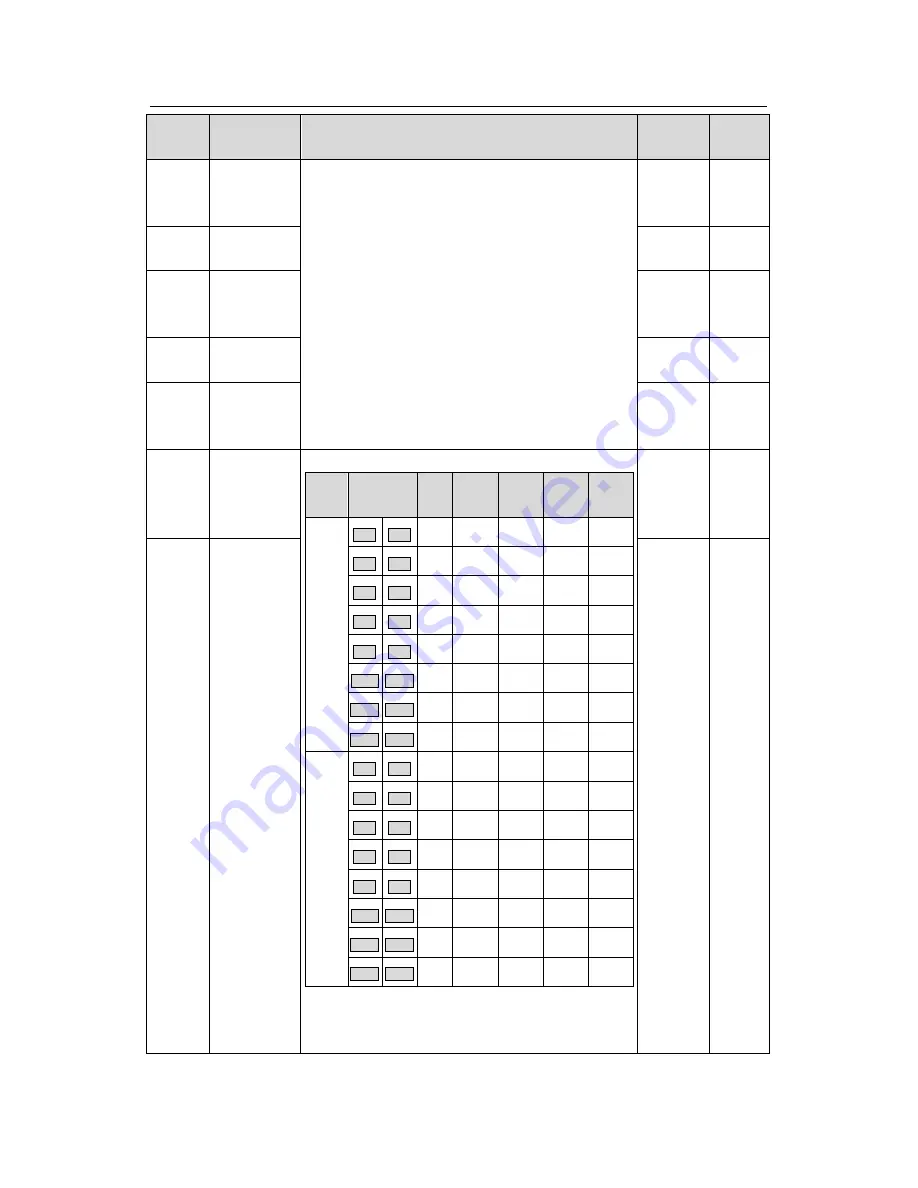
Goodrive200A
inverters Function parameters
82
Function
code
Name
Detailed instruction of parameters
Default
value
Modify
P10.29
The running
time of step
13
P10.(2n+1,1<n<17):0.0~6553.5s(min)
0.0s
○
P10.30
Multi-step
speed 14
0.0%
○
P10.31
The running
time of step
14
0.0s
○
P10.32
Multi-step
speed 15
0.0%
○
P10.33
The running
time of step
15
0.0s
○
P10.34
Simple PLC
0~7 step
ACC/DEC
time
Below is the detailed instruction:
Functio
n code
Binary bit
Step
ACC/DE
C 0
ACC/DE
C 1
ACC/DE
C 2
ACC/DE
C 3
P10.34
BIT1
BIT0
0
00
01
10
11
BIT3
BIT2
1
00
01
10
11
BIT5
BIT4
2
00
01
10
11
BIT7
BIT6
3
00
01
10
11
BIT9
BIT8
4
00
01
10
11
BIT11 BIT10
5
00
01
10
11
BIT13 BIT12
6
00
01
10
11
BIT15 BIT14
7
00
01
10
11
P10.35
BIT1
BIT0
8
00
01
10
11
BIT3
BIT2
9
00
01
10
11
BIT5
BIT4
10
00
01
10
11
BIT7
BIT6
11
00
01
10
11
BIT9
BIT8
12
00
01
10
11
BIT11 BIT10
13
00
01
10
11
BIT13 BIT12
14
00
01
10
11
BIT15 BIT14
15
00
01
10
11
After the users select the corresponding
ACC/DEC time, the combined 16 binary bits will
change into decimal bit, and then set the
0x0000
○
P10.35
Simple PLC
8~15 step
ACC/DEC
time
0x0000
○