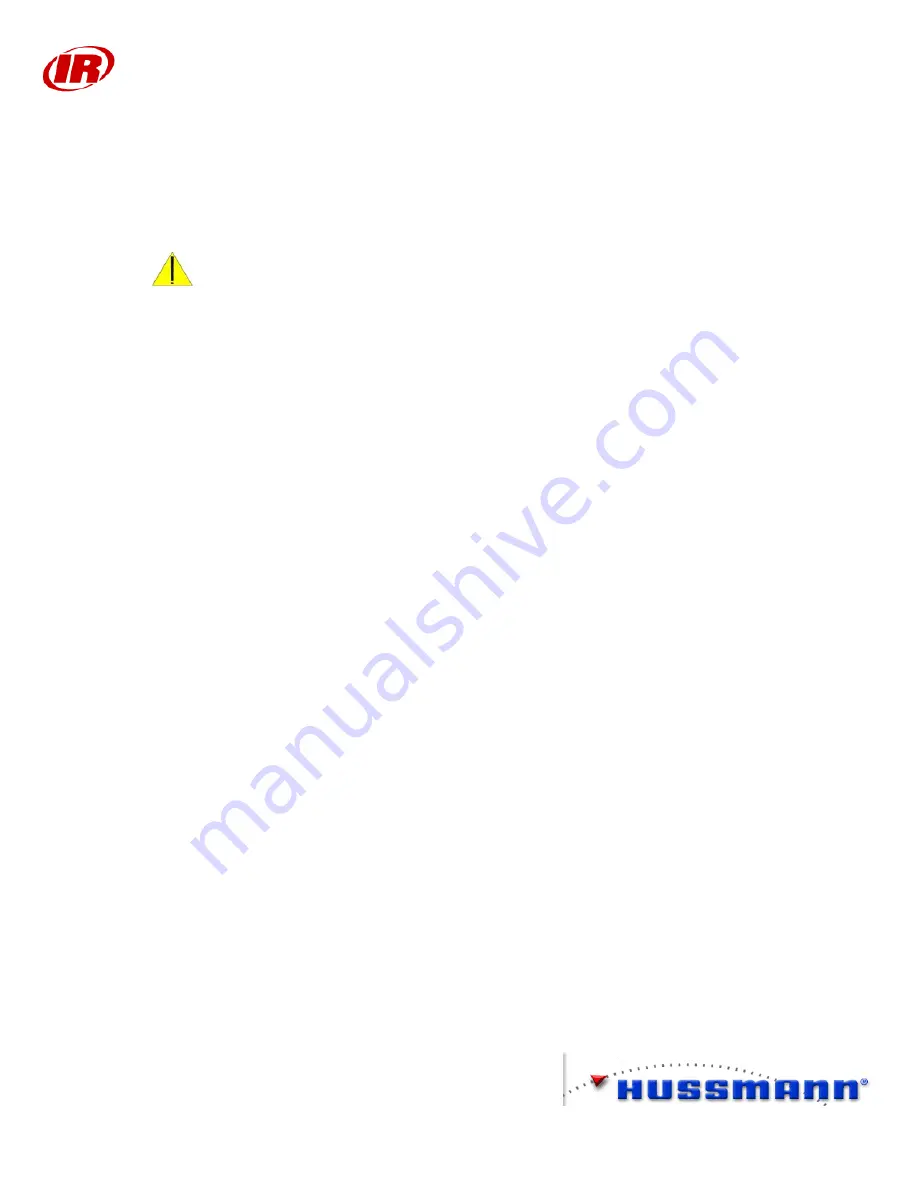
Installation and Start-up
17
Troubleshooting - Motor Burnout (Clean-up Procedure)
When a hermetic motor burns out, the stator winding decomposes forming carbon, water,
and acid, which contaminate refrigerant systems. These contaminants must be removed
from the system to prevent repeat motor failures.
Warning!
Before attempting any service work on the compressor, see safety
precautions listed on page 12 of this section. Failure to follow these instructions could
result in serious personal injury.
a. Determine cause of burnout and make any necessary corrections. Check control box
for blown fuses, welded starter contacts, welded overload contacts or burned out
heater elements. Check compressor terminal plate for burned or damaged terminals
and insulation, also check for shorted or grounded terminals. Check unit wiring for
loose power connections. Check for high or low voltage.
b. Close compressor suction and discharge service valves and bleed refrigerant from
compressor. Save remaining refrigerant in system.
c. Remove suction and discharge service valves and all other connections from the
damaged compressor. Remove damaged compressor and replace with a new
compressor. On severe motor burnouts, be sure shut-off valves and suction or
discharge lines are not contaminated. If they are, they should be thoroughly cleaned
or replaced before connecting to replacement compressor.
d. Install new liquid line filter-drier and if the system has a suction line filter-drier, also
replace that core.
e. Evacuate and dehydrate replacement compressor and check to see that oil in
compressor is at proper level.
f. Place compressor in operation. After 2-4 hours of operation, check compressor oil for
discoloration and/or acidity. If oil shows signs of contamination, replace oil charge,
replace filter-driers, and clean suction strainer.
g. Check oil daily for discoloration and acidity. If oil stays clean and acid-free, the
system is clean. If oil shows signs of contamination, change oil, change filter-drier,
and clean suction strainer. If filter-drier or strainer is dirty or discolored, repeat this
step until system is cleaned.
Summary of Contents for Ingersoll Rand
Page 2: ......
Page 6: ......
Page 191: ...Dimensions 1...
Page 192: ...Dimensions 2...
Page 193: ...Dimensions 3...
Page 194: ...Dimensions 4...
Page 212: ...Electrical Data 12 Control Circuit Wiring Schematics Figure 1 Motor protector SE B1 shown...
Page 213: ...Electrical Data 13 Figure 2 Motor protector SE B2 shown...
Page 214: ...Electrical Data 14 Figure 3 Motor protector and oil failure control module INT69 70 shown...
Page 215: ...Mechanical Design 1 Ingersoll Rand Impact Semi Hermetic Reciprocating Compressors...
Page 260: ......
Page 265: ...Aftermarket 5 IR Impact Compressor 4 hour Distribution Map...
Page 285: ...Aftermarket 25 Compressor Exploded View IR2C0173 to IR4C1385...
Page 286: ...Aftermarket 26 Compressor Optional Heads Exploded View IR2C0173 to IR4C1385...
Page 287: ...Aftermarket 27 Compressor Exploded View IR4C1480 to IR4C2397...
Page 288: ...Aftermarket 28 Compressor Optional Heads Exploded View IR4C1480 to IR4C2397...
Page 289: ...Aftermarket 29 Compressor Exploded View IR4B2707 to IR6B6462...
Page 290: ...Aftermarket 30 Compressor Optional Heads Exploded View IR4B2707 to IR6B6462...
Page 291: ...Aftermarket 31 Compressor Exploded View IR8C7863 to IR8C9400...
Page 292: ...Aftermarket 32 Compressor CR Head Exploded View IR8C7863 to IR8C9400...
Page 297: ...Aftermarket 37...
Page 299: ......
Page 308: ......
Page 328: ......