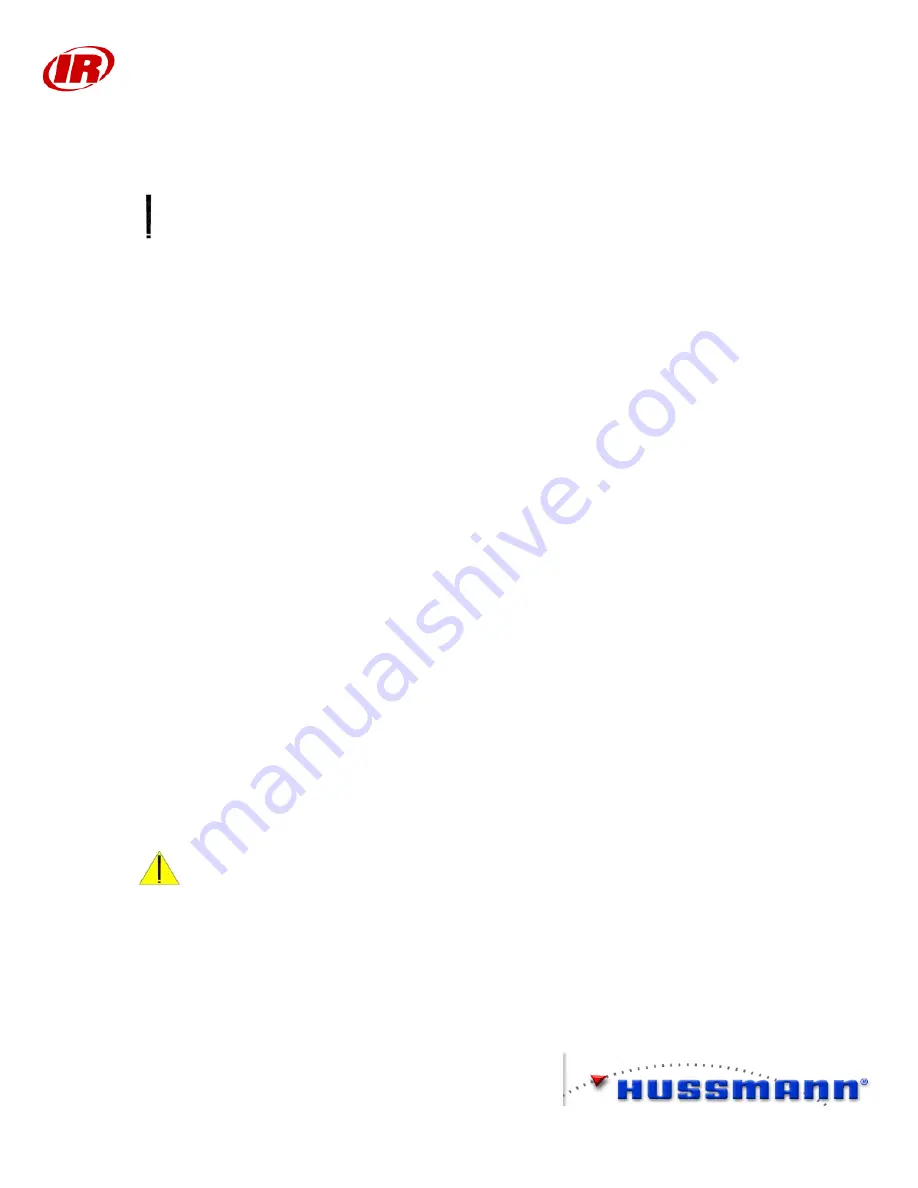
Installation and Start-up
8
Evacuation
Attention!
Nitrogen and moisture will remain in the system unless proper evacuation
procedures are followed. Nitrogen left in the system may cause excessive discharge
pressure problems. Moisture causes TEV ice blockage, wax build up, acid oil, and
sludge formation.
Do not
simply purge the system, this method is expensive, harmful
to the environment, may leave moisture and nitrogen in the system, and may result in
fines or penalties from the EPA.
Do not
run the compressor to evacuate the system. This
procedure introduces moisture into the compressor’s crankcase oil and does not produce
adequate vacuum levels to remove moisture from the system.
1. Using all copper lines or high vacuum hoses and packless isolation valves,
connect a vacuum pump with adequately sized lines to the refrigeration
system piping. The vacuum pump must be in good working order and filled
with fresh oil to achieve the desired results.
2. Connect a micron vacuum gauge near the pump so it can be isolated from the
pump and still read system pressure. It is also recommended that a second
vacuum gauge be connected at the farthest point in the system from the
vacuum pump.
3. Energize the crankcase heaters, if applicable.
4. Open all compressor service valves and oil lines.
5. Turn on the vacuum pump and pull down the entire system to a vacuum level
of 1500 microns.
6. If the vacuum fails to hold, or pull down, determine the cause i.e. a leak, and
correct.
7. Break the vacuum with refrigerant vapor, to a pressure of at least 2 psig, being
careful not to exceed the micron gauges maximum pressure limit.
8. Repeat steps 5-7.
9. Install suction filters and liquid drier cores.
10. Pull a vacuum on the entire system again to a level of 500 microns or less.
11. Close all vacuum headers and valves and allow the system to stabilize for a
minimum of 12 hours.
12. If the vacuum holds, charging may begin. If the vacuum does not hold, the
cause must be determined and corrected, and repeat the entire evacuation
procedure from the beginning.
Warning!
Do not start or operate the compressor while the system is in a
vacuum. Severe damage to the compressor’s motor windings may result.
Summary of Contents for Ingersoll Rand
Page 2: ......
Page 6: ......
Page 191: ...Dimensions 1...
Page 192: ...Dimensions 2...
Page 193: ...Dimensions 3...
Page 194: ...Dimensions 4...
Page 212: ...Electrical Data 12 Control Circuit Wiring Schematics Figure 1 Motor protector SE B1 shown...
Page 213: ...Electrical Data 13 Figure 2 Motor protector SE B2 shown...
Page 214: ...Electrical Data 14 Figure 3 Motor protector and oil failure control module INT69 70 shown...
Page 215: ...Mechanical Design 1 Ingersoll Rand Impact Semi Hermetic Reciprocating Compressors...
Page 260: ......
Page 265: ...Aftermarket 5 IR Impact Compressor 4 hour Distribution Map...
Page 285: ...Aftermarket 25 Compressor Exploded View IR2C0173 to IR4C1385...
Page 286: ...Aftermarket 26 Compressor Optional Heads Exploded View IR2C0173 to IR4C1385...
Page 287: ...Aftermarket 27 Compressor Exploded View IR4C1480 to IR4C2397...
Page 288: ...Aftermarket 28 Compressor Optional Heads Exploded View IR4C1480 to IR4C2397...
Page 289: ...Aftermarket 29 Compressor Exploded View IR4B2707 to IR6B6462...
Page 290: ...Aftermarket 30 Compressor Optional Heads Exploded View IR4B2707 to IR6B6462...
Page 291: ...Aftermarket 31 Compressor Exploded View IR8C7863 to IR8C9400...
Page 292: ...Aftermarket 32 Compressor CR Head Exploded View IR8C7863 to IR8C9400...
Page 297: ...Aftermarket 37...
Page 299: ......
Page 308: ......
Page 328: ......