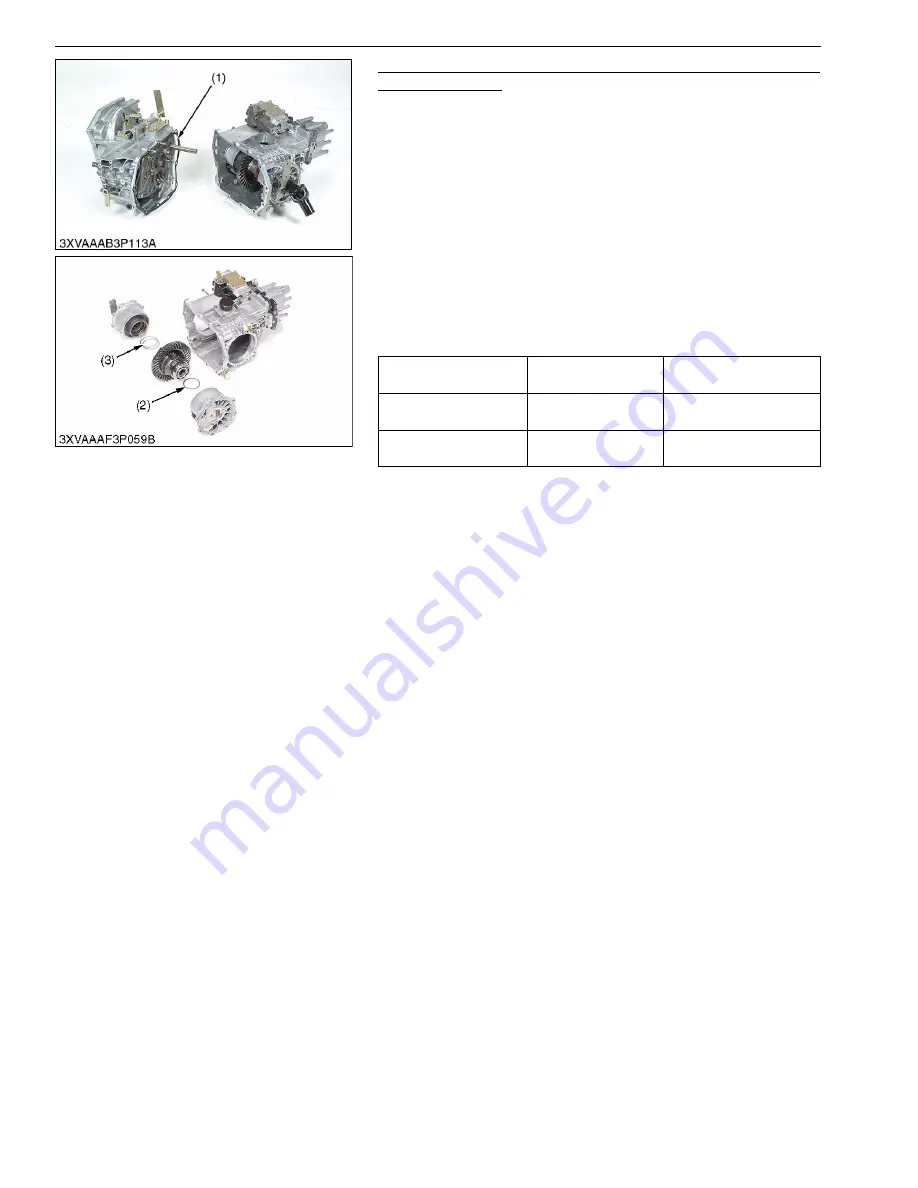
TRANSMISSION
RTV1140CPX, WSM
2-S46
Tooth Contact between 6T Spiral Bevel Pinion Shaft and 37T
Spiral Bevel Gear
• Use the transmission gasket (1) of the same thickness as the
origin first.
• Use same number of shims as before disassembling.
1. Apply red lead (or prussian blue) lightly on the teeth of spiral
bevel pinion shaft.
2. Reassemble the front case and transmission case.
In this time, set the differential lock shiftier to lock position
3. Tighten the transmission case mounting screw and nut to
specified torque.
4. Temporarily install the propeller shaft assembly and make the
propeller shaft back and forth by 2 to 3 rotations.
5. Check the tooth contact, if not proper, adjust according to the
instructions below.
(Reference)
• Thickness of gasket
0.30 mm (0.012 in.)
0.50 mm (0.020 in.)
0.80 mm (0.031 in.)
1.0 mm (0.039 in.)
• Thickness of shims (2) (LH)
0.10 mm (0.0039 in.)
0.20 mm (0.0079 in.)
0.30 mm (0.012 in.)
0.50 mm (0.020 in.)
• Thickness of shims (3) (RH)
0.10 mm (0.0039 in.)
0.20 mm (0.0079 in.)
0.30 mm (0.012 in.)
0.40 mm (0.016 in.)
0.50 mm (0.020 in.)
0.60 mm (0.024 in.)
0.70 mm (0.028 in.)
(To be continued)
Thickness of gasket (1)
Factory specification
0.50 mm
0.020 in.
Thickness of shim (LH)
Factory specification
0.70 or 0.80 mm
0.028 or 0.031 in.
Thickness of shim (RH)
Factory specification
0.70 or 0.80 mm
0.028 or 0.031 in.
(1) Gasket
(2) Shim (LH)
(3) Shim (RH)
KiSC issued 05, 2014 A
Summary of Contents for RTV1140CPX
Page 1: ...RTV1140CPX WORKSHOP MANUAL UTILITY VEHICLE KiSC issued 05 2014 A...
Page 4: ...I INFORMATION KiSC issued 05 2014 A...
Page 10: ...INFORMATION RTV1140CPX WSM I 5 9Y1210293INI0002US0 KiSC issued 05 2014 A...
Page 11: ...INFORMATION RTV1140CPX WSM I 6 9Y1210293INI0003US0 KiSC issued 05 2014 A...
Page 12: ...INFORMATION RTV1140CPX WSM I 7 9Y1210293INI0004US0 KiSC issued 05 2014 A...
Page 13: ...INFORMATION RTV1140CPX WSM I 8 9Y1210293INI0005US0 KiSC issued 05 2014 A...
Page 14: ...INFORMATION RTV1140CPX WSM I 9 9Y1210293INI0006US0 KiSC issued 05 2014 A...
Page 15: ...INFORMATION RTV1140CPX WSM I 10 9Y1210293INI0007US0 KiSC issued 05 2014 A...
Page 19: ...INFORMATION RTV1140CPX WSM I 14 5 DIMENSIONS 9Y1210293INI0012US0 KiSC issued 05 2014 A...
Page 20: ...G GENERAL KiSC issued 05 2014 A...
Page 77: ...1 ENGINE KiSC issued 05 2014 A...
Page 138: ...2 TRANSMISSION KiSC issued 05 2014 A...
Page 215: ...3 REAR AXLE KiSC issued 05 2014 A...
Page 216: ...CONTENTS 1 STRUCTURE 3 M1 MECHANISM KiSC issued 05 2014 A...
Page 227: ...4 BRAKES KiSC issued 05 2014 A...
Page 254: ...5 FRONT AXLE KiSC issued 05 2014 A...
Page 283: ...6 STEERING KiSC issued 05 2014 A...
Page 306: ...7 HYDRAULIC SYSTEM KiSC issued 05 2014 A...
Page 328: ...8 ELECTRICAL SYSTEM KiSC issued 05 2014 A...
Page 330: ...ELECTRICAL SYSTEM RTV1140CPX WSM 8 M1 1 WIRING DIAGRAM KiSC issued 05 2014 A...