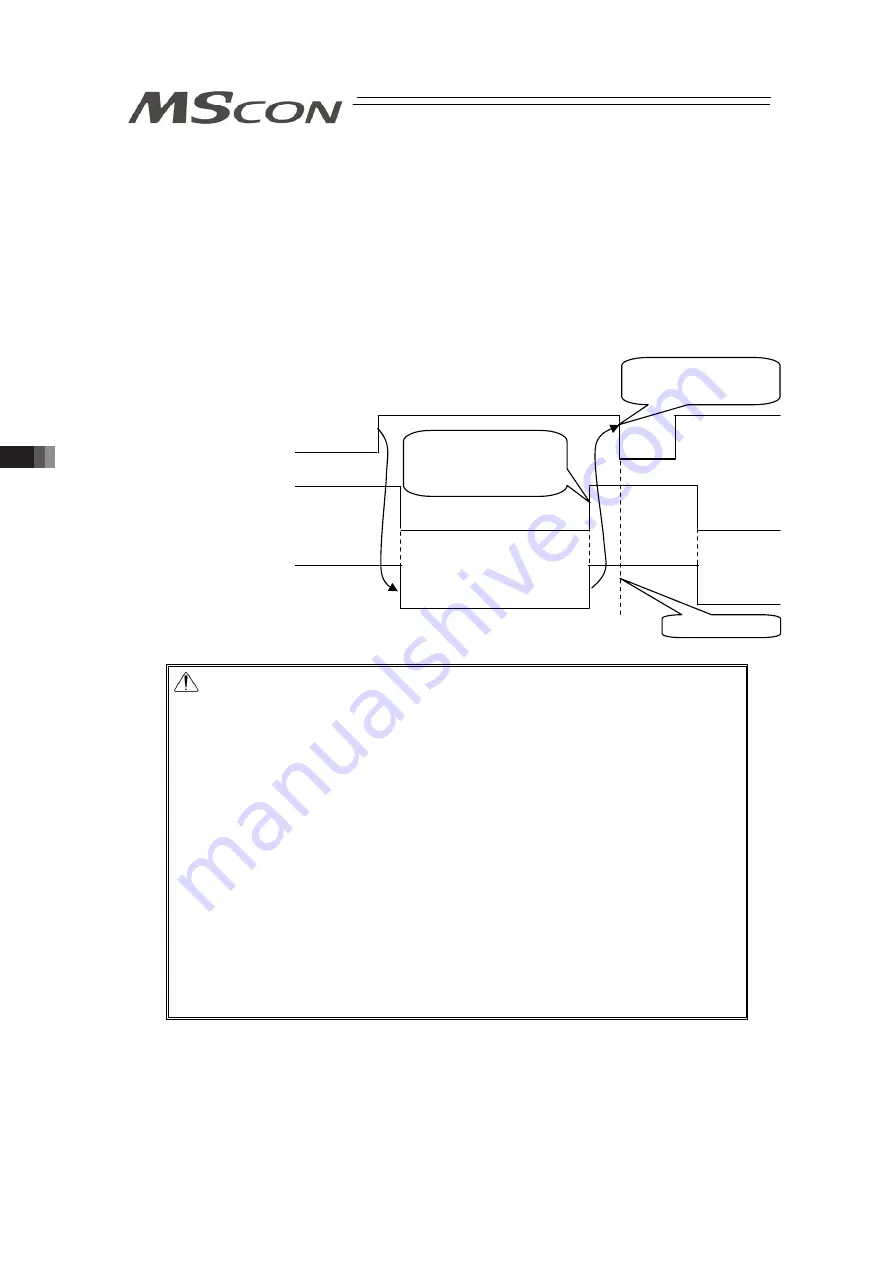
3.8 Control and functions of Input and output signals of Remote I/O Mode
198
Control method
1) When start signal ST* is turned ON, the actuator starts acceleration based on the data in the
specified position table for positioning to the target position.
2) At the completion of positioning, positioning complete signal PEND is turned ON as well as
current position No. PE* of the specified position.
3) After PEND is turned ON, turn the ST* signal OFF.
4) Current position No. PE* and positioning completion signal PEND are turned ON if the
remaining moving distance is entered into the positioning width zone. PE* and PEND turned
ON once remain ON unless start signal ST* is turned ON again or the servo is turned OFF.
They are also turned OFF when pause signal *STP is turned OFF.
Caution: (1) If the ST* signal is turned ON for the position after completion of
positioning, both the PE* and PEND signals remain ON (except the
pitch feed operation).
(2) Both the PE* and PEND signals are set to ON in the positioning
width zone. Accordingly, they may be turned ON under operation of
the actuator if a large positioning width is set.
(3) Interlock should be taken so that two or more ST* signals are set to
ON simultaneously
.
1) Entering the ST* signal of another position during positioning is
invalid. If the ST* signal of another position is turned ON during
positioning, the operation is terminated after the completion of
the positioning being operated.
2) Entering the ST* signal of another position with the ST* signal of
the current position remaining ON after the completion of
positioning allows the positioning to the other position to be
executed.
(4) If Parameter No.27 “Move command type” is set to “0” (factory
setting), turning ST* OFF during positioning caused the operation to
be interrupted.
Start signal
ST*
(PLC
→
MSCON)
Positioning Completion Signal
PEND
(MSCON
→
PLC)
Turned ON after
entering into
positioning width zone
Target Position
Current Position No.
PE*
(MSCON
→
PLC)
Turned OFF by
turning PEND ON
ME0306-2A
Summary of Contents for MSCON
Page 1: ...MSCON Controller Instruction Manual Second Edition ...
Page 2: ......
Page 4: ...ME0306 2A ...
Page 8: ...ME0306 2A ...
Page 20: ...12 ME0306 2A ...
Page 28: ...20 ME0306 2A ...
Page 46: ...Chapter 1 Specifications Check 38 ME0306 2A ...
Page 240: ...3 11 Gateway status LED 232 ME0306 2A ...
Page 246: ...Chapter 4 Vibration Suppress Control Function 238 ME0306 2A ...
Page 290: ...Chapter 7 Parameter 282 ME0306 2A ...
Page 310: ...Chapter 8 Troubleshooting 302 ME0306 2A ...
Page 354: ...Chapter 9 Appendix 346 ME0306 2A ...
Page 358: ......
Page 359: ......