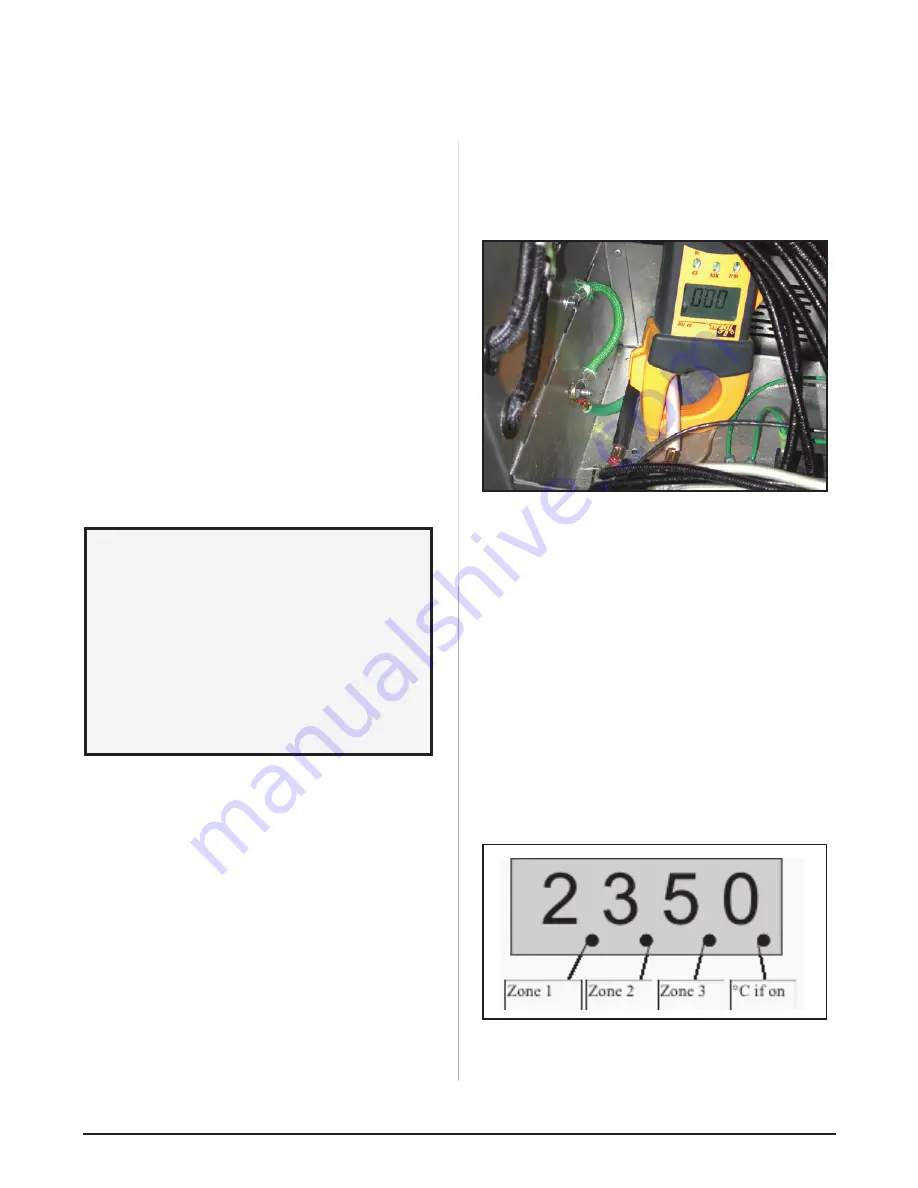
TROUBLESHOOTING AND REPAIR INSTRUCTIONS FOR L&L KILNS
troubleshoot-general.pdf
REV: 4/15/2017
Page 11
2017
L&L Kiln Mfg, Inc. 505 Sharptown Rd, Swedesboro NJ 08085 856.294.0077 F:856.294.0070 [email protected] hotkilns.com
the resistance drops far enough. In addition, the expanding
diameter of an element can make it difficult to get it out of the
holder. Usually this will not happen to those firing to higher
temperatures because the maximum temperature of the
kiln is quickly compromised by increases in the resistance,
requiring the elements to be changed long before they
can jam up in the corners. Also, high temperatures and
glaze firings are more prone to eating through the element,
causing it to fail, before the element can expand enough
to cause the problems mentioned above. Visually inspect
your elements for the above conditions and do a resistance
check. If you see this it may be time to change elements.
Power Relays
As mechanical switches, power relays will fail over time.
In particular, the coil which actuates the switch closure
increases in resistance to the point where it no longer has
the power to close, especially as it gets hot. This means
that a relay can work at low temps but fail at elevated ones,
making it more difficult to diagnose.
WIRES WILL GET HOT
Unlike many other appliances that use electricity (like
motors) kilns are called a “resistive load.” This means that
there will be a continuous pull of steady electrical power for
many hours. Even with properly sized wire this will generate
SOME heat in the wires. This is one reason we recommend
against using aluminum wire for a power feed. If you look
carefully you will see that we have OVERSIZED our internal
power wires far in excess of their rated capacity. In addition
all our power wire is rated for very high temperatures. The
larger the wires the less resistance in the wires and the
cooler they will operate.
Bad Wiring
1) Have an electrician check your wiring. We have seen
aluminum wire cause intermittent problems with allowing
enough voltage through. We do not recommend aluminum
wiring although some electricians will swear by it. The
problem with it is that aluminum oxide, which is formed
from heat, is a resistor while copper oxide is not a resistor.
With kilns you will often develop some heat in the electrical
lines. If all connections are perfect and the wire is oversized
you probably will not have a problem - but why take that
chance? Make sure your wires are of the proper size and
that all connections are good.
2) Check your circuit breaker for proper operation. These
sometimes go bad over time.
3) If all the elements are firing and the kiln is still firing too
slow check the amperage draw of the kiln under a full load.
CAUTION: This test should only be done by an experienced
person familiar with electricity and its dangers. You need to
see what the voltage is when the kiln is firing.
Check amperage under load with an amp-probe.
3) To check to see if all zones are firing on an Easy-Fire
kiln, press the number 8 on the control numeric pad. You
will see one little light per zone under the numbers on the
control display. If you see two dots on an e18S, e23S, or
e28S then you are firing at full load. If you see three dots on
an e18T, e23T, or e28T then you are firing at full load. See
if the amperage drawn is the same as what the kiln is rated
for. See the product literature and/or data nameplate on the
kiln for the rated amperage draw. There is also a complete
table of this information in the Installation Instructions part of
this manual. For instance, a model e23T rated for 240 volts,
Single Phase should draw 48.0 amps. If it is substantially
less than the rated amperage draw and your voltage is
within 5% of the rated voltage (for instance 230 volts for a
240 volt unit), then chances are the elements have changed
in resistance. This will require element replacement.
Pressing the number ”8” will turn on 2 or 3 small LEDs that
indicate whether the various zones are firing.
Wiring in the Kiln
1) Unplug kiln.