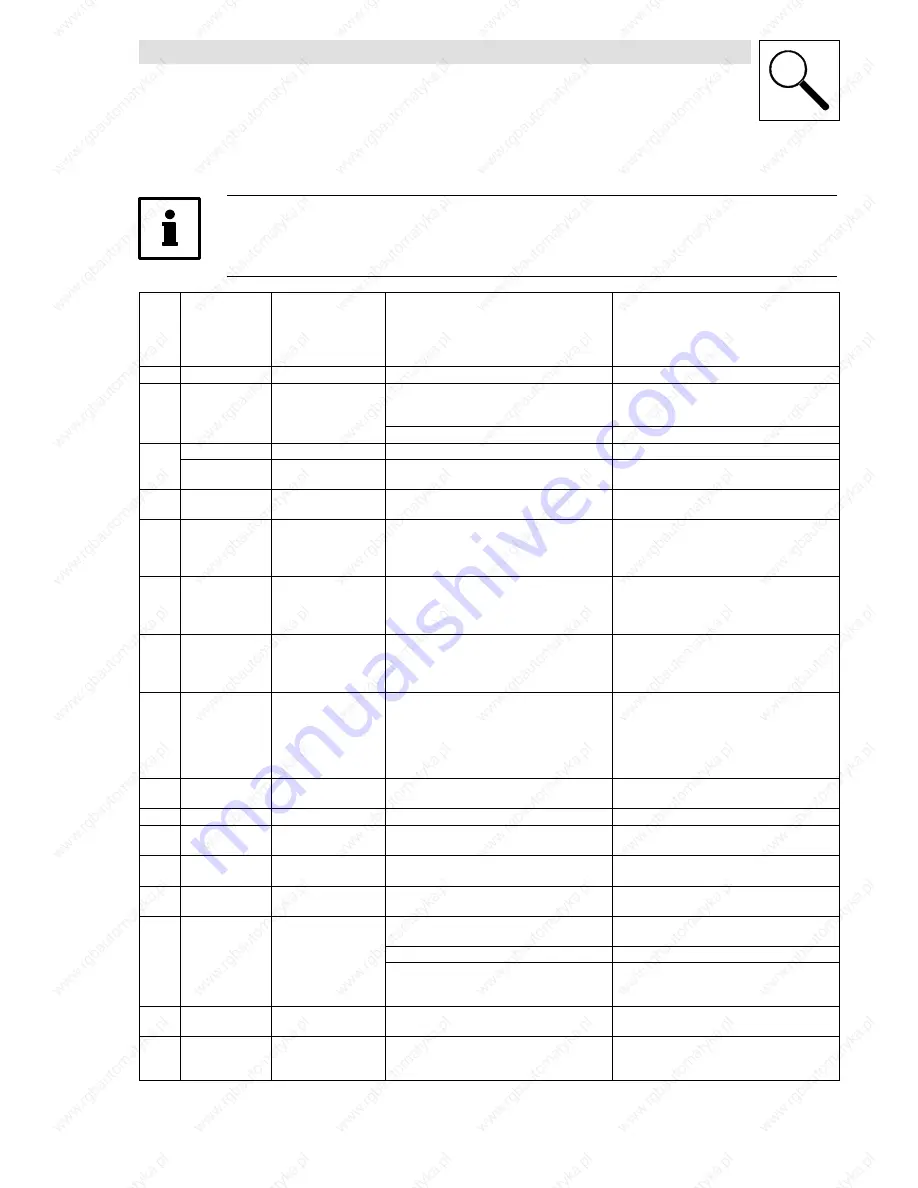
Troubleshooting and fault elimination
9-5
BA9300SU EN 2.1
9.3
Fault indications
Note!
If the fault indication is requested by a fieldbus (C0168/x), the fault indication is represented by a
fault number in column 2 of the table.
Display
Fault No.:
q
xxx
- TRIP
- Message
- Warning
- FAIL-QSP
Error
Cause
Remedy
---
---
No fault
-
-
CCr
q
071
System error
Strong interference on control cables
For 9300 cam profiler:
Selection of too many points
Screen control cables
For 9300 cam profiler:
Reduce number of points to max. 2 points per ms)
Ground or earth loops in the wiring
PE wiring.
^
4-34
CDA
q
220
Data error
Attempt to accept faulty data
New data transfer.
q
221
Data error warning
The checksum of the data transferred is not
correct.
New data transfer and check.
CE0
q
061
Communication error
Interference during transmission of control
commands via automation interface X1
Plug in automation module firmly, bolt down, if
necessary
CE1
q
062
Communication error at
the process data input
object CAN_IN_1
CAN_IN_1 object receives faulty data, or
communication is interrupted
•
Check cable at X4
•
Check transmitter
•
Increase monitoring time under C0357/1 if
necessary
CE2
q
063
Communication error at
the process data input
object CAN_IN_2
CAN_IN_2 object receives faulty data, or
communication is interrupted
•
Check cable at X4
•
Check transmitter
•
Increase monitoring time under C0357/2 if
necessary
CE3
q
064
Communication error at
the process data input
object CAN_IN_3
CAN_IN_3 object receives faulty data, or
communication is interrupted
•
Check cable at X4
•
Check transmitter
•
Increase monitoring time under C0357/3 if
necessary
CE4
q
065
BUS-OFF state
Controller has received too many incorrect
telegrams via system bus X4, and has disconnected
from the bus
•
Check wiring
•
Check bus termination (if any)
•
Check screen contact of the cables
•
Check PE connection
•
Check bus load:
•
Reduce baud rate (observe cable length)
EEr
q
091
External fault (TRIP-Set)
A digital input assigned to the TRIP-Set function has
been activated.
Check external encoder
H05
q
105
Internal error
Contact Lenze
H07
q
107
Incorrect power stage
During initialization of the controller, an incorrect
power stage was detected
Contact Lenze
H10
q
110
Sensor fault heat sink
temperature
Sensor for heat sink temperature detection
indicates indefinite values
Contact Lenze
H11
q
111
Senso fault indoor
temperature
Sensor for indoor temperature detection indicates
indefinite values
Contact Lenze
LP1
q
032
Motor phase failure
A current-carrying motor phase has failed
•
Check motor
•
Check supply module
The current limit is set too high
Set a lower current limit value under C0599
This monitoring is not suitable for:
•
Synchronous servo motors
•
at field frequencies > 480 Hz
Deactivate monitoring with C0597= 3
LU
q
030
Undervoltage
DC bus voltage is smaller than the value fixed under
C0173
•
Check mains voltage
•
Check supply cable
r
MAX
q
200
Max. speed exceeded
(C0596)
Active load (e.g. for hoists) too high
Drive is not speed-controlled, torque excessively
limited.
Check drive dimensioning.
Increase torque limit if necessary.
Summary of Contents for EVS9321-CS
Page 3: ...Operating Instructions EDB9300UES 00414796 Global Drive 9300 servo ...
Page 21: ...Technical data 3 8 BA9300SU EN 2 1 ...
Page 57: ...Installation 4 36 BA9300SU EN 2 1 ...
Page 73: ...During operation 6 4 BA9300SU EN 2 1 ...
Page 117: ...Troubleshooting and fault elimination 9 10 BA9300SU EN 2 1 ...
Page 119: ...Maintenance 10 2 BA9300SU EN 2 1 ...
Page 188: ...Appendix 11 69 BA9300SU EN 2 1 ...
Page 189: ...Appendix 11 70 BA9300SU EN 2 1 ...