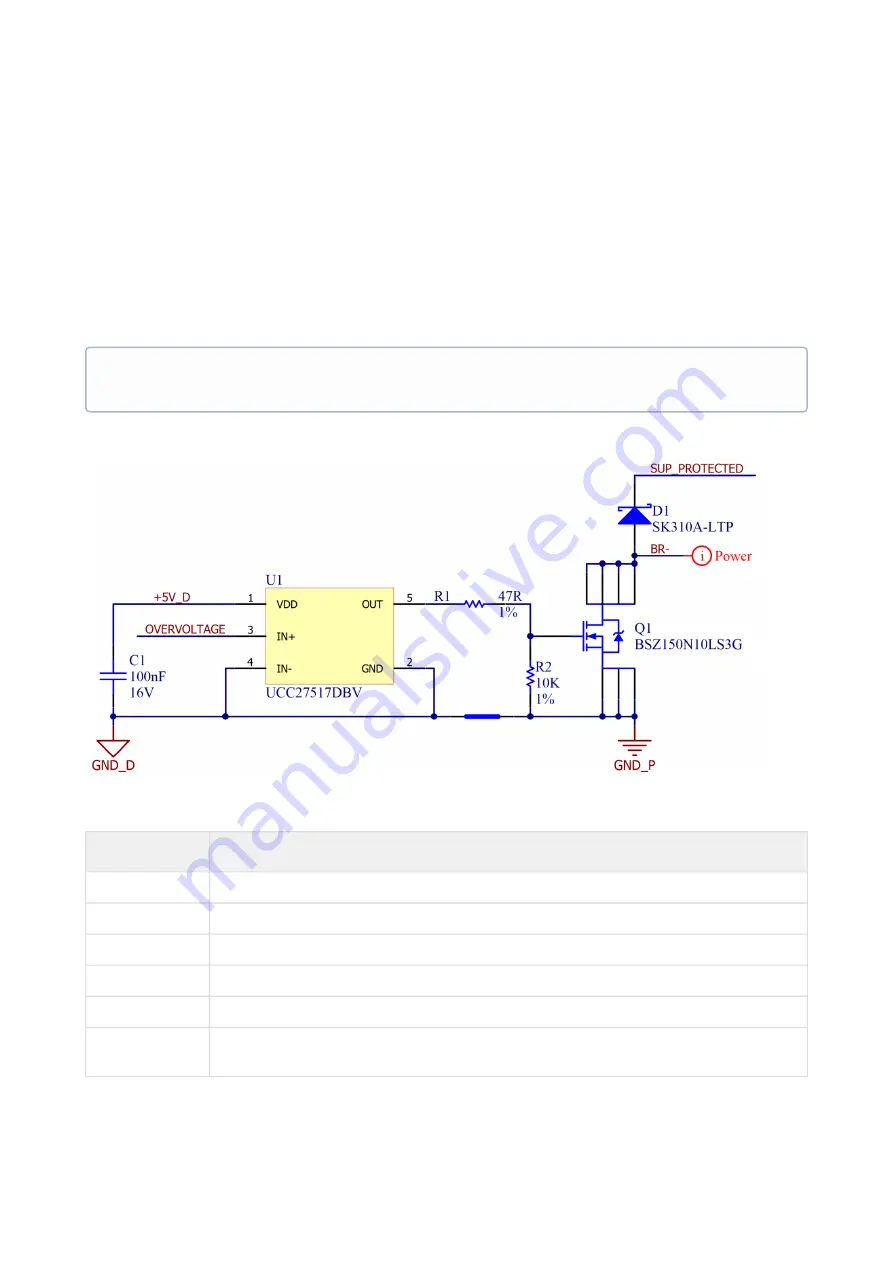
Everest CORE - Product Manual |
Application Guide
INGENIA | 08/01/2019
32
•
The system is battery powered:
in this specific case, the re-injection charges the battery. In some
applications, like electric vehicles, this might even be an advantage, as it would extend the battery life.
However, care must be taken in ensuring that the re-injected current measured in the battery terminals is
not beyond its maximum charging ratings. Also, when the battery is fully charged this method cannot be
used.
•
Get rid of the excess of energy:
Here a transistor is used to short the DC bus to Ground through a power
resistor, which would dissipate the excess of energy as heat. This method has proved to be the most
effective (and the less efficient) but has the drawback of requiring a very bulky resistor, which is costly and
space-consuming. This method can be implemented with the circuit proposed below.
To learn more about motor re-injection and how to dimension the power resistor, check the following document:
•
Dimensioning a Shunt Resistor for Regenerative Braking
Schematic
Signals description
Signal
Description
+5V_D
+5 V Logic supply
OVERVOLTAGE
To be connected to any of the GPOx pins of Everest CORE Interface connector
SUP_PROTECTED To be connected to power pin 1 of P1 in Everest CORE
BR-
To be connected to the negative terminal of the power resistor
GND_P
Power supply reference voltage. To be connected to power pin 2 of P1 in Everest CORE
GND_D
Logic supply reference voltage. To be connected to pins 39, 59 or 60 of Everest CORE Interface
connector
Multi-axis systems
Notice that in multi-axis systems or even when multiple drives share a same DC bus only 1 braking resistor
is needed. Even some advanced power supplies have a braking resistor already integrated.