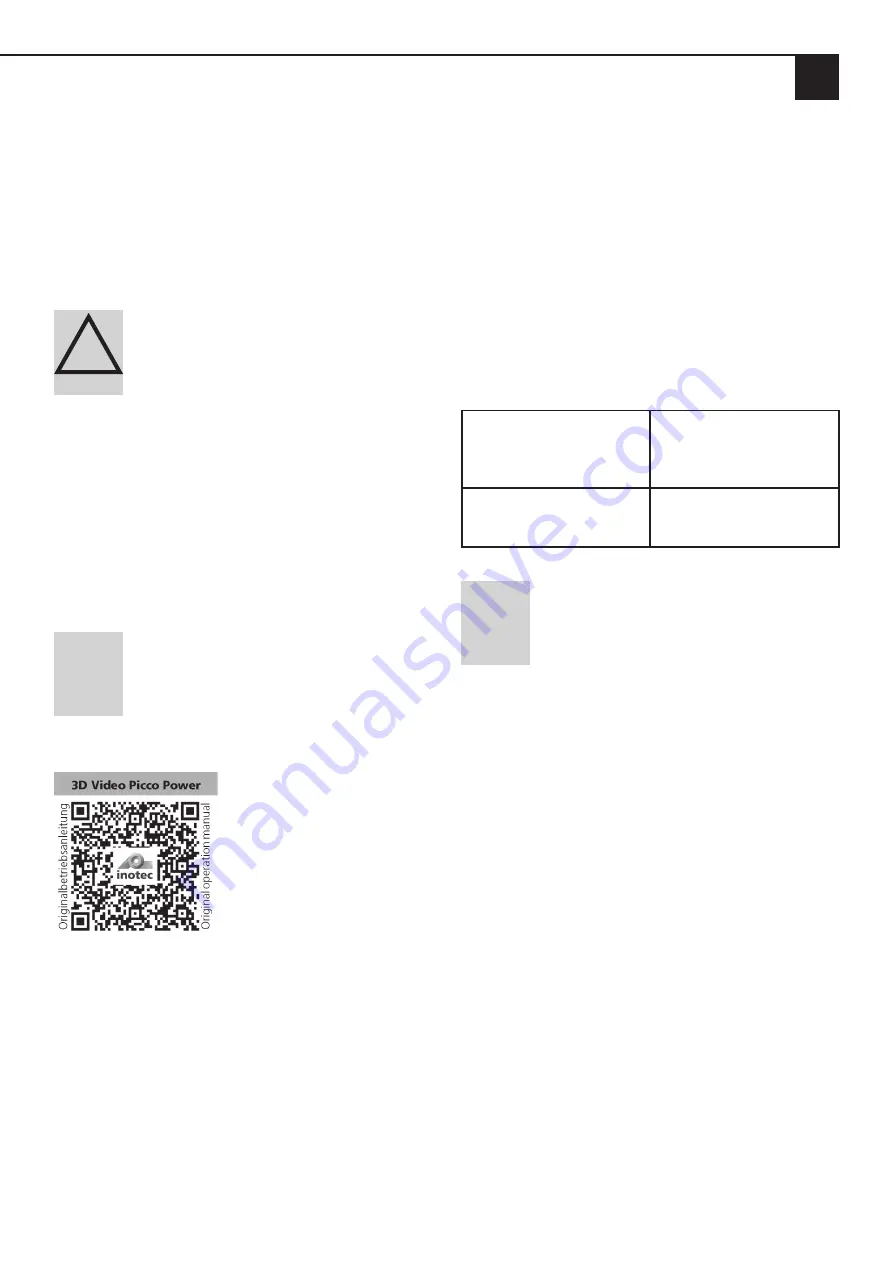
Page 31
EN
Chapter 8 Operation, use
7.3 Changing material
1. Run the material hopper of the inoCOMB Picco Power
until it is empty.
2. Then switch off the mixing pump and compressor.
3. Close the valve on the external water supply.
4. Clean the material container, mixing coil, mixing zone
and pump unit (rotor/stator/pressure gauge) incl. the
conveyor hoses used.
!
WARNING
Operation without any material or with
too little material.
Danger of destroying the rotor/stator.
If the machine is operated without any material or with too
little material, there is a risk of the rotor/stator being de-
stroyed within an extremely short period of time (< 1 min.)!
7.4 Change of location on the construction site
The inoCOMB Picco Power is equipped with four wheels.
This allows it to be conveniently moved around the con-
struction site. To do this, disconnect the mixing pump from
the electricity and water supply.
NOTE
This QR code will take you to the 3D ani-
mation of the assembly and the function of the mix-
ing pump.
8 Operation, use
8.1 Checking operating performance
1. If you notice any deviations in the operating behaviour,
decommission the inoCOMB Picco Power immediately.
2. Ensure that the damage and/or defects which led to the
deviating operating behaviour are rectified.
8.2 Checking the consistency of the material
Ensure an even, paste-like material consistency during
operation.
• The viscosity may change, especially in warm weather
conditions.
Material too rigid
Increase the water supply
by re-adjusting it on the
needle valve of the water
fitting
Material too runny
Reduce the water supply by
re-adjusting it on the nee-
dle valve of the water fitting
NOTE
Ensure that the change in consistency
may take some time to become noticeable, depending
on the length of the hose. Therefore, adjust the water
supply at the needle valve only by turning it a small
amount each time.
8.3 Correcting flow fluctuations
1. Check the water inlet screen and clean it if it is dirty.
2. Check the water pressure at the supply line and regulate
it accordingly, if necessary.
3. Check the pressure reducer and regulate it, if necessary.
8.4 Work break/end of work
If the duration of a work break exceeds the setting time of
the material to be processed, there is a risk of the material
setting during the break.
1. In the event of short interruptions of the pump process
(up to approx. 15 min., depending on the material),
close the air valve and the material valve on the spray-
ing device.
2. In the event of longer interruptions, the machine must
be run until it is empty and then cleaned.
Summary of Contents for inoCOMB Picco Power
Page 41: ...Page 41 EN Chapter 13 Systems 13 3 Circuit diagram for compressor...
Page 42: ...Page 42 EN Chapter 13 Systems 13 3 1 Circuit diagram for mixer motor safety switch...
Page 44: ...Page 44 EN Chapter 13 Systems 13 3 3 Circuit diagram for pump rotation speed...
Page 45: ...Page 45 EN Chapter 13 Systems 13 3 4 Switching cabinet subplate inside...
Page 46: ...Page 46 EN Chapter 13 Systems 13 3 5 Switching cabinet outside...