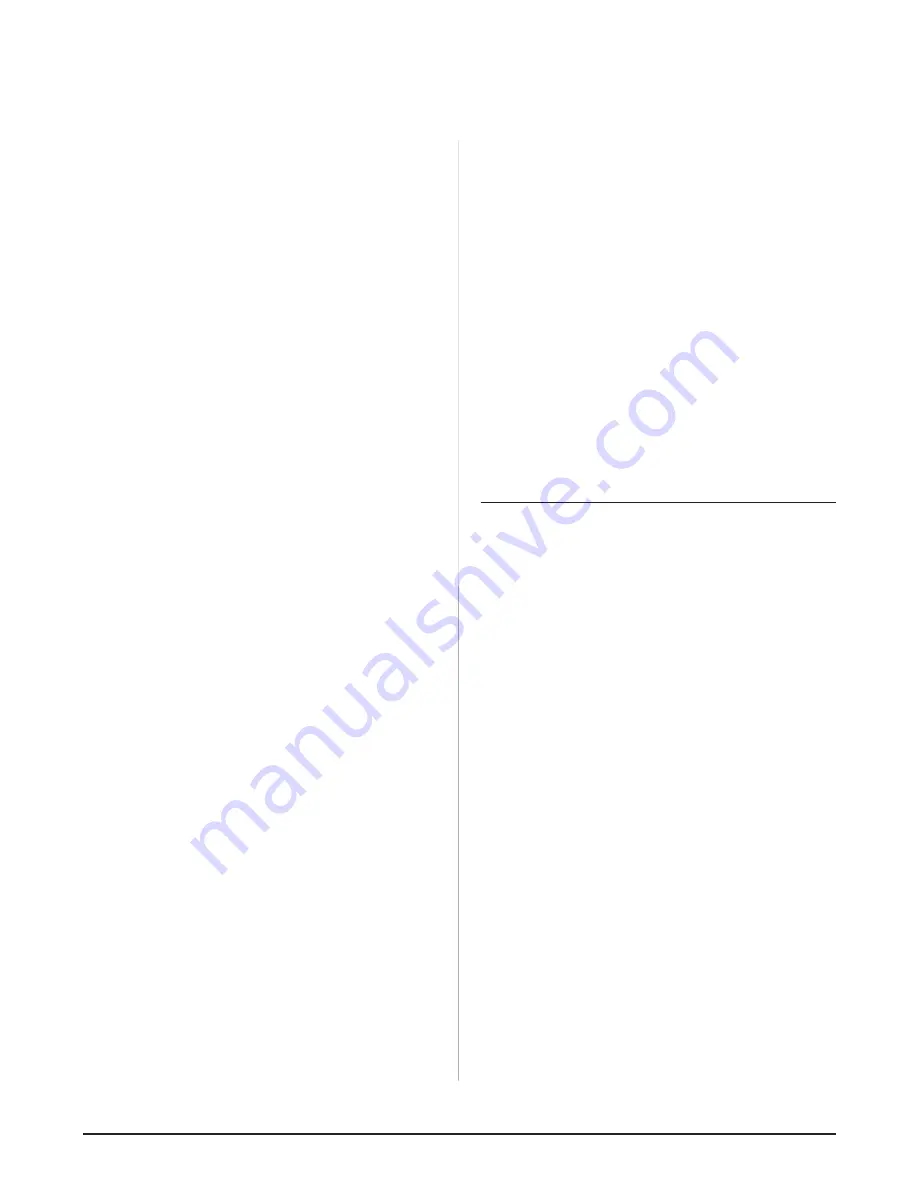
TROUBLESHOOTING AND REPAIR INSTRUCTIONS FOR L&L KILNS
troubleshoot-general.pdf
REV: 4/15/2017
Page 12
2017
L&L Kiln Mfg, Inc. 505 Sharptown Rd, Swedesboro NJ 08085 856.294.0077 F:856.294.0070 [email protected] hotkilns.com
2) Trace wiring for missing or bad connections.
