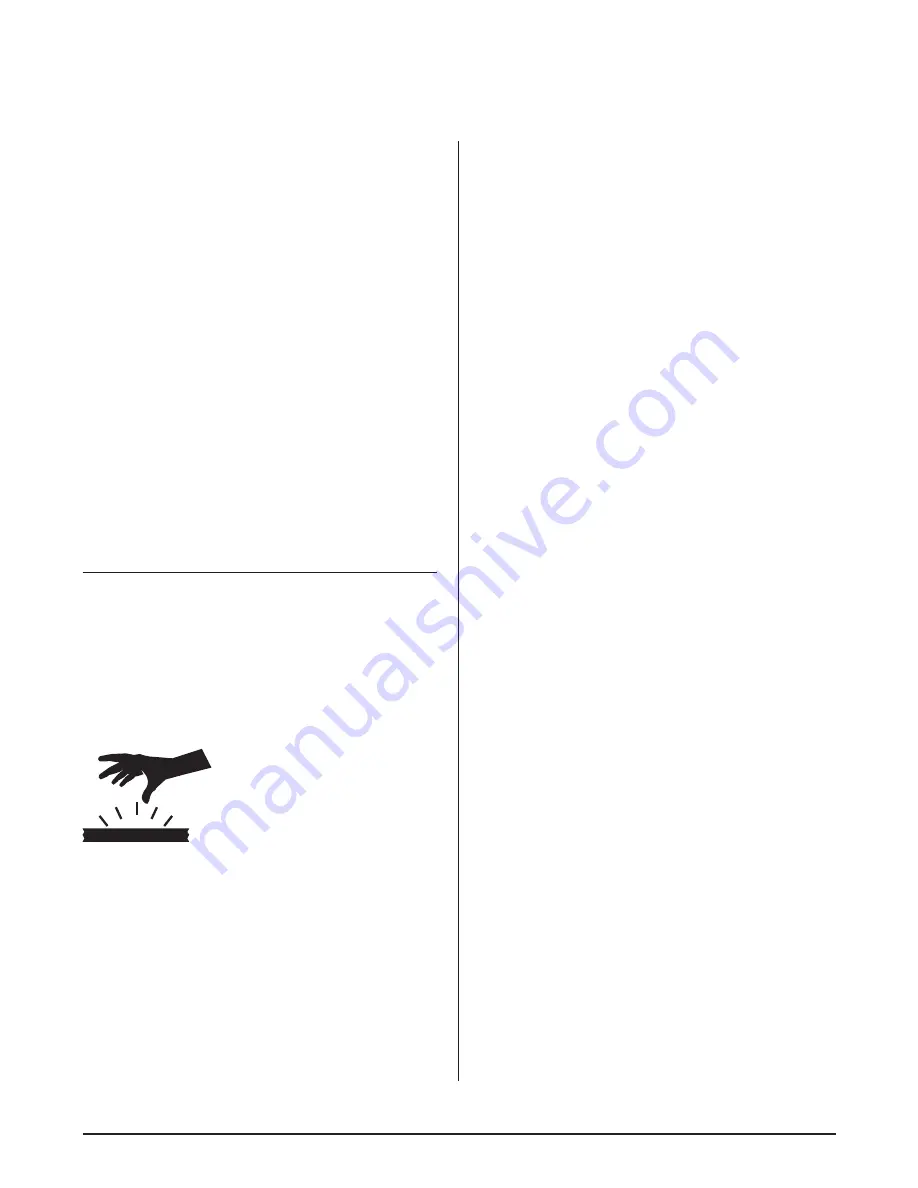
CAUTION INSTRUCTIONS FOR L&L KILNS
cautions.pdf
REV: 11/1/2016
Page 3
2016
L&L Kiln Mfg, Inc. 505 Sharptown Rd, Swedesboro NJ 08085 P:856.294.0077 F:856.294.0070 [email protected] hotkilns.com
WORK ON LIVE EQUIPMENT UNLESS ABSOLUTELY
NECESSARY!
Use the right tools for the job – do not improvise. For
instance, use a proper fuse puller; don’t use a screwdriver
to pry out an open fuse.
Protect the person; use proper gloves, shoes, and clothing.
In industry it is recommended to wear safety goggles or
face shields to prevent arc-flash or arc-blast injuries. Wear
rubber soled shoes.
Make sure the environment around the equipment being
serviced is safe. For instance, when working around
electricity, it always very dangerous for the floor to be
wet. Make sure there is adequate space to work safely.
Be aware that current flow across your chest can be fatal.
If possible, use only one hand to manipulate test leads
when conducting any necessary measurements on live
equipment. Use a clamp for one lead, and use one hand
to guide the other test lead. Keep the other hand as far as
possible from the live circuit components.
INSTALLATION CAUTIONS
USE A QUALIFIED ELECTRICIAN
1. Have electrical installation performed by an licensed
electrician or other qualified technician.
2. There is danger of electric shock.
3. There is danger that an improperly sized or installed
circuit could cause a fire.
CLEARANCES AND FLAMMABLE SURFACES
1. Make certain floor is not flammable.
2. Install kiln so that the hot surface of the kiln is no
closer than 12” (30 cm) to any wall. 18” (46 cm) is
preferable.
3. Be careful about enclosed spaces: In general, it is not a
good idea to install a kiln in a small confined space (such
as a closet).
4. Maintain a minimum of 36” (91 cm) between the hot
surfaces of two adjacent kilns, especially if they are going to
be used at the same time. (The kilns will heat each other).
5. The essential issue with kiln clearance is to keep excessive
heat from flammable surfaces. Remember, even when you
follow clearance and ventilation recommendations, the kiln
is giving off heat. Try not to place the kiln near things that
can be affected by elevated temperatures. An example
would be an electrical fuse panel which you do not want to
overheat.
CHECK TEMPERATURES AROUND KILN
1. Check temperatures around the kiln when it is at high fire
to be sure that you are not creating an unsafe condition.
2. Combustible surfaces that stay below 71°C (160°F) are
generally considered safe from the point of view of starting
a fire.
LEVELING THE KILN
1. Level the kiln while you are installing it.
2. Use thin metal shims under the legs to accomplish the
leveling (never wood or other combustible materials).
3. Make sure that the base will not wobble.
4. Leveling is important because the kiln sitter (in older
manual kilns) is affected by gravity. If the kiln is not properly
leveled the kiln sitter might be either too reactive or too
sluggish.
5. You do not want your ware to be unstable in the kiln. It
might fall over.
6. If kiln is not leveled this could lead to the cracking of the
bottom and the top. In particular, the bottom could easily
crack when you first set the weight of the kiln on the bottom
while setting up the kiln for the first time.
ADJUSTING THE HINGE PROPERLY
1. See the assembly instructions for your specific kiln.
(Assembly instructions are available at hotkilns.com/
assembly-instructions)
2. CAUTION: DO NOT attempt to disengage the spring
hinge without first reading the detailed assembly
instructions. The spring is under great pressure and
could cause severe injury if it is removed under pressure.
RELIEVE ALL SPRING TENSION BEFORE REMOVING!
OPEN LID COMPLETELY!
3. The hinge of any kiln must be adjusted so that expansion
caused by the heating process has room to expand up and
down. (L&L includes expansion slots in the hinges.)
4. An improperly adjusted hinge can damage the top kiln
rim and/or lid by compressing and breaking the brick near
the hinge.