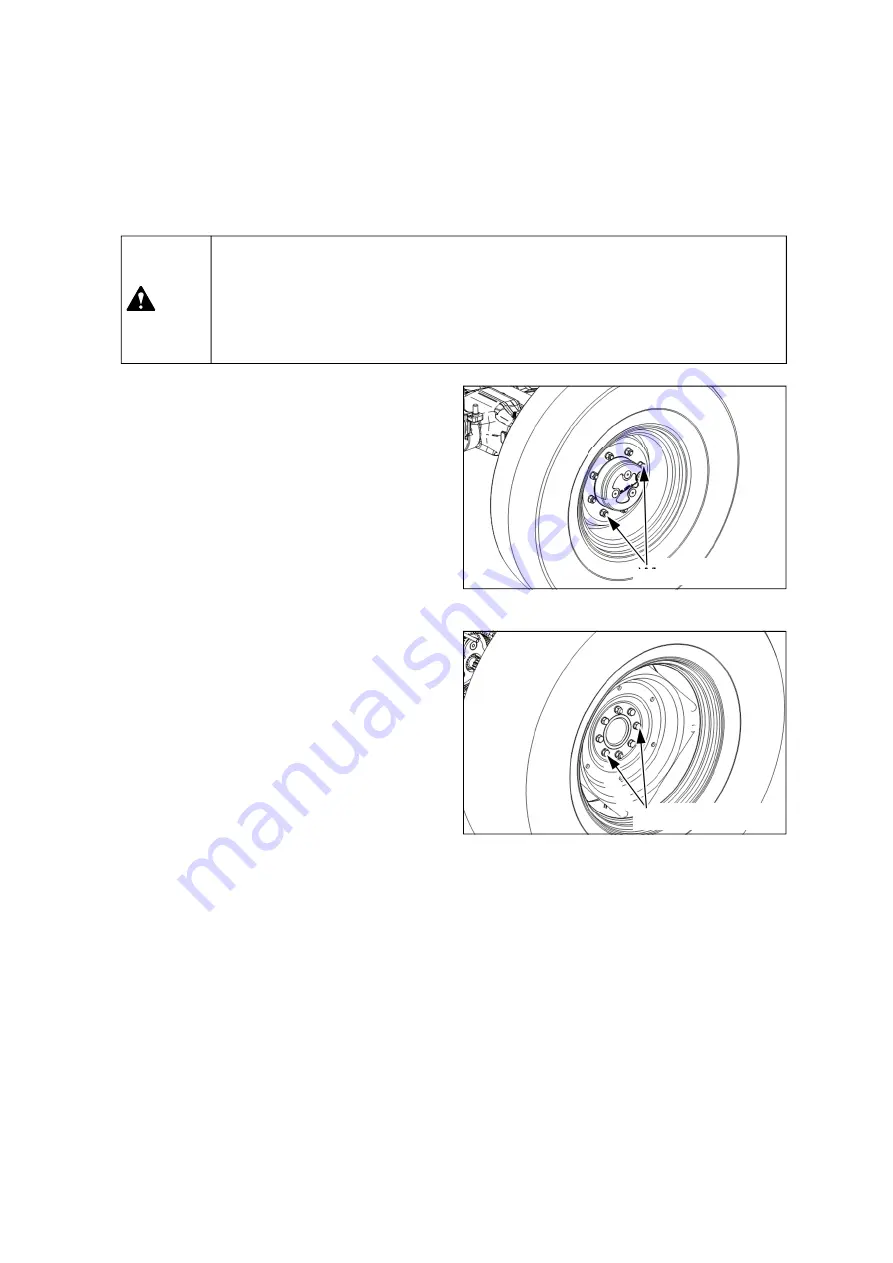
5 - 27
(9) Tightening state of bolts and nuts of each part
Check if the bolts or nuts of each part are loosened. If necessary, tighten it again. Especially, check
the bolts and nuts of the tires before starting engine, if necessary, tighten them.
Tighten the wheel bolts and nuts to the
specified torque any time you remove the
wheel assembly from the machine or loosen
the wheel bolts or nuts.
Front Wheel Torque: M18x1.5P
2500~2800 kgf.cm
(245~275 N.m, 181~203 lb.ft)
▶
Roll-over hazard!
Never operate the machine with a loose wheel rim or disc. Always tighten
nuts and/or bolts to the specified torque value and at the recommended
intervals.
Failure to comply could result in death or serious injury.
Warning
Rear Wheel Torque: M18x1.5P
2500~2800 kgf.cm
(245~275 N.m, 181~203 lb.ft)
NOTICE: Check and tighten wheel bolts and
nuts to proper torque specifications after the
following hours of use:
• First 5 hours
• First 50 hours
• Every 300 hours
Wheel bolts and nuts
Wheel bolts and nuts
Summary of Contents for XP8084
Page 1: ...LS TRACTOR OPERATOR S MANUAL XP8084 XP8094 XP8101 ...
Page 2: ......
Page 4: ......
Page 12: ......
Page 70: ......
Page 80: ...3 10 SCR inducement strategy Low DEF level ...
Page 81: ...3 11 SCR inducement strategy poor DEF quality ...
Page 82: ...3 12 SCR inducement strategy SCR System tampering detection ...
Page 188: ......
Page 261: ...5 73 Attachment ...
Page 262: ......
Page 280: ......
Page 282: ...8 2 2 Roll bar type Unit mm When applying front tire 12 4 24 8PR rear tire 16 9 34 8PR ...
Page 287: ......
Page 288: ......