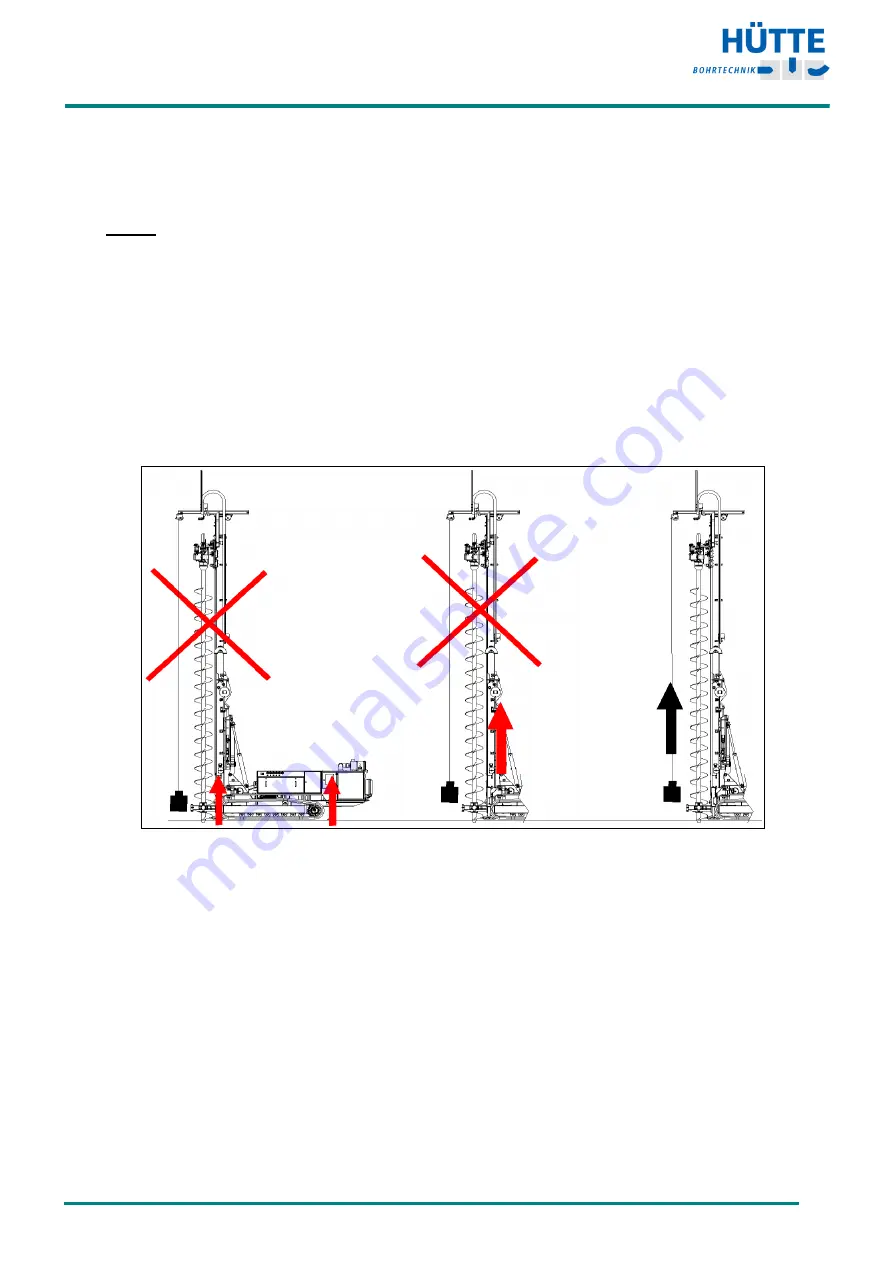
18
TECHNICAL CHARACTERISTICS
Winch
HBR204-MU-6-eng.doc
OPERATION AND MAINTENANCE INSTRUCTION MANUAL
THIS DOCUMENT IS THE PROPERTY OF HÜETTE BOHRTECHNIK GMBH - TOTAL OR PARTIAL REPRODUCTION IS PROHIBITED
LIMITS OF USE OF WINCH
Winch
The lifting of a load applied to the winch rope must never make use of the mast joint, the
stabilizers or the mast where the winch is installed; in this case the pressure relief valve may
not be able to protect the winch from very dangerous overloads.
Tampering with the pressure relief valve for loads in excess of those allowed is prohibited.
Winch may not be used for the direct or indirect transport or lifting of persons.
It is forbidden to carry out any lifting operations liable to cause risks to, first and foremost, the
safety of workers, and, secondly, to the vehicles and equipment connected with the lifting
operations.
2.2.3