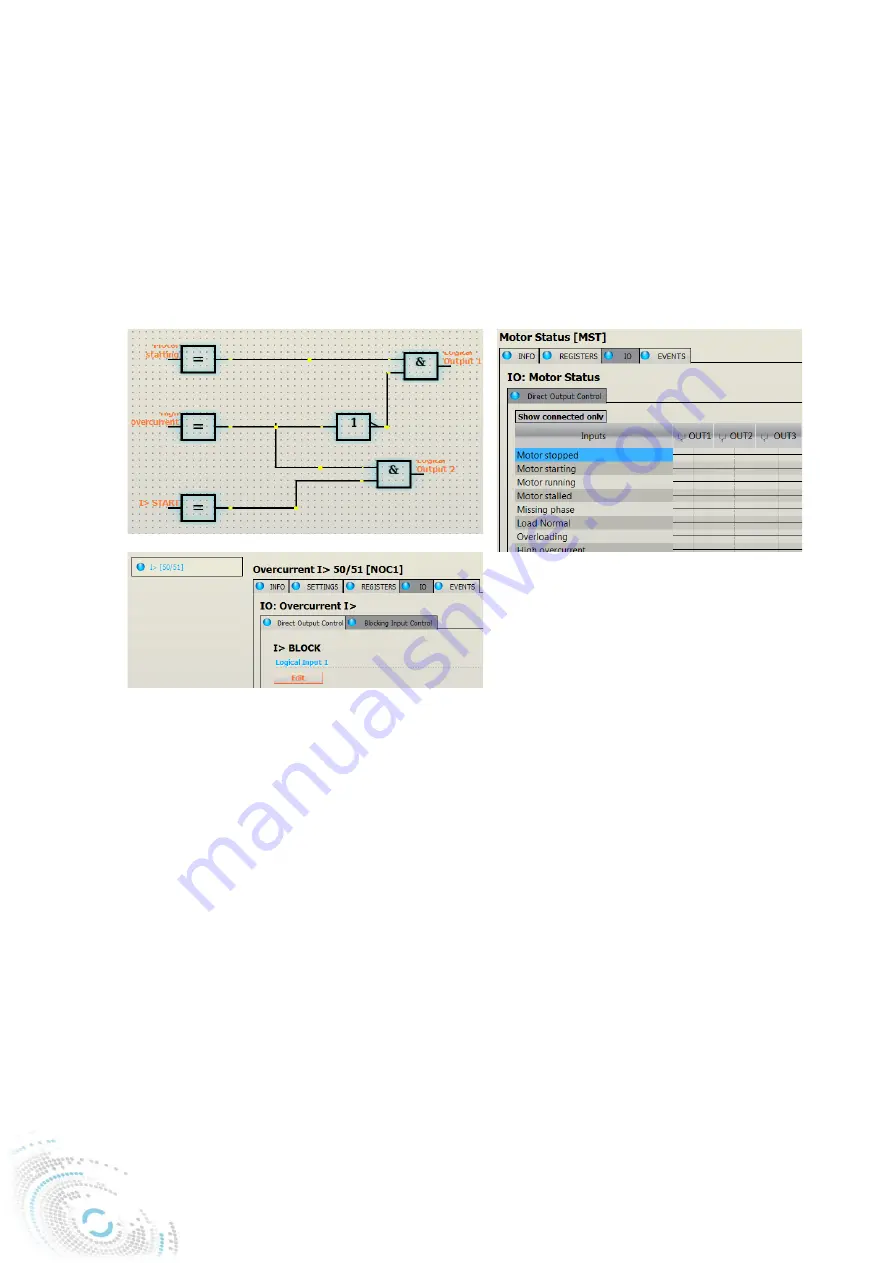
Application Guide - NP900 Series
220 (504
)
A996A
Problem in this example application may be that if during the start-up of the motor, short
circuit fault occurs in cases when the overcurrent stage is blocked it may prolong the fault
clearing time since the relay is considering this situation still as starting. For this purpose
following logic can be used to prevent the prolongation of the fault clearing time during
startup of the motor. Benefit of this logic is that there is no need to spend another
protection stage for short circuit faults since the one stage set below the starting current of
the motor can be used for short circuits and also overcurrent faults.
Figure 3.3.1-103 Motor start up overcurrent control logic.
Picture 1. In the start-up situation MST_MOTSTART signal is connected to LOGIC_OUT1
signal with “AND” gate to “NOT” high overcurrent detect in the MST function. When motor
is started I> stage is blocked, if high overcurrent is detected during the startup the
blocking is released. If wanted the high overcurrent detect can be combined with I>
(NOC1) start signal to “AND” and use for example LOGIC_OUT2 to change the active
setting group of I> function to instant operating.
Picture 2. This LOGIC_OUT1 signal is connected to I> blocking input (NOC1, first stage
overcurrent) function to block the stage in motor start-ups.
Picture 3. High overcurrent detect signal can also be directly connected to output relay.
With this application there is no need for extra logics for the fault clearing control and the
fault clearing is very fast.
In addition to this application suggestion there is possible also to just release the tripping
of I> stage when the high overcurrent is detected and let the overcurrent function to