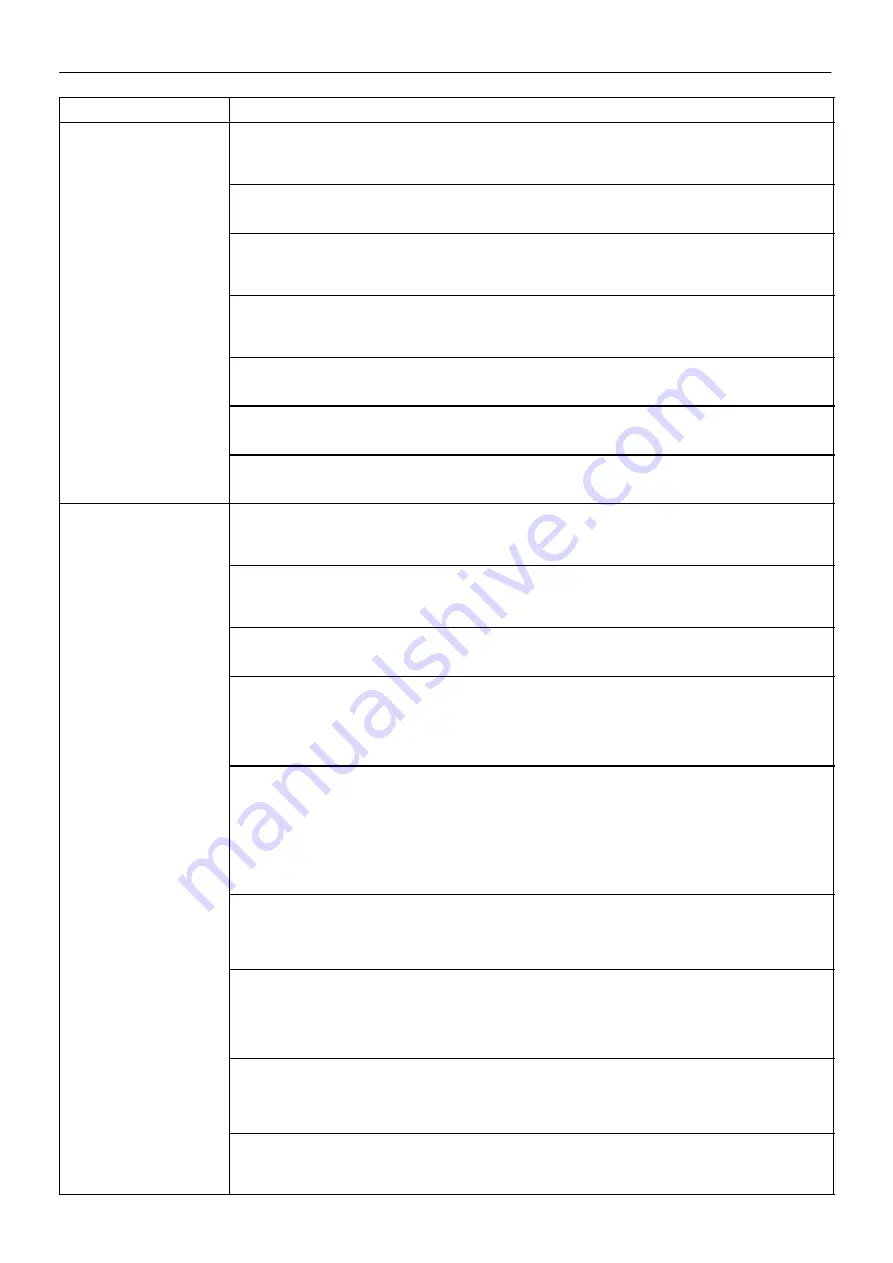
TROUBLE SHOOTING
66
SL, SM & SH 90, 110, 132, 150, 200, 250 &300 (50Hz)
L, H & HH 125, 150, 200, 250, 300, 350 & 400 (60Hz)
PROBLEM
REMEDY
Compressor fails to start.
110/120V CONTROL VOLTAGE NOT AVAILABLE.
“CK CONTROL PWR / PHASE”
Check the fuse. Check the transformers and wiring connections.
”EMERGENCY STOP”
Rotate emergency stop button to disengage, and press reset button twice.
”STARTER FAULT (1SL OR 2SL)”
Inspect starter auxiliary contacts, connections and wiring.
Inspect contactors. Replace if defective.
”MAIN (OR FAN) MOTOR OVERLOAD”
Manually reset main (or fan) motor overload relay, and press reset button twice.
Run unit and compare actual amps with name plate for possible action.
”SENSOR FAILURE”
Check for defective sensor, bad sensor connection or broken sensor wires.
INTELLISYS 24VAC CONTROLL VOLTAGE NOT AVAILABLE.
Check fuses.
DISPLAY PANEL AND POWER ON LIGHT DOES NOT ILLUMINATE.
Check wiring. Verify 24VAC is within voltage tolerance (
15%)
Compressor shuts down.
NOTE:
If a shutdown occurs, press the status button once to activate the display table. Using the adjacent up and
down arrows, the values displayed will be those immediately preceding shutdown. These values may be benefi-
cial when fault finding.
”HIGH 2ND STAGE TEMP”
Ensure that installation area has adequate ventilation. Fan side of intercooler may be dirty or plugged, clean as
required.
”HIGH l/C PRESS, UNLOAD”
Check position of inlet throttle valve, adjust to be 0.3 mm (0.012”) open.
”INLET RESTRICTION”
Check for obstructions in air intake system. Verify that 2nd stage discharge temperature in the unload reduces
slowly from the temperature in the load mode. If the unload temperature is greater, adjust the inlet/unloading valve.
(Note: The inlet vacuum under the inlet/unloading valve should be approximately 0.87 bar (13 psi) in the unload
mode).
”LOW BRG OIL PRESS”
Check oil level in gearcase sight glass. The level should be between
3
/
4
to
4
/
4
full.
Check complete machine for oil leaks.
Oil filter may be dirty or plugged. Replace filter.
Remove tube on discharge side of oil relief valve to determine if valve is leaking. Replace valve if leaking.
Remove flex line from vent side of hydraulic cylinder. If a large amount of oil exits the cylinder, overhaul hydraulic
cylinder valve assembly.
Remove oil pump to inspect tang drive. Replace pump and/or drive assembly if found defective.
”HIGH I/C PRESS, LOADED”
Check for air leaks between 2nd stage discharge flange and discharge check valve.
Check discharge safety relief valve for leakage. Replace valve if leaking.
Check discharge manual condensate valve to ensure that it is closed.
”HIGH 1ST STAGE TEMP”
Ensure that installation area has adequate ventilation.
Ensure that cooling fan is operating.
Ensure that inlet control hydraulic cylinders is fully stroking when compressor is loaded. Replace inlet/unloading
assembly if it is found defective.
”HIGH BRG OIL TEMP”
Ensure that installation area has adequate ventilation.
Fan side of oil cooler may be dirty. Clean as required.
Thermostat element in oil temp control valve may be defective.
”HIGH I/C AIR TEMP”
Ensure that installation area has adequate ventilation.
Fan side of intercooler may be dirty or plugged. Clean as required.