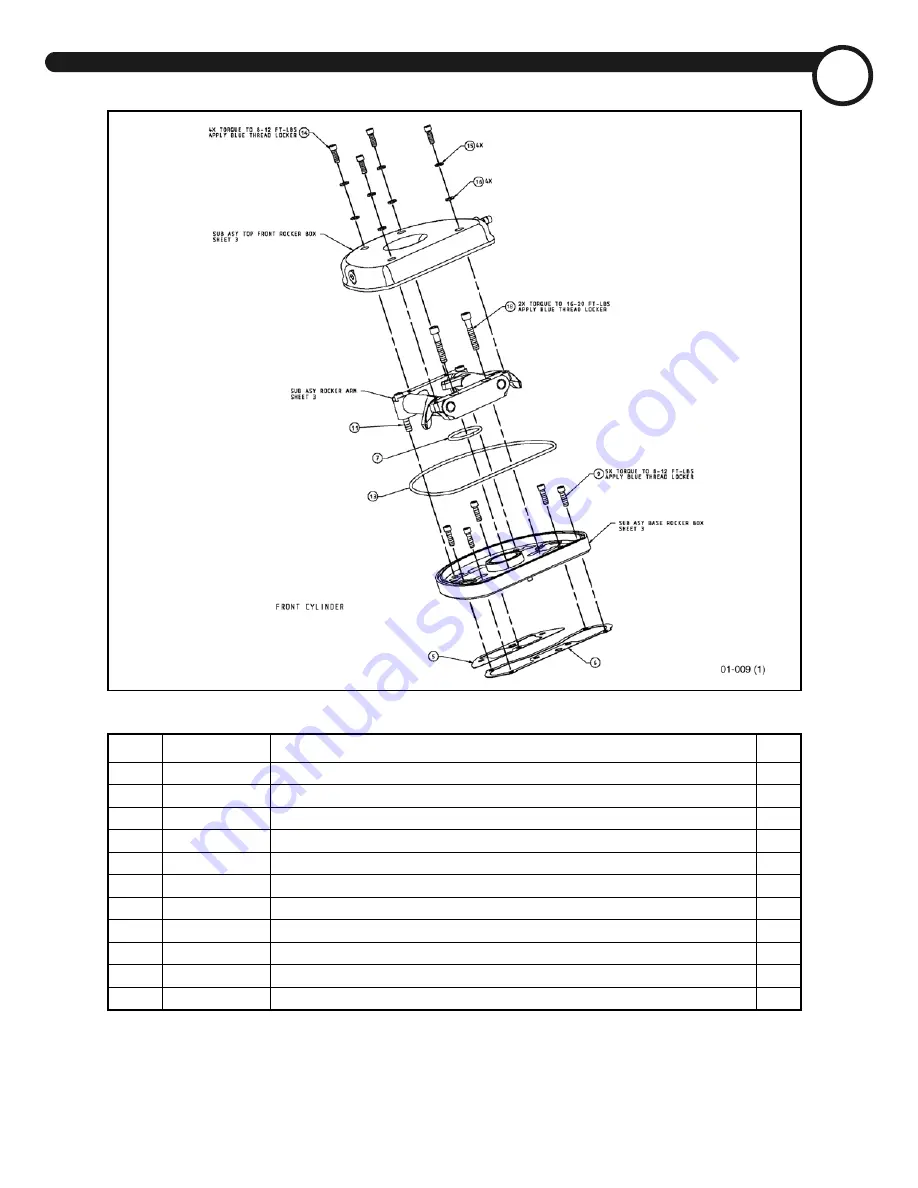
*/%*"/$)*&'7*/5"(&4&37*$&."/6"-
"44&.#-:%3"8*/(4
283
Figure 578 — Front cylinder rocker assembly
Item
Part Number
Part Description
Qty.
5
01-257
Gasket, lower right
1
6
01-258
Gasket, lower left
1
7
01-260
O-ring, small
1
9
96-296
Screw, socket head, 1/4"-20 x 7/8"
5
11
96-297
Screw, socket head, 5/16" x 18 x 1-3/4"
2
13
01-259
O-ring, large
1
14
97-121
Screw, socket head, 1/4"-20 x 3/4"
4
15
96-201
Washer, flat
4
16
01-924
Washer, vulcanized
4
18
96-298
Screw, socket head, 5/16"-18 x 2"
2
—
01-201
Rocker box, front (does not include rockers, shafts or girdles)
1
Summary of Contents for 2003 Chief Vintage
Page 1: ...P N 98 173 ...
Page 3: ...ii 05 4 7 5 4 37 6 ...
Page 15: ...6 05 4 7 5 4 37 6 ...
Page 25: ...16 5306 4 005 7 5 4 37 6 Figure 12 Typical operation check screen ...
Page 129: ...120 6 4 45 7 5 4 37 6 BSCVSFUPS MMVTUSBUJPOT Figure 232 Carburetor right side ...
Page 130: ... 7 5 4 37 6 6 4 45 121 Figure 233 Carburetor left side ...
Page 131: ...122 6 4 45 7 5 4 37 6 Figure 234 Carburetor exploded view ...
Page 160: ... 7 5 4 37 6 151 Figure 290 Cylinder head assembly ...
Page 206: ... 7 5 4 37 6 65 197 Figure 409 Clutch assembly ...
Page 235: ......
Page 269: ...260 4 5 4 7 5 4 37 6 44 4 8 3 3 4 Figure 552 Front chassis harness diagram ...
Page 270: ... 7 5 4 37 6 4 5 4 261 Figure 553 Rear chassis harness diagram ...
Page 271: ...262 4 5 4 7 5 4 37 6 5 0 4 45 3 Figure 554 POWERPLUS 100 engine ignition system ...
Page 296: ... 7 5 4 37 6 44 3 8 4 287 Figure 582 Engine assembly ...
Page 299: ...290 05 4 7 5 4 37 6 ...
Page 305: ...296 05 4 7 5 4 37 6 ...