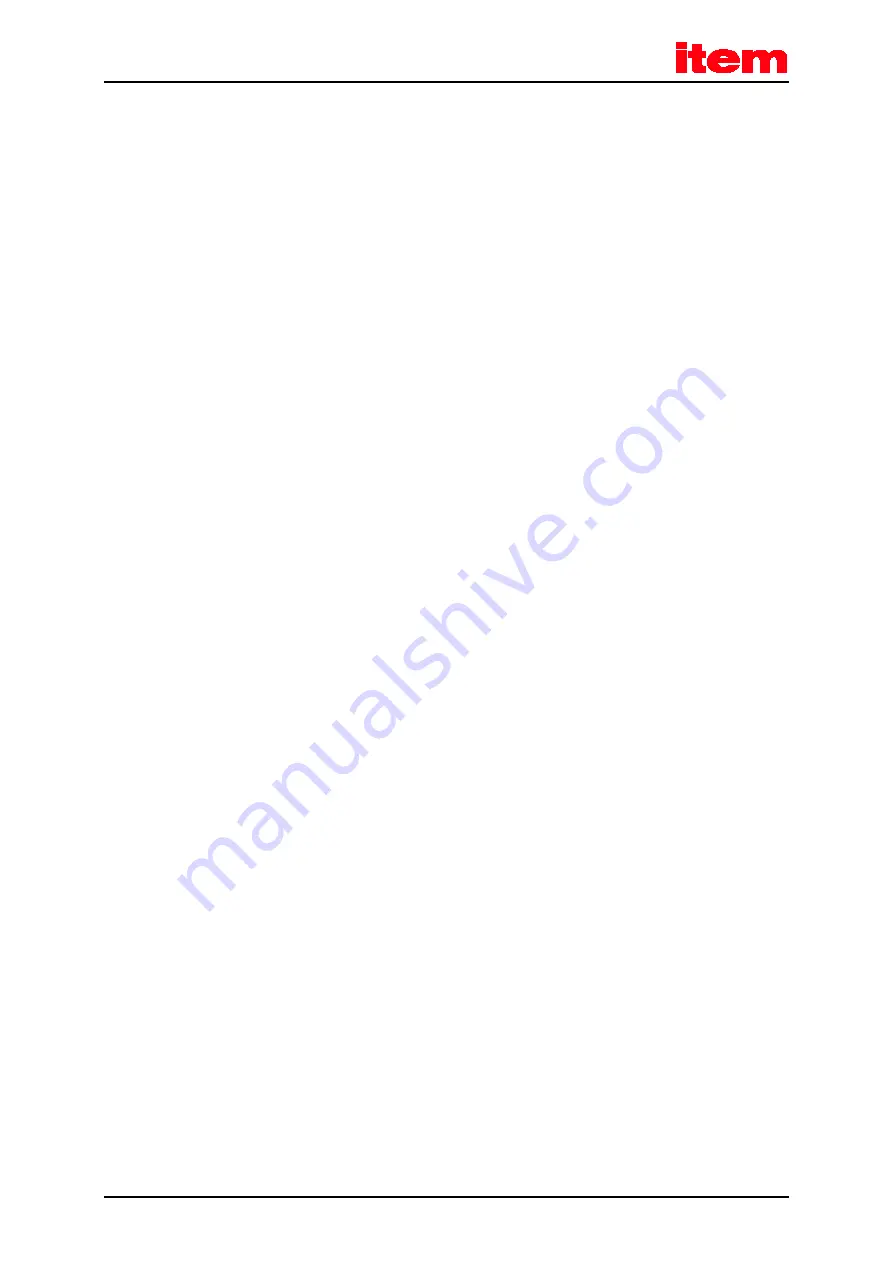
Electrical installation
Page 83
8.4
Connection: Motor [X6]
8.4.1
Device side [X6]
PHOENIX MINI-COMBICON MC1.5/9-G-5.08 BK
PHOENIX COMBICON MSTBA 2,5/9-G-5.08 BK
8.4.2
Counterplug [X6]
PHOENIX MINI-COMBICON MC1.5/9-ST-5.08 BK
PHOENIX COMBICON MSTB 2,5/9-ST-5,08 BK
PHOENIX MINI-COMBICON connector housing 12-pole,
KGG-MC1,5/12 BK
PHOENIX COMBICON connector housing 12-pole,
KGS-MSTB 2,5/9 BK
Coding to PIN 1 (BR-)