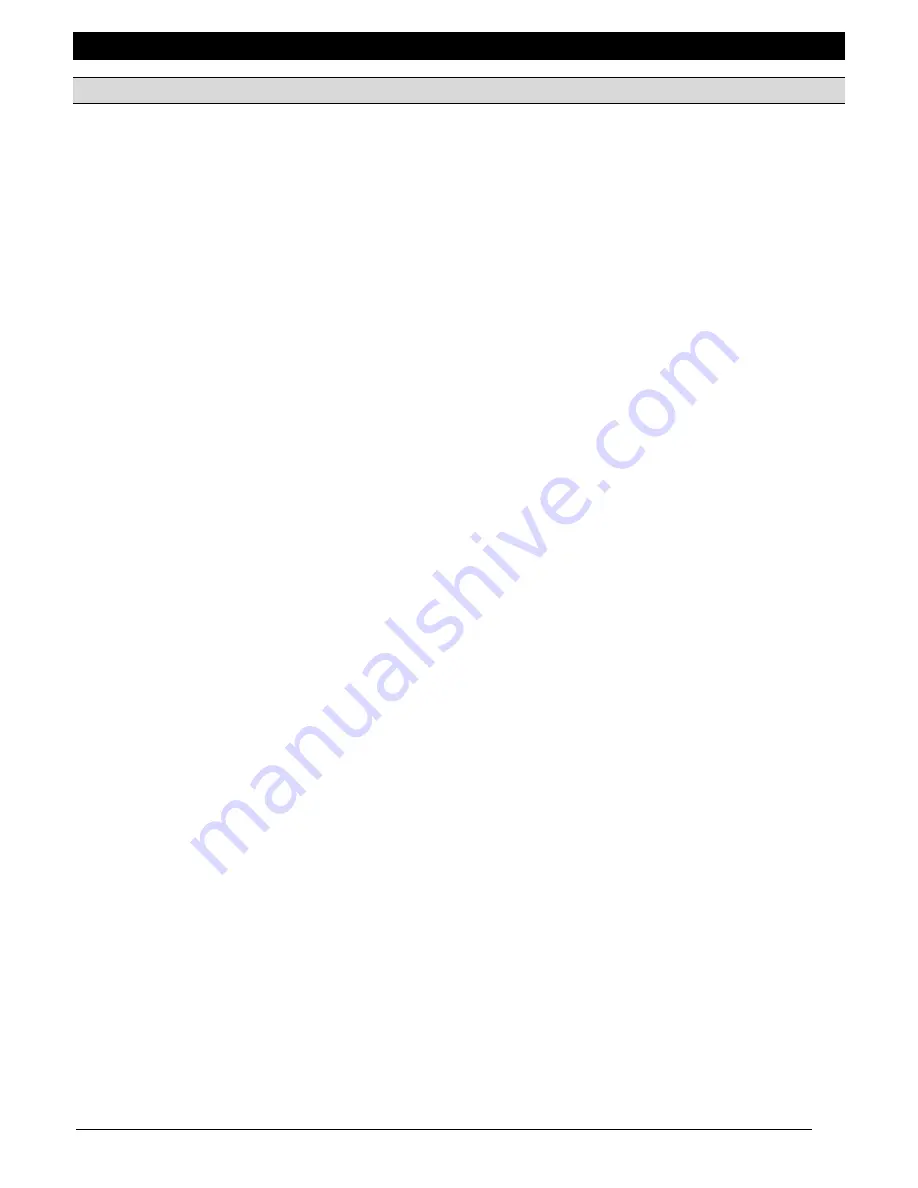
1.0
SPYDER-PLUS-S1 BASIC SETUP
www.maxcessintl.com
MAGPOWR Spyder-Plus-S1 Tension Control
MI 850A351 1 C
Page 9 of 68
1.3
OPEN LOOP TENSION BASED ON DIAMETER
This page provides a summary of the basic set-up and calibration of the Spyder control in
Open Loop Tension
mode. Additional features and options of the Spyder control are described later in this manual.
Refer to the
Open Loop Tension
screen flowchart drawing number 850B352 for a navigation aid.
1. Required connections for the basic Spyder system are:
24 VDC power (Term.6 and Term.7)
Earth ground (Term. 8)
Diameter signal (Term.38, and Term.39, see Section 5.4.4 and Figure 16 for connections.)
Tension setpoint signal (Term.15 through Term.17)
RUN/STOP using the Spyder internal logic supply between Term.9 and Term.11 (This is typically
accomplished by using a switch between these terminals.)
E-Stop jumper in place between Term.10 and Term.11. (This is supplied by default from the factory.)
Analog control output to clutch or brake amplifier, current-to-pressure transducer, motor controller, etc.
(Term.30 to Term.31, refer to Sections 5.1 and 5.3 for output configuration). The Spyder inputs and
outputs are referenced to Earth ground and the negative of the 24 VDC power.
See Sections 2.0, 8.0 and figure 16 for specific wiring requirements.
2. When using a power amplifier, set the current range jumper to the proper setting for the clutch or brake being
used. (Refer to amplifier and clutch or brake user manuals for proper settings.) The following is also required:
Power amplifier input (if used), 115 VAC for PS-90 or 24 VAC or 24 VDC for PS-24
Output from power amplifier to clutch or brake.
The Spyder output is referenced to Earth ground and the negative of the 24 VDC power.
3. Close the RUN/STOP circuit (Term.9 and Term.11) to put the Spyder into HOLD mode (see Section 5.2.1).
4. Using the Configure menu, select
Control Type = Tension, Diameter
. In the Configuration menu select the
appropriate system type. See Section 8.2.2 for the Configure menu.
5. Using the Configure menu, select
Setpoint Source = ANALOG
if the tension setpoint will be read from the
analog voltage on terminal 16. Selecting
Setpoint Source = ETHERNET
will use a software setpoint tension
which can be changed either through the Web page, or Modbus/TCP.
6. Calibrate the diameter input and the setpoint tension input (refer to Sections 8.3 and 9.3). The setpoint tension
input does not need to be calibrated if
Setpoint Source = ETHERNET
.
7. Using the Parameters menu, enter the Core diameter and the Full Roll diameter.
8. Turn tension on by opening the TENSION ON/OFF circuit (Term.13 and Term.11), and put the Spyder in RUN
mode by switching open the RUN/STOP circuit. Adjust the tension setpoint using a potentiometer (Term. 15
through Term.17).
9. Basic set-up is complete. Additional features and options are described later in this manual. Always use the
RUN/STOP feature to activate inertia compensation during stopping. See Section 9.6.8.
Summary of Contents for MAGPOWR Spyder-Plus-S1
Page 2: ......