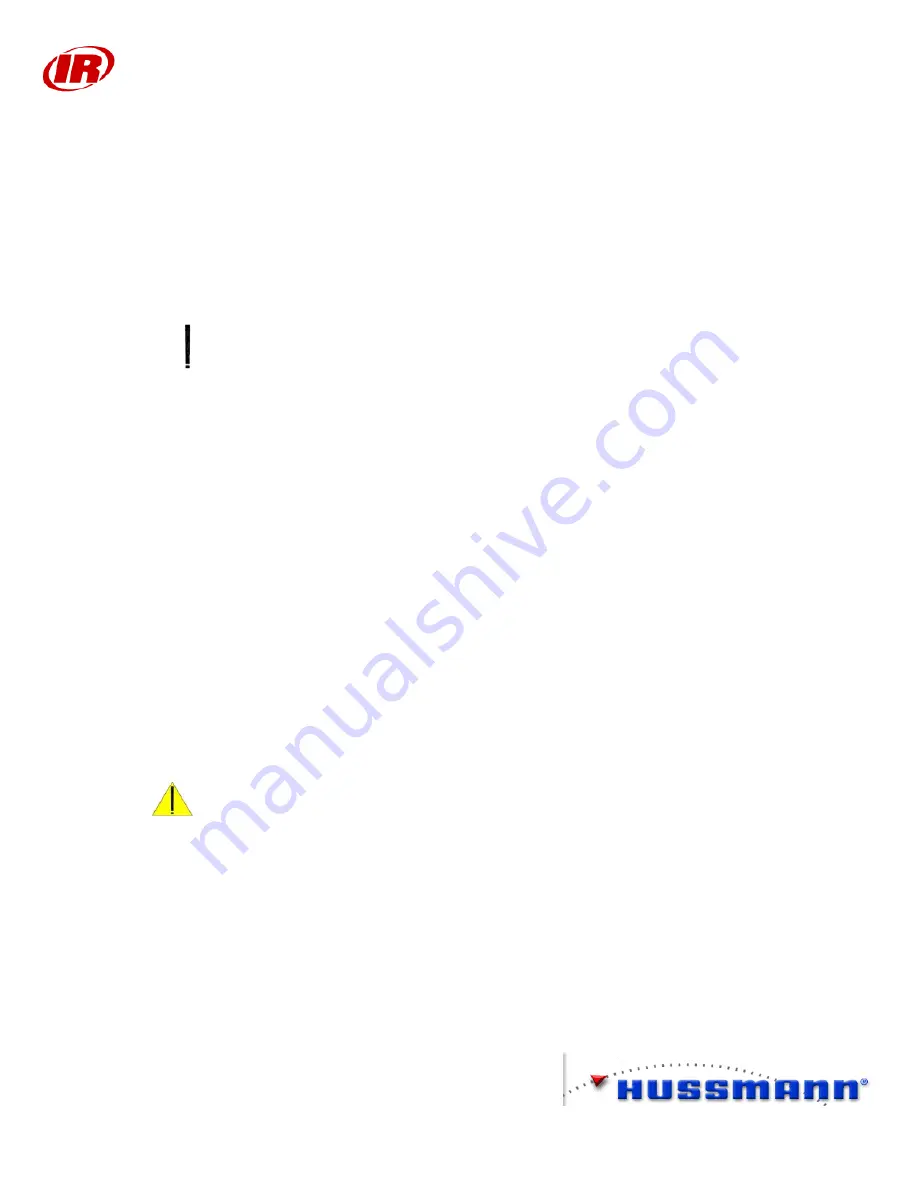
Installation and Start-up
6
For the electrical part of the installation, verify the following installed components match
those listed in the Electrical section of this manual.
1. Wire sizes to handle the connected load
2. Circuit breaker size
3. Contactor
size
4. Control circuit wiring, including high pressure safety controls, low pressure
controls, and oil failure controls
5. Motor protection devices
Attention!
The terminals 1-2/3-4/B1-B2 on the compressor and motor protection
device must not come into contact with supply or control voltage.
Installation – Refrigerant Piping
Great care should be taken to ensure the refrigeration piping is kept clean and dry prior to
installation. The following procedures should be followed:
1. Do not leave dehydrated compressors, filter dryers, or refrigerant lines open to
the atmosphere any longer than absolutely necessary.
2. Use only refrigerant grade tubing.
3. Suction lines should slope towards the compressor ½” per 10 feet
4. Suitable p-traps should be located at the base of suction risers to enhance oil
return.
5. Suction line risers should be sized to provide adequate velocity for oil return,
and in certain instances double risers may be required. Consult either the
equipment manufacturers recommendations, or ASHRAE refrigeration piping
guidelines.
6. When brazing copper lines, nitrogen (or suitable inert gas) should be passed
through the lines at low pressure to prevent scaling and oxidation inside the
tubing. This is especially critical when using HFC refrigerants with POE oils.
Warning!
Always use a pressure regulator with a nitrogen tank
. Do not
exceed two psi and vent lines when brazing. Do not exceed 350 psi for leak
testing the high side of the system, or 150 psi for leak testing the low side of the
system.
7. Joints should be brazed with a silver alloy brazing material, use a minimum of
35% silver solder for joints that contain dissimilar metals.
8. When brazing compressor service valves, care should be taken to not
overheat the valves. The maximum brazing temperature is 1292
q
F.
Summary of Contents for Ingersoll Rand
Page 2: ......
Page 6: ......
Page 191: ...Dimensions 1...
Page 192: ...Dimensions 2...
Page 193: ...Dimensions 3...
Page 194: ...Dimensions 4...
Page 212: ...Electrical Data 12 Control Circuit Wiring Schematics Figure 1 Motor protector SE B1 shown...
Page 213: ...Electrical Data 13 Figure 2 Motor protector SE B2 shown...
Page 214: ...Electrical Data 14 Figure 3 Motor protector and oil failure control module INT69 70 shown...
Page 215: ...Mechanical Design 1 Ingersoll Rand Impact Semi Hermetic Reciprocating Compressors...
Page 260: ......
Page 265: ...Aftermarket 5 IR Impact Compressor 4 hour Distribution Map...
Page 285: ...Aftermarket 25 Compressor Exploded View IR2C0173 to IR4C1385...
Page 286: ...Aftermarket 26 Compressor Optional Heads Exploded View IR2C0173 to IR4C1385...
Page 287: ...Aftermarket 27 Compressor Exploded View IR4C1480 to IR4C2397...
Page 288: ...Aftermarket 28 Compressor Optional Heads Exploded View IR4C1480 to IR4C2397...
Page 289: ...Aftermarket 29 Compressor Exploded View IR4B2707 to IR6B6462...
Page 290: ...Aftermarket 30 Compressor Optional Heads Exploded View IR4B2707 to IR6B6462...
Page 291: ...Aftermarket 31 Compressor Exploded View IR8C7863 to IR8C9400...
Page 292: ...Aftermarket 32 Compressor CR Head Exploded View IR8C7863 to IR8C9400...
Page 297: ...Aftermarket 37...
Page 299: ......
Page 308: ......
Page 328: ......