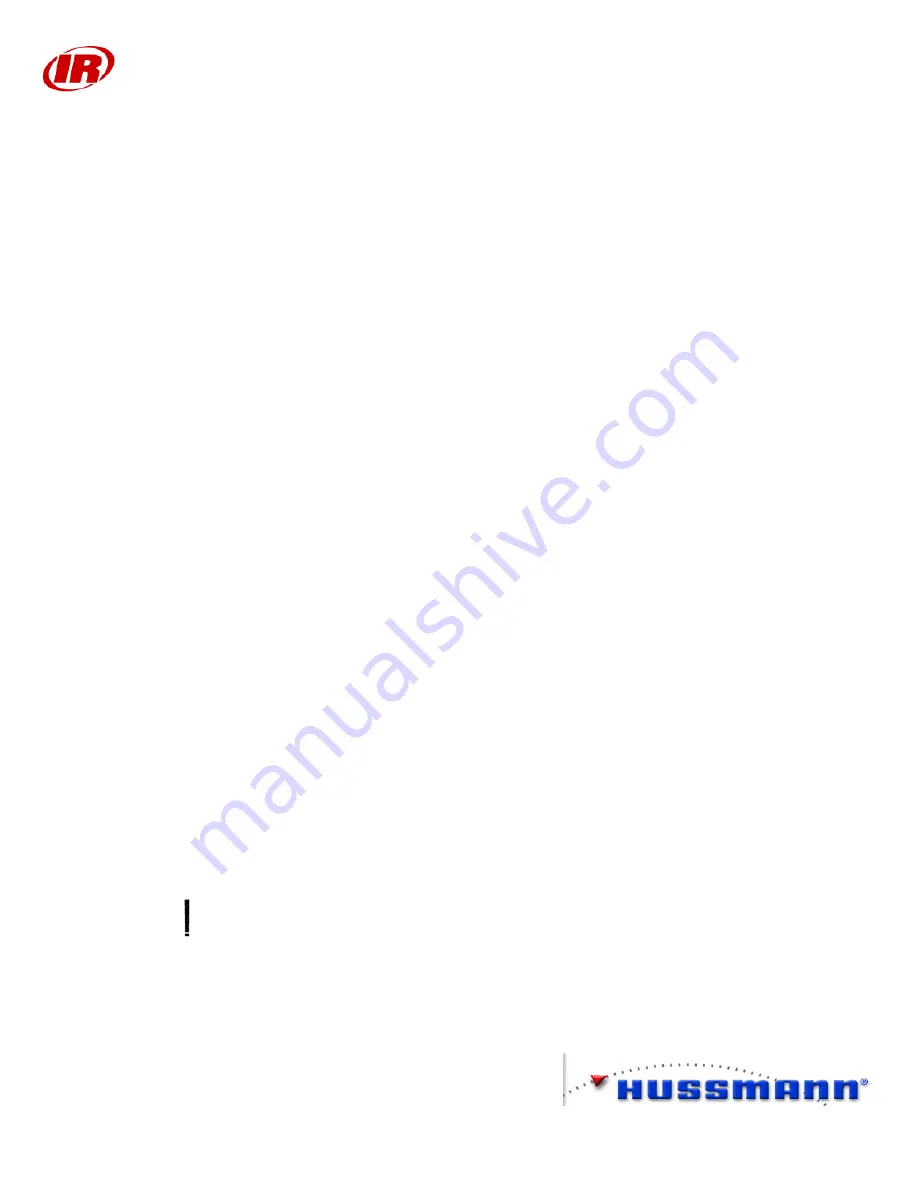
Installation and Start-up
9
Pre-Check, Charging and Start-up
After the installation, leak testing, and evacuation procedures are complete the following
items should be checked before charging the system with refrigerant:
1. Check all electrical connections to make sure they are tight.
2. Observe compressor oil levels; oil should be visible in the compressor sight
glass. If needed, pump oil into the compressor until the level is between ¼ and
¾ of the sight glass. (Note: See the lubrication section of this manual for the
proper oil type.)
3. Add oil as necessary to the oil reservoir.
4. Check high and low pressure controls, oil regulators, other safety controls, and
valves and adjust if necessary.
Charging
1. Close the ball valve immediately downstream of the receiver, and connect the
proper refrigerant to the charging access port.
2. Slowly open the liquid valve on the refrigerant tank and fill the receiver to
approximately 60%.
3. Disconnect the refrigerant tank, and open the ball valve. The liquid level
should decrease as refrigerant is drawn into the system piping.
4. The remaining refrigerant charge must be added only as vapor through the
suction access port.
5. Turn on a compressor, and continue charging through the suction side of the
system with vapor only until the receiver level is approximately 30%. (Note:
In a parallel compressor application, additional compressors may be turned on
to maintain the suction pressure to aid in the charging process.)
6. Check oil levels of each compressor continually through the charging process.
If oil needs to be added, stop the charging process add the oil, then resume
charging the refrigerant.
7. For compressors with oil pumps, check the oil pressure by means of a gauge
connected to the Schrader valves on the oil pump. Differential oil pressure
should be in the range of 20 to 50 psi, with a minimum inlet pressure
(measured on the suction side of the oil pump) of 5.8 psig.
8. Monitor the oil temperature while charging, and maintain its temperature
above 104
q
F.
Attention!
With non-azeotropic refrigerants, it is best to charge the entire
contents of the cylinder to prevent fractionalization of the refrigerant.
Summary of Contents for Ingersoll Rand
Page 2: ......
Page 6: ......
Page 191: ...Dimensions 1...
Page 192: ...Dimensions 2...
Page 193: ...Dimensions 3...
Page 194: ...Dimensions 4...
Page 212: ...Electrical Data 12 Control Circuit Wiring Schematics Figure 1 Motor protector SE B1 shown...
Page 213: ...Electrical Data 13 Figure 2 Motor protector SE B2 shown...
Page 214: ...Electrical Data 14 Figure 3 Motor protector and oil failure control module INT69 70 shown...
Page 215: ...Mechanical Design 1 Ingersoll Rand Impact Semi Hermetic Reciprocating Compressors...
Page 260: ......
Page 265: ...Aftermarket 5 IR Impact Compressor 4 hour Distribution Map...
Page 285: ...Aftermarket 25 Compressor Exploded View IR2C0173 to IR4C1385...
Page 286: ...Aftermarket 26 Compressor Optional Heads Exploded View IR2C0173 to IR4C1385...
Page 287: ...Aftermarket 27 Compressor Exploded View IR4C1480 to IR4C2397...
Page 288: ...Aftermarket 28 Compressor Optional Heads Exploded View IR4C1480 to IR4C2397...
Page 289: ...Aftermarket 29 Compressor Exploded View IR4B2707 to IR6B6462...
Page 290: ...Aftermarket 30 Compressor Optional Heads Exploded View IR4B2707 to IR6B6462...
Page 291: ...Aftermarket 31 Compressor Exploded View IR8C7863 to IR8C9400...
Page 292: ...Aftermarket 32 Compressor CR Head Exploded View IR8C7863 to IR8C9400...
Page 297: ...Aftermarket 37...
Page 299: ......
Page 308: ......
Page 328: ......