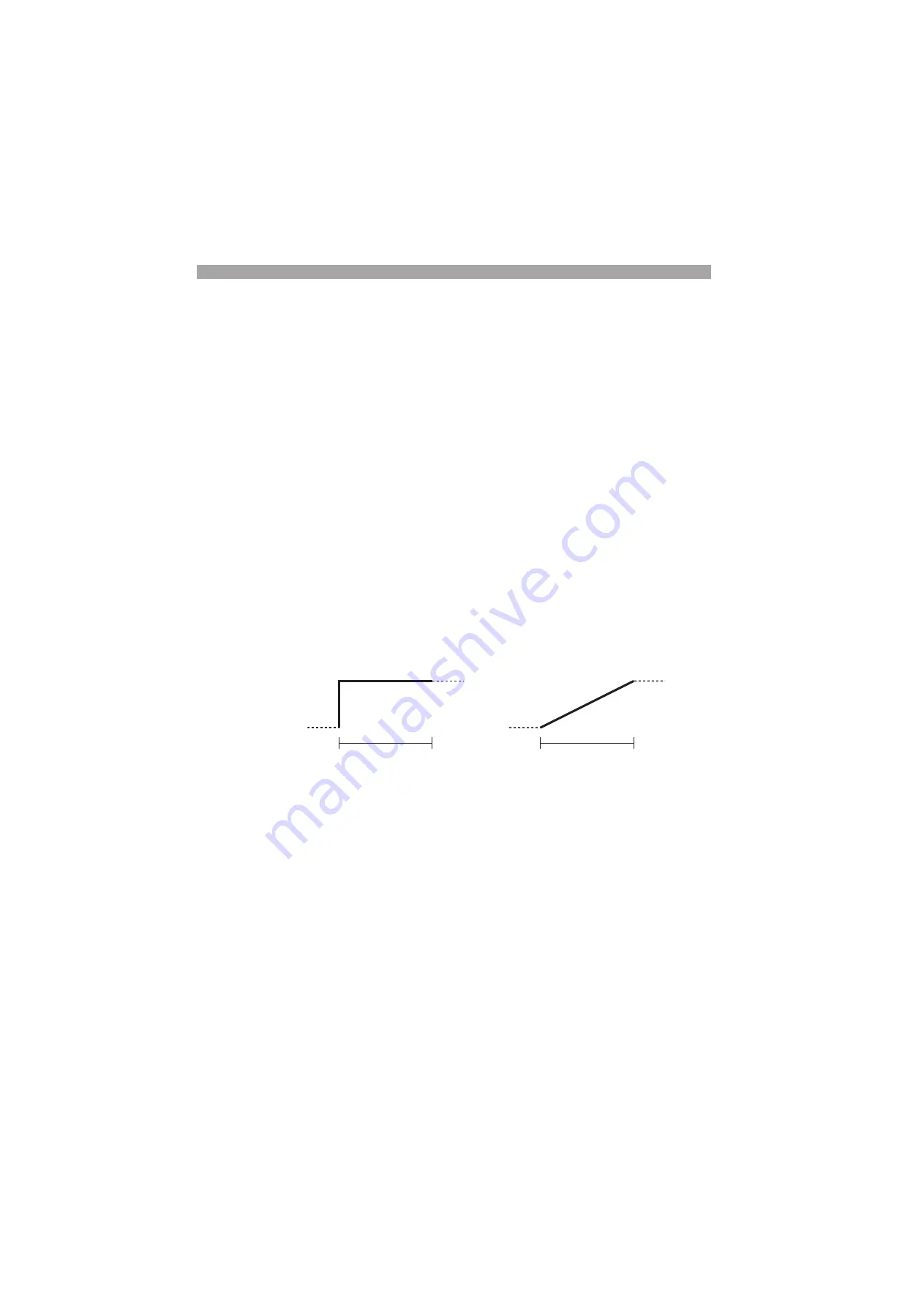
6-16 Applied Operation
PLZ-4W
• Step
In a single step, one execution condition can be speci
fi
ed. In other words, one oper-
ation of the executed waveform corresponds to one step. In normal sequence mode,
up to 256 steps can be shared among all programs (10 programs).
Below are the settings of a step.
•
Step number
•
__SET
Setting at the operation mode (A, mS, V, or W)
•
h:min:s.ms
Step execution time (0:00:00.001 to 999:59)
•
LOAD
Load or not load (OFF/ON)
•
RAMP
Current change type (ON: slope, OFF: step)
•
TRIG
Output or not output the trigger signal during step execution
(ON/OFF)
•
PAUSE
Pause or not pause during step execution (ON/OFF)
■
Step execution pattern
Of the settings of a step, the execution pattern when RAMP (current change type),
TRIG (trigger output), or PAUSE is speci
fi
ed are indicated below.
• RAMP (current transition)
RAMP sets the current transition. When turned on, the current takes on a slope
form; when turned off, the current takes on a step form.
Fig. 6-12
RAMP sequence example
(Example) Setting: 10 A
Step transition (RAMP OFF)
Step execution time: 1 s
(Example) Setting: 10 A
Ramp transition (RAMP ON)
Step execution time: 1 s
1 s
10 A
1 s
10 A
Summary of Contents for PLZ-4W Series
Page 10: ...VIII Contents PLZ 4W ...
Page 20: ...1 10 General Information PLZ 4W ...
Page 38: ...2 18 Installation and Preparation PLZ 4W ...
Page 90: ...5 30 Basic Operation PLZ 4W ...
Page 192: ...9 10 Specifications PLZ 4W ...
Page 214: ...A 22 Appendix PLZ 4W ...