3) Check wiring against wiring diagram.
4) Check for corroded connectors or connectors that have
frayed wires. Replace if you see this.
Element Connections
1) The holes where the elements go through the firebrick
walls are too large. This could cause too much heat to
escape from the kiln thereby overheating the element
terminals. This can be remedied by lightly stuffing non-RCF
ceramic fiber in the element holes. (See
hotkilns.com/
non-rcf-fiber-blanket
for non-RCF fiber). You can stuff this
in from the inside of the kiln using a sharp tool like a very
small screw driver.
2) Check to see if the element ends are twisted properly.
They should be twisted clockwise around the terminal
screw. If the twist is too loose this could generate extra heat
at the element ends. Check for corrosion on the terminal. If there
is corrosion sometimes you can remove it with a wire brush.
3) The element connection hardware may not be tight
enough. A loose connection can generate heat and cause
oxidation of the hardware which in turn will cause a worse
electrical connection (because of resistance) and more
heat. Replace with new terminal hardware. See
hotkilns.
com/parts
and filter for Model Series and Elements
(Terminals)
Heat Leakage & Vents
1) Make sure peephole plugs are in.
2) Make sure hole for vent is proper. Check Vent-Sure
instructions for proper hole sizes.
3) If you are using a different brand of vent make sure it
is the appropriate size for your kiln. Check with the vent
manufacturer and tell them how many cubic feet are in your
kiln.
4) If your lid or bottom is cracked check to see if it seems
to be leaking much heat at high temperatures. Patch or
replace if extreme. (SOME IS OK).
Adding More Insulation
1) In L&L’s top loading kilns an additional bottom may be
placed under the original bottom. This will improve the
insulation in the kiln, thereby slowing heat loss and speeding
the firing time. You can also put a 2” layer of calcium silicate
on top of the stand beneath the bottom of the kiln.
2) Also try raising the height of the kiln from the floor or
putting a reflective stainless steel or aluminum sheet under
the kiln. All these things keep the floor from absorbing the
radiant energy from the kiln and will improve heat up times
(as well as bottom of the kiln uniformity).
3) Put a 1” layer of non-RCF ceramic fiber on the lid. This
is completely non-hazardous which is important in this
application because you will be releasing fibers into the air
when you move it while loading. While this is a somewhat
extreme measure we have found that a disproportionate
amount of the heat loss from a kiln is through the top. Non-
RCF ceramic fiber is soluble in the body and is considered
totally safe.
4) Whatever you do be sure NOT to put the kiln directly on
the floor. If the floor is cement or other hard non-flammable
material it will absorb the heat from the kiln. If the floor is
wood or other flammable material you will create a very
DANGEROUS situation which could cause a serious fire.
KILN FIRES SLOWLY - EASY-FIRE
Single vs Three Zone Control
1) Three zone control will slow a kiln down. It helps even out
the temperatures in a kiln by shutting off one or more zones
while firing. In addition zone control introduces other issues
like LAG that sometimes complicate a firing. The first thing
to try if you are getting a slow firing is to switch the kiln to
single zone operation. That may get you back into operation
quickly. Then, if that makes the problem go away you can
fine tune the specific issue within the zone system that is
causing the problem.
2) Normally models e23S and e28S are programmed to have
two zones and models e23T and e28T are programmed to
have three zone control. You can easily change this to be
single zone operation.
3) Press
OTHER, 4, 4, 3
4) The display says
notC
This stands for “number of
thermocouples”.
5) To run the kiln using only one thermocouple press
ENTER
at the
notC
prompt. You will then see
0003
or
0002
(depending on whether it is currently programmed
for three zones or two zones). Then press
1
, then
ENTER
.
The display will then say
StOP
. All the zones of the kiln
will turn on and off simultaneously when you program the
DynaTrol to use only one thermocouple.