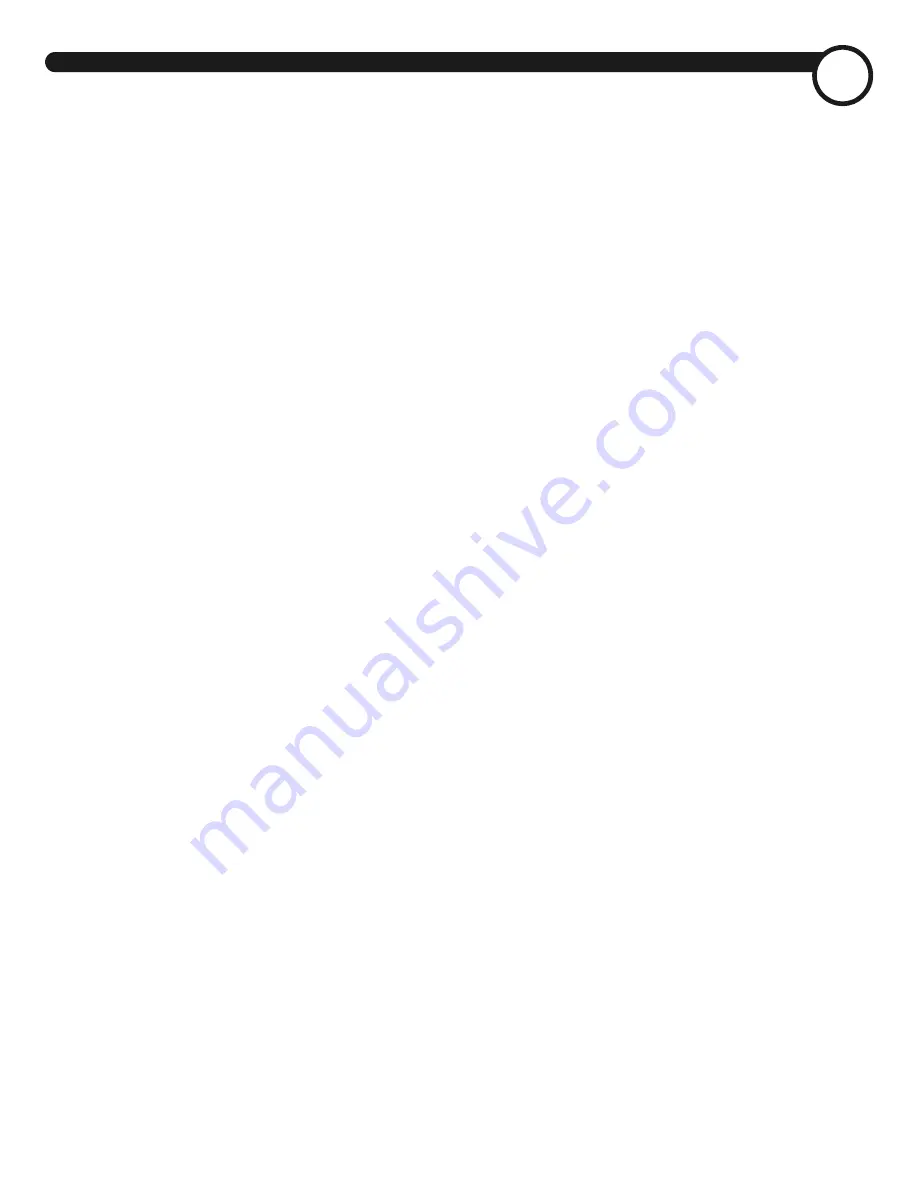
*/%*"/$)*&'7*/5"(&4&37*$&."/6"-
5306#-&4)005*/(
11
Starter does not operate or does not turn engine over:
•
Engine stop switch in OFF position
•
Ignition switch not in ON position
•
Discharged battery or loose or corroded
connections
•
Connector to starter loose
•
Poor or loose starter ground connection
-VCSJDBUJPO4ZTUFN
Oil does not return to oil tank:
•
Insufficient amount of oil in system
•
Oil lines or fittings clogged
•
Oil filter clogged
•
Inoperative oil pump
Oil leaks from cases, pushrod covers and/or hoses:
•
Loose parts
•
Incorrect or imperfect seal at gaskets, pushrod
cover, washers, etc.
