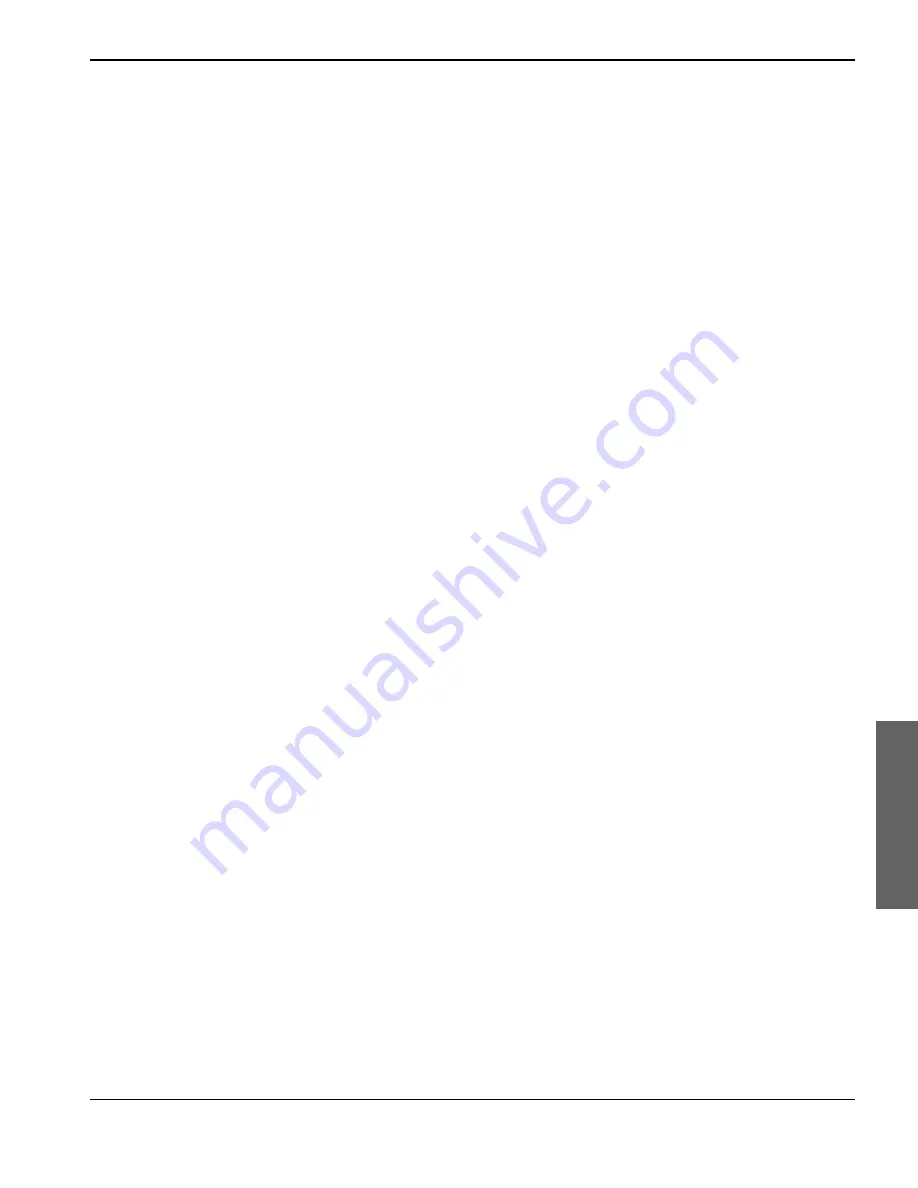
HyPrecision15/30/50
Operator
Manual 808240
155
7 – Troubleshooting
Tr
oubleshoo
ti
ng
Intensifier
Stroking problems
It is normal for the intensifier to stroke faster during startup and when changing from pierce-pressure mode to
cut-pressure mode.
The motor’s wattage and the size of the hydraulic pump determine the maximum intensifier stroke rate.
If the intensifier does not stroke to either side, check these possible causes.
Make sure that the intensifier is enabled. Refer to page 57 for instructions for disabling and enabling the intensifier.
Make sure that the cutting head is turned on.
Look at the proximity switch lights. If both lights are on at the same time, a proximity switch might have failed, an
indicator spring might be broken, or an indicator pin might be stuck. Inspect all parts to determine the cause of the
fault.
Check the cord ends on the proximity switches for damage.
Make sure that the indicator pins and springs are not damaged.
If the intensifier strokes to 1 side and then stalls on the same side, check these items.
Trade the proximity switches (but not the wires).
Replace the proximity switches.
Check the indicator pin for burrs. The pins should move freely to the bottom of the bore.
Make sure that the indicator pin springs are not broken and that they are the same length.
While the pump is in cooling mode, push on the shift pin on the stalled side.
The shift pin is found at the ends of the coil on the pilot valve. If the intensifier strokes to other side, the problem
is electrical. If the intensifier does not move, the problem is mechanical.
If the intensifier strokes but there is not enough pressure at the cutting head, check these items.
Replace the water filter.
Repair or replace the thimble filter for the on/off valve.
Make sure that there is not an obstruction in the high-pressure tubing.
The hydraulic piston seals could be worn. Contact Hypertherm Technical Service for support.
If a high-pressure cylinder is hot, disassemble it and look for flaws, deterioration, erosion marks, or cracks in the
parts, including the check valve and piston seal.
If an output adapter is hot, check the high-pressure poppet and the high-pressure seat.
If the bleed-down valve is hot or if water is coming out of the pump drain line, repair the bleed-down valve.
Make sure that the number of orifices and their sizes are sufficient for the pump’s output.
Summary of Contents for HyPrecision 15
Page 1: ...HyPrecision15 30 50 Waterjet Pump Operator Manual 808240 Revision 1 English ...
Page 10: ...10 HyPrecision15 30 50 Operator Manual 808240 Pump information Pump information ...
Page 12: ...SC 12 Safety and compliance Warranty Warranty ...
Page 16: ...SC 16 Safety and compliance Product stewardship Product stewardship ...
Page 18: ...SC 18 Safety and compliance Environmental stewardship Environmental stewardship ...
Page 24: ...SC 24 Safety and compliance Symbols and marks Symbols and marks ...
Page 28: ...28 HyPrecision15 30 50 Operator Manual 808240 Terminology Terminology ...
Page 44: ...44 HyPrecision15 30 50 Operator Manual 808240 3 Options Options ...
Page 60: ...60 HyPrecision15 30 50 Operator Manual 808240 4 Operation Operation ...
Page 152: ...152 HyPrecision15 30 50 Operator Manual 808240 6 Parts lists Parts lists ...
Page 176: ...176 HyPrecision15 30 50 Operator Manual 808240 8 Pump specifications Pump specifications ...
Page 194: ...194 HyPrecision15 30 50 Operator Manual 808240 9 Installation Installation ...