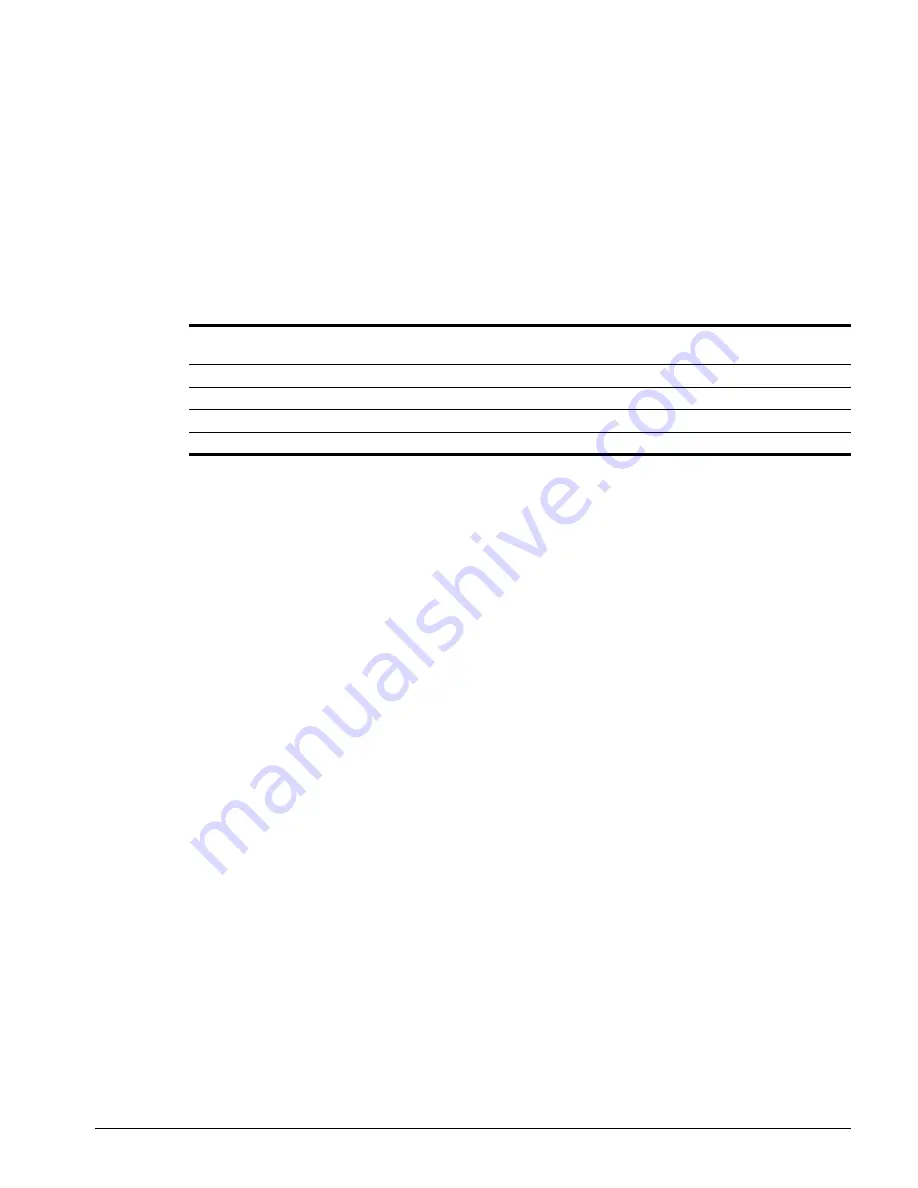
IMPULSE•VG+ Series 3 Instruction Manual - 07/25/05
3-14
Wiring the Encoder Circuit
A shaft-mounted encoder is required to provide speed and shaft position feedback to
IMPULSE•VG+ Series 3. Without an encoder, a flux vector control cannot operate properly.
Before you wire the encoder circuit, refer to the specification tables in this section and to “Wiring
Specifications.”
Encoder Circuit Wiring Procedures
Encoder Specifications
To wire the encoder circuit for IMPULSE•VG+ Series 3 (assuming the cover and keypad are
detached):
1. Direct-couple the encoder to the motor shaft, using a zero-backlash-type coupling.
NOTE:
Do not connect the encoder to the motor with roller chain or gear drive. If unable to
direct-couple the encoder, use a timing belt to drive the encoder. (Contact
Electromotive Systems for encoder kits.) Also, do not connect the encoder to the low-
speed shaft of a speed reducer.
2. Connect the encoder to the PG-T2 Encoder Interface Card. Refer to Figure 3-9: “PG-T2
Encoder Card Wiring” on page 3-15.
NOTE:
Use twisted-pair, shielded cable (Electromotive R-20/6, Belden 9730, or Brand Rex T-
11651). Strip the encoder wires .25 in. (5.5 mm). Keep the wiring length less than 300
feet. (For cable lengths greater than 300 feet, contact Electromotive Systems for
information on available fiber optic cable systems.)
3. Ground the shielded cable to Terminal TA4 of the PG-T2 Encoder Interface Card. (Ground only
one end of the shielded cable.)
NOTE:
For LakeShore encoders, the shield connection is not considered “Ground.” The
shield should be grounded at TA4 and connected to the shield at the encoder.
4. Whenever possible, the encoder cable should be wired in a continuous run between the motor
and drive. If it cannot be a direct run, the splice should be in its own junction box and isolated
from the power wires.
Power supply
+12VDC; if current demand is greater than 200 mA, an auxiliary power supply must
provided
Output Type
Quadrature (A and B channels; Z is not necessary)
Type of output circuit
High-speed, differential line driver.
Resolution
1024 PPR
Mounting method
Encoder must be direct-coupled to motor shaft, using a zero-backlash-type coupling.
Summary of Contents for IMPULSE VG+ Series 3
Page 1: ...Software 8001 X July 2005 Part Number 140 10257 Copyright 2005 Magnetek Instruction Manual...
Page 6: ...c h a p t e r 1 Introduction...
Page 7: ...IMPULSE VG Series 3 Instruction Manual 07 25 05 1 2 This page intentionally left blank...
Page 14: ...c h a p t e r 2 Installation...
Page 15: ...IMPULSE VG Series 3 Instruction Manual 07 25 05 2 2 This page intentionally left blank...
Page 23: ...IMPULSE VG Series 3 Instruction Manual 07 25 05 2 10 This page intentionally left blank...
Page 24: ...c h a p t e r 3 Wiring...
Page 25: ...IMPULSE VG Series 3 Instruction Manual 07 25 05 3 2 This page intentionally left blank...
Page 40: ...c h a p t e r 4 Programming Basic Features...
Page 41: ...IMPULSE VG Series 3 Instruction Manual 07 25 05 4 2 This page intentionally left blank...
Page 54: ...c h a p t e r 5 Programming Advanced Features...
Page 55: ...IMPULSE VG Series 3 Instruction Manual 07 25 05 5 2 This page intentionally left blank...
Page 149: ...IMPULSE VG Series 3 Instruction Manual 07 25 05 5 96...
Page 150: ...Troubleshooting IMPULSE VG Series 3 c h a p t e r 6...
Page 151: ...IMPULSE VG Series 3 Instruction Manual 07 25 05 6 2 This page intentionally left blank...
Page 170: ...A p p e n d i x A IMPULSE VG Series 3 Parameter Listing...
Page 171: ...IMPULSE VG Series 3 Instruction Manual 07 25 05 A 2 This page intentionally left blank...
Page 183: ...IMPULSE VG Series 3 Instruction Manual 07 25 05 A 14...