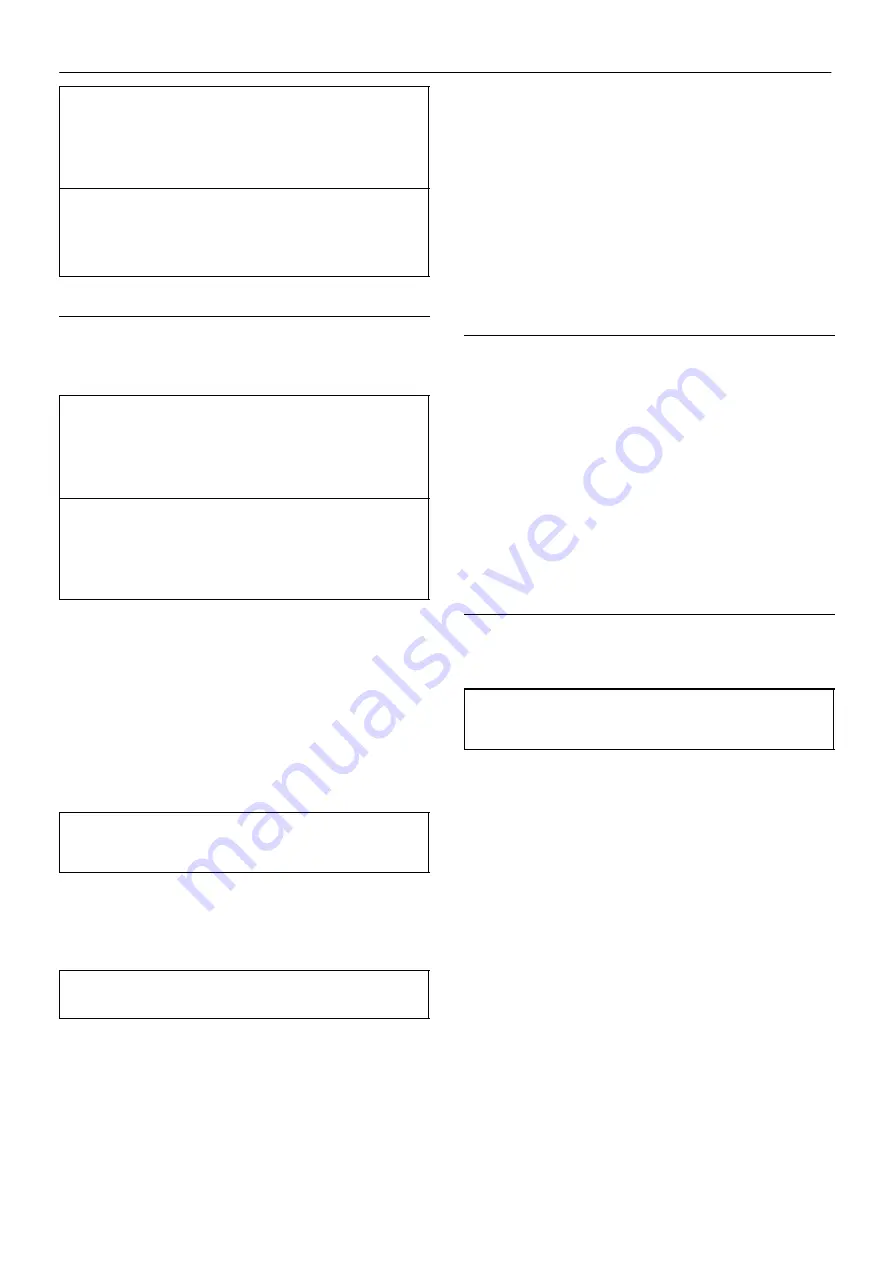
INSTALLATION / HANDLING
43
SL, SM & SH 90, 110, 132, 150, 200, 250 &300 (50Hz)
L, H & HH 125, 150, 200, 250, 300, 350 & 400 (60Hz)
CAUTION
Screw type compressors [1] should not be installed in air
systems with reciprocating compressors without means of
isolation such as a common receiver tank. It is recommended that
both types of compressor be piped to a common receiver using
individual air lines.
CAUTION
The use of plastic bowls on line filters and other plastic air line
components without metal guards can be hazardous. From a
safety stand-point, metal bowls should be used on any
pressurised system.
DISCHARGE PIPING
Discharge piping should be at least as large as the discharge
connection of the compressor. All piping and fittings should be suitably
rated for the discharge pressure.
WARNING:
All air pressure equipment installed in or connected to the
machine must have safe working pressure ratings of at least the
machine rated pressure, and materials compatible with the
compressor lubricant
(refer to the GENERAL INFORMATION
section).
WARNING:
If more than one compressor is connected to one common
downstream plant, effective check valves and isolation valves
must be fitted and controlled by work procedures, so that one
machine cannot accidentally be pressurised / over pressurised by
another.
The built–in intercooler and aftercooler reduces the discharge air
temperature well below the dew point (for most ambient conditions),
therefore, considerable water vapour is condensed. To remove this
condensation, each compressor is furnished with two moisture
separator/solenoid valve combinations. Since these solenoid valves
discharge at different pressures, it is extremely important that
they are
piped separately to an open drain.
A dripleg assembly and isolation valve should be mounted near the
compressor discharge. A drain line should be connected to the
condensate drain in the base.
NOTICE:
The drain line must slope downward from the base to work
properly.
It is possible that additional condensation can occur if the
downstream piping cools the air even further and low points in the
piping systems should be provided with driplegs and traps.
CAUTION:
Do not use the compressor to support the discharge pipe.
It is essential when installing a new compressor [1], to review the
total air system. This is to ensure a safe and effective total system. One
item which should be considered is liquid carryover. Installation of air
dryers [3] is always good practice since properly selected and installed
they can reduce any liquid carryover to zero.
To assure long trouble free operation of a compressor operating with
ON–LINE OFF–LINE control, such as the Sierra, the system volume
must be large enough to keep the load/unload cycles to a minimum
(greater than 2 minutes). This may require the installation of a receiver
down stream of the compressor.
We strongly recommend to locate an isolation valve close to the
compressor and to install line filters [4].
PRIOR TO STARTING
If the electric motor/control wiring should become exposed or
saturated with moisture/water deposits, it must be safely dried off
before attempting to make any part or conductor electrically live.
Ensure all persons concerned are suitably competent with electrical
installations.
Ensure that there is a safe working procedure which has been
issued by supervisory personnel, and that it is understood by all
persons concerned with the operation of the compressor.
Ensure that the safety procedure to be applied is based on the
appropriate national regulations.
Ensure that the safety procedure is followed at all times.
ELECTRICAL CONNECTION
Feeder cables should be sized by a competent electrical engineer
to meet all power requirements.
IMPORTANT
Ensure that the control circuit is connected to the transformer
tapping that matches the supply voltage.
COOLING WATER PIPING
Isolation valves with side drains should be installed on both the inlet
and outlet water piping lines.
Carefully inspect your water system before installing the
compressor package. Ensure that the piping is free of scale and
deposits that may restrict water flow to the Sierra package.
Proper operation of your compressor requires that the water flow
listed below is provided at a maximum supply temperature of 27
_
C
(80
_
F).
Higher temperatures up to 46
_
C (115
_
F) can be achieved by
increasing the flow.