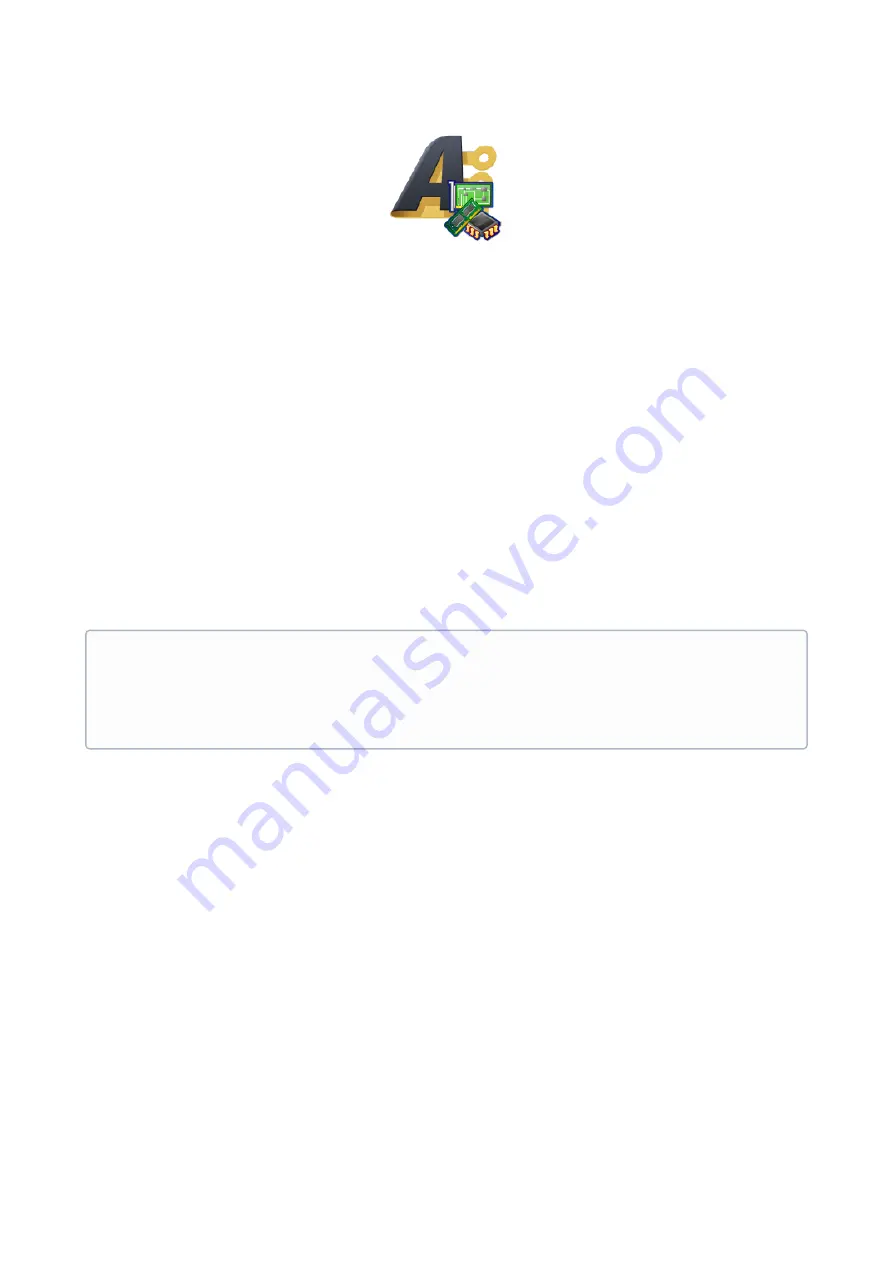
Everest CORE - Product Manual |
Application Guide
INGENIA | 08/01/2019
52
•
Altium Integrated Library:
contains the symbols and footprints for Everest CORE as well as for the required
PCB mating connectors and power pin contacts.
•
Altium Device Sheet Module:
allows to easily add Everest CORE plus all the components required to plug it
to an Altium project.
•
Altium Project Example:
simple Altium project template where the Everest CORE module has already been
added to schematic and PCB.
7.3.2. The Everest CORE component
The Everest CORE is not directly plugged to a PCB, but instead it uses components to be plugged to, either along
the direct solder or the pluggable approach. This means that the Everest CORE component does not have any
terminals, and the Interface board must be set with the terminals of the required mating components, which are:
•
Signal connectors:
60-pin and 80-pin mezzanine male mating connectors (see
section for more
info).
•
Power pin receptacles:
mating terminals (Mill-Max 9801-0-15-15-23-27-10-0) for pluggable approach or TH
holes for soldered approach. Both are disposed as independent components, yet the holes do not entail any
BOM (only copper).
Additionally, fixing holes for M2.5 screws are required to fix the aluminium chassis to the Interface board.
Notice this means that the Everest CORE component does not have any copper in its footprint. The copper is in the
mating and fixing elements listed above. To set it right, the PCB component does include some critical information
in various of its mechanical layers:
•
Mechanical layer 5:
can be used as a positioning guide for the required mating and fixing elements.
•
Mechanical layer 10:
contains the bounding boxes and designators for each component, used to generate
the Assembly Drawing 2D output. If the Everest CORE is flipped from Top to Bottom layer, this information
should move to Mechanical layer 11, according to the defined layer pairs this component has been created
with.
•
Mechanical layer 13:
contains the 3D body of Everest CORE in a native STEP AP214 format (STEP file alone
can be downloaded from the
•
Mechanical layer 15:
contains critical information on clearances to nearby components, as well as routing
considerations.
Mechanical layer 5: positioning guide
This mechanical layer contains useful mechanical data, including the centre of all the mating and fixing elements,
as well as their diameters or bounding boxes. It also includes a full footprint representation of the 2 mezzanine
connectors, with the full pinout specified, plus their proper orientation with first and last pins marked.
Plugged vs. Soldered approach
Pluggable approach would require terminals P1, P2, P3, P4 and P5 (Mill-Max 9801-0-15-15-23-27-10-0),
while soldered approach would require holes H1, H2, H3, H4 and H5. In the Device Sheet Module attached
both sets of elements are superposed in the PCB (this might be shown as a component clearance conflict).
Whichever is the selected approach, remove the components for the other from schematic, and update
the PCB. When only 1 of the 2 sets of components remain in the PCB, the conflict should be gone.