•
Restricted oil return line to tank
•
Restricted crankcase vent
#BTJD&OHJOF5FTUT
The cylinder leakage and compression checks are basic
engine tests that will help determine the overall
mechanical condition of the engine and identify
problems that can prevent the engine from delivering
peak performance.
$ZMJOEFS-FBLBHF5FTU
With the cylinder leakage test, air pressure is applied to
the cylinder. A drop in pressure indicates a leak.
Run the engine to attain normal operating temperature.
Stop the engine.
Clean the area around the spark plug with compressed
air and remove the spark plug.
Position the piston, in the cylinder being tested, at top
dead center (TDC) on the compression stroke.
Remove the air filter and set the throttle and choke in
the wide-open position.
Place the transmission in 5th gear and engage the rear
brake to prevent the engine from turning over.
Using a cylinder leakdown tester, follow the
manufacturer’s instructions to perform a leak test on the
cylinder (maximum acceptable leakdown rate is 15%).
Listen for air escaping at the following locations:
•
Exhaust pipe — indicates a defective exhaust valve
•
Head gasket — indicates defective head gasket,
cylinder head surface or cylinder surface
•
Carburetor — indicates defective intake valve
•
Crankcase vent — indicates worn piston rings
Air escaping through the valves may indicate incorrect
pushrod length. Check that the correct length pushrods
are installed in each location.
&OHJOF$PNQSFTTJPO5FTU
The engine compression test provides a quick method
to uncover engine faults.
Make sure the battery is fully charged.
Run the engine to attain normal operating temperature.
Stop the engine.
Clean the areas around the spark plugs with compressed
air and remove the spark plugs.
Remove the air filter and set the throttle in the wide-
open position.
Install a compression gauge in the cylinder being tested.
Have an assistant crank the engine at least four
complete compression strokes and record the
compression readings. Repeat the test on the second
cylinder, and compare the readings.
If the highest readings from both cylinders are within
specification, 150-195 psi, the engine compression is
satisfactory. If the engine compression is not to
specification, the cause may be one of the following:
•
Worn piston rings — If compression is low on the
first stroke, increases on successive strokes, but
never achieves specification, the piston rings may
be worn. Add a tablespoon of heavy oil into the
cylinder and crank the engine to distribute the oil.
Repeat the compression test. If the compression
readings increase considerably, the rings are worn.
•
Faulty valve seating — If compression is uniformly
low on all strokes, the valves may not be seated
properly. Add a tablespoon of heavy oil into the
cylinder and crank the engine to distribute the oil.
Repeat the compression test. If the compression
readings remain approximately the same, the valves
are not seated properly (perform cylinder leakage
test). Check that the correct length pushrods are
installed in each location.
•
Head gasket leak — If compression is uniformly
low on all strokes, the head gasket may be leaking.
If the compression readings are below specification,
perform the Cylinder Leakage Test.
Summary of Contents for 2003 Chief Vintage
Page 1: ...P N 98 173 ...
Page 3: ...ii 05 4 7 5 4 37 6 ...
Page 15: ...6 05 4 7 5 4 37 6 ...
Page 25: ...16 5306 4 005 7 5 4 37 6 Figure 12 Typical operation check screen ...
Page 129: ...120 6 4 45 7 5 4 37 6 BSCVSFUPS MMVTUSBUJPOT Figure 232 Carburetor right side ...
Page 130: ... 7 5 4 37 6 6 4 45 121 Figure 233 Carburetor left side ...
Page 131: ...122 6 4 45 7 5 4 37 6 Figure 234 Carburetor exploded view ...
Page 160: ... 7 5 4 37 6 151 Figure 290 Cylinder head assembly ...
Page 206: ... 7 5 4 37 6 65 197 Figure 409 Clutch assembly ...
Page 235: ......
Page 269: ...260 4 5 4 7 5 4 37 6 44 4 8 3 3 4 Figure 552 Front chassis harness diagram ...
Page 270: ... 7 5 4 37 6 4 5 4 261 Figure 553 Rear chassis harness diagram ...
Page 271: ...262 4 5 4 7 5 4 37 6 5 0 4 45 3 Figure 554 POWERPLUS 100 engine ignition system ...
Page 296: ... 7 5 4 37 6 44 3 8 4 287 Figure 582 Engine assembly ...
Page 299: ...290 05 4 7 5 4 37 6 ...
Page 305: ...296 05 4 7 5 4 37 6 ...