Electronic overcurrent protection (Pr. 9, Pr. 48)
Pr. 9 "electronic thermal O/L relay"
Pr. 48 "second electronic thermal O/L
relay"
Set the current of the electronic overcurrent
protection to protect the motor from overheat.
This feature provides the optimum protective characteristics, including reduced motor
cooling capability, at low speed.
Parameter
Number
Factory Setting
Setting Range
Remarks
9
Rated output
current*
0 to 500A
48
9999
0 to 500A, 9999
9999: Function invalid
*0.4K and 0.75K are set to 85% of the rated inverter current.
<Setting>
!
Set the rated current [A] of the motor.
!
Setting "0" makes the electronic overcurrent protection (motor protective function)
invalid. (The inverter's protective function is valid.)
!
When using a Mitsubishi constant-torque motor, first set "1" in Pr. 71 to choose the
100% continuous torque characteristic in the low-speed range. Then, set the rated
motor current in Pr. 9.
!
Pr. 48 "Second electronic thermal O/L relay" is made valid when the RT signal is on.
(Note 4)
Note: 1. When two or more motors are connected to the inverter, they cannot be
protected by the electronic overcurrent protection. Install an external thermal
relay to each motor.
2. When the difference between the inverter and motor capacities is large and
the setting is small, the protective characteristics of the electronic
overcurrent protection will be deteriorated. In this case, use an external
thermal relay.
3. A special motor cannot be protected by the electronic overcurrent protection.
Use an external thermal relay.
4. The RT signal serves as the second function selection signal and makes the
other second functions valid. Refer to page 148 for Pr. 180 to Pr. 183 (input
terminal function selection).
Pr. 71 "applied motor"
Pr. 180 to Pr. 183
"input terminal function
selection"
Related parameter